Equator™ gauging systems for industrial manufacturing
The Equator gauging systems enable process control by delivering highly repeatable, thermally insensitive, versatile and reprogrammable gauging to the shop floor.
Shop floor gauging for industrial manufacturing
To control manufacturing processes on the shop floor, traditional gauges like callipers, go/no-go gauges or bore gauges have been used for decades. However, modern manufacturing requires high-speed operations, consistent measurement and adaptability to fast changing needs that gauges cannot deliver.
Equator gauging systems are high-speed gauges designed to provide speed, repeatability and ease of use for manual or automated applications in medium or high-volume manufacturing shop floors; which is why hundreds of manufacturers worldwide continue to replace their current gauging method with Equator systems.
Equator systems can be configured with hardware, software and accessory options to optimise manufacturing process and specific application, whether for manual or automated operations.
- Fast and efficient to keep up with production lines and reduce scrap
- Highly repeatable and accurate
- Thermally insensitive and designed for the shopfloor
- Versatile and reprogrammable
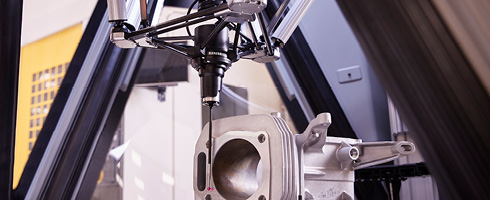
The new Renishaw Equator-X dual-method gauge delivers ultra-high speed inspection on the shop floor. It offers both absolute and comparator capability.
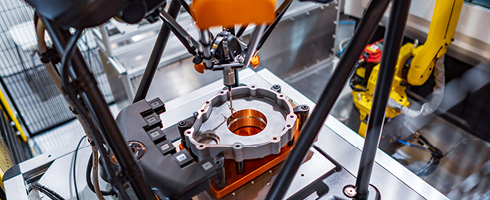
Renishaw's Equator comparator gauging systems are fast and highly repeatable systems designed for automated comparison of production parts to a reference master part.
The new Equator-X™ dual-method gauging system
Two systems in one: the absolute measurement of a CMM, the comparator performance of a versatile gauge
Instant access to information and support for our gauging customers
Unlock the power of your data with Renishaw Central
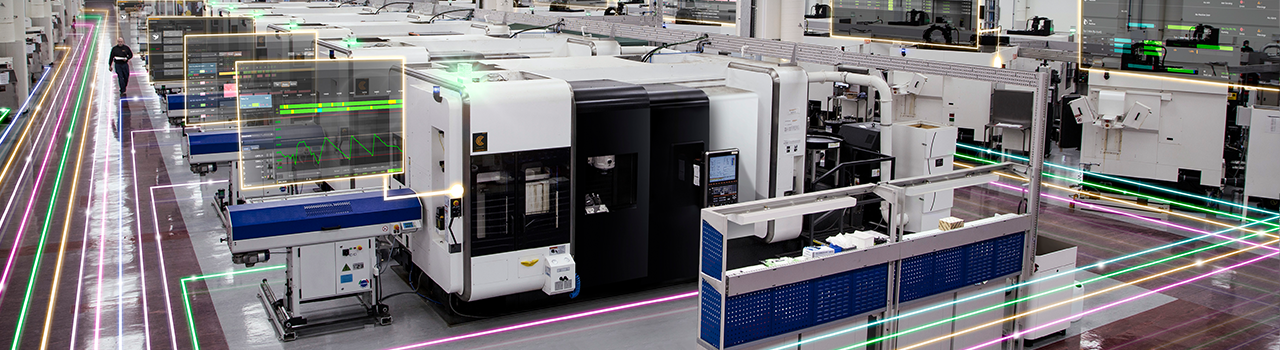
Take advantage of your CMM metrology data with our smart manufacturing data platform, Renishaw Central. Discover how our powerful platform can transform your manufacturing today.
Contact your local office
Get in touch with your local office to find out more information and speak to an expert.