First metal 3D printed bicycle frame manufactured by Renishaw for Empire Cycles
Renishaw, the UK's only manufacturer of a metal-based additive manufacturing machine that prints metal parts, has collaborated with a leading British bicycle design and manufacturing company to create the world's first 3D printed metal bike frame.
Empire Cycles
Empire Cycles is a unique British bike designing and manufacturing company in the North-West of England. Passionate about using great British engineering to create elite products, the Company offers innovative designs to the world's mountain bikers and downhillers. By working together, Renishaw and Empire Cycles optimised the bicycle design for additive manufacture, eliminating many of the downward facing surfaces that would otherwise have needed wasteful support structures.
Empire Cycles designed the mountain bike to take advantage of Renishaw's additive manufacturing technology, allowing them to create a titanium frame that would be both strong and light using topological optimisation - the new frame is some 33% lighter than the original. The frame has been additively manufactured in titanium alloy in sections and bonded together. This offers a number of advantages:
Design freedom
- Rapid iterations; flexibility to make design improvements right up to production
- Ability to make shapes derived by topological optimisation
- Ultimate customisation and tailoring - make one-offs as easily as production batches
Construction
- Complex shape with internal strengthening features
- Hollow structures
- Built in features, such as the rider's name
Performance, titanium alloy
- Seat post bracket 44% lighter than aluminium alloy version
- Extremely strong - tested to EN 14766
- Corrosion resistant and long lasting
What is topological optimisation?
From the Greek word for place, "topo", topological optimisation software is the term given to programs that are used to determine the "logical place" for material – normally using iterative steps and finite element analysis. Material is removed from areas of low stress until a design optimised for load bearing is evolved. The resulting model is both light (due to the low volume) and strong. The historical challenge in manufacturing these shapes can now be overcome with additive manufacturing, enabling physical 3D models to be realised. By working together, Renishaw and Empire Cycles optimised the bicycle design for additive manufacture, eliminating many of the downward facing surfaces that would otherwise have needed wasteful support structures.
How strong is it?
Titanium alloys have a high Ultimate Tensile Strength (UTS) of more than 900 MPa when processed using additive manufacturing and near perfect densities of greater than 99.7% are achieved; this is better than casting and, as any porosity is both small and spherical, it has little effect on strength. The project's aim is to produce a fully functioning bicycle, so the seat post bracket was tested using the mountain bike standard EN 14766; it withstood 50000 cycles of 1200 N. Testing continued to six times the standard without failure. Testing of the completed bicycle frame will continue, both in the laboratory using Bureau Veritas UK, and on the mountainside using portable sensors in partnership with Swansea University.
Empire Cycles (UK)
How light is it?
The entire bike frame was arranged in sections with the seat post bracket on one build plate and fabricated in one go. Titanium alloys are more dense than aluminium alloys, with relative densities of around 4 g/cm3 and 3 g/cm3 respectively. Therefore, the only way to make a titanium alloy version of a part lighter than its aluminium alloy counterpart is to significantly alter the design to remove any material not contributing to the overall strength of the part.
The original aluminium alloy seat post bracket is 360 g and the hollow titanium version is 200 g, a weight saving of 44%. This is just the first iteration; with further analysis and testing it could be reduced further. The original bike frame weighs in at 2100 g. Redesigned to make use of additive manufacturing, the weight drops to 1400 g, a 33% weight saving.
There are lighter carbon fibre bikes available, but Chris Williams, Managing Director at Empire Cycles, has researched this already and says, “The durability of carbon fibre can't compare to a metal bike, they are great for road bikes, but when you start chucking yourself down a mountain you risk damaging the frame. I over-engineer my bikes to ensure there are no warranty claims”.
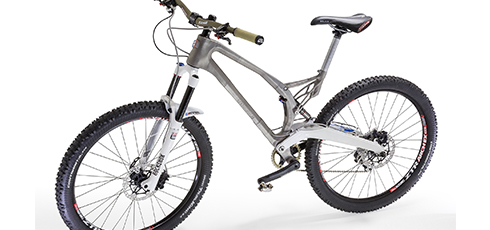
How was the project managed?
Chris had already produced a full size 3D printed replica of his current bike before he approached Renishaw, so had a good idea of what he wanted to achieve. Renishaw originally agreed to optimise and manufacture the seat post bracket only, but after this proved successful, decided the whole frame was a practical goal. Chris updated his design with guidance from Renishaw's applications team on what would build well, and the frame was sectioned so that it would fully utilise the AM250's 300 mm build height.
The key benefit for Empire Cycles is the performance advantages that this construction method bestows. The design has all of the advantages of a pressed steel ‘monocoque' construction used in motorbikes and cars, without the investment in tooling that would be prohibitive for a small manufacturer. The potential performance has not been completely explored yet, but we hope to continue to develop the project. As no tooling is required, continual design improvements can be made easily; and as the component cost is based on volume and not complexity, some very light parts will be possible at minimal costs.
Research into bonding methods resulted in Mouldlife providing the adhesive, and technical specialists 3M providing test facilities. We will develop this further in partnership to look at iterative improvements in bonding methods, such as specific surface finishes. The wheels, drive train and components required to finish the bike were provided by Hope Technology Ltd. This project has highlighted that excellent results can be achieved by working closely with the customer. If you have a component that would benefit from additive manufacture please contact your local Renishaw office for further information.