Produttore di biciclette customizzate scopre i vantaggi dell’additive manufacturing.
I componenti realizzati a mano per le biciclette in titanio hanno una qualità molto alta ed è difficile eguagliarne le caratteristiche poiché sono richieste abilità consolidate nel tempo. Angel Cycle Works ha sfidato Optimus3D a implementare un tipo di produzione additiva in metallo (AM) in grado di fabbricare, in piccole serie, un componente del fodero orizzontale mantenendo uno standard qualitativo perfettamente uniforme.
Background
Optimus3D è specializzata in produzione additiva e fornisce un servizio a 360° rivolto ad aziende appartenenti ai più svariati settori manifatturieri, tra cui quello aerospaziale, automobilistico e medicale. L’azienda offre soluzioni end-to-end, che comprendono la progettazione di componenti, la produzione di prototipi e lotti, la post-lavorazione e i controlli metrologici.
Situata nel Parco tecnologico di Álava a Vitoria-Gasteiz, nel nord della Spagna, l'azienda serve clienti internazionali e locali, dando loro accesso all'ultima generazione di macchine e software per la stampa 3D. L’esperienza pluriennale dell’azienda nella produzione additiva permette di ridurre la complessità, il peso e il costo dei componenti, aumentandone inoltre la qualità e l'affidabilità.
L'azienda spagnola Angel Cycle Works è un produttore di telai e componenti per biciclette conosciuto a livello internazionale. La società realizza telai e componenti in titanio a mano e su misura e produce biciclette ad alte prestazioni per tutti i tipi di terreno.
Dal momento che Angel Cycle Works fabbricava un componente ultraresistente di alta qualità in piccole serie saldandolo a mano, è stata spinta a valutare l’alternativa della stampa 3D in metallo e, a tale scopo, si è rivolta a Optimus3D.
Pablo Capellan, Project Leader di Optimus3D ha dichiarato: “La nostra esperienza nella stampa 3D in metallo è dovuta in gran parte alla profonda conoscenza che abbiamo nell'ingegneria di produzione e nel reverse engineering. Questo significa che riusciamo ad adattare più facilmente il processo di stampa 3D ai fabbisogni del cliente, sfruttando appieno le potenzialità dell'additive manufacturing (AM).”
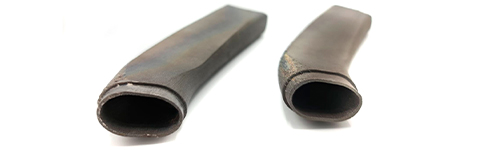
Componente in titanio del fodero stampato in 3D su sistema RenAM 500S
La nostra idea era piuttosto semplice. Producendo il componente in orizzontale, potevamo ridurre al minimo il tempo di produzione del lotto specifico e aiutare la Angel Cycle Works a raggiungere i propri obiettivi di produzione. Questo significava anche che saremmo stati in grado di misurare e gestire meglio l’eventuale deformazione, dato che il componente del fodero è lungo e sottile e misura 35 mm x 20 mm x 115 mm”.
Optimus3D (Spagna)
Confronto tra un componente del fodero saldato a mano e uno prodotto in 3D
La sfida
“La vera sfida per Angel Cycle Works nel produrre manualmente il componente in titanio del fodero è legata essenzialmente al tipo di metallo. Sicuramente, non è il metallo più facile da lavorare. Soprattutto durante la saldatura a mano, possono verificarsi deformazioni del componente, per cui rimanere perfettamente fedeli a un modello CAD tridimensionale può risultare davvero molto difficile.”
Capellan ha continuato: “Anche quando abbiamo a che fare con il procedimento di stampa 3D, sia se ottenuto fondendo il metallo strato su strato sia mediante deposizione lungo un tracciato, il titanio può comunque presentare delle sfide impegnative.”
Altro fattore chiave per Optimus3D, per produrre il componente in quantità elevate, è stato portare al massimo la produttività del processo di AM. Al fine di ottenere la massima redditività del processo, non solo era necessaria l'assoluta precisione e affidabilità del pezzo finito, ma anche che ogni camera di lavorazione producesse il più alto numero di componenti possibili.
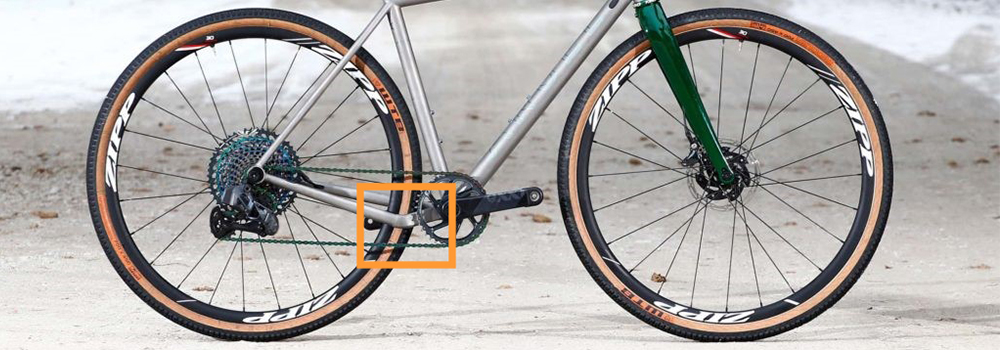
Nel riquadro arancione, posizione del componente prodotto in titanio
Soluzione
Optimus3D ha proposto l'utilizzo del suo sistema di produzione additiva a laser singolo Renishaw RenAM 500S. Il macchinario è progettato per la costruzione di componenti metallici utilizzando la fusione laser su letto di polvere e dispone di una camera di lavorazione che misura 250 mm x 250 mm x 350 mm.
L'atmosfera inerte generata dal sistema Renishaw, un vuoto riempito con gas argon ad alta purezza, garantisce un ambiente di lavorazione di altissima qualità per tutti i metalli qualificati, compreso il titanio Ti6AI4V usato in quest’applicazione.
Considerando la struttura e le dimensioni del componente, la costruzione in senso verticale sarebbe stata la scelta più ovvia. Tuttavia, consapevole del potenziale problema di deformazione e della necessità di massimizzare la produttività, Optimus3D ha scelto di costruire in senso orizzontale.
Capellan ha spiegato: “La nostra idea era piuttosto semplice. Producendo il componente in orizzontale, potevamo ridurre al minimo il tempo di produzione del lotto specifico e aiutare la Angel Cycle Works a raggiungere i propri obiettivi di produzione. Questo significava anche che saremmo stati in grado di misurare e gestire meglio l’eventuale deformazione, dato che il componente del fodero è lungo e sottile e misura 35 mm x 20 mm x 115 mm”.
“Come previsto, la stampa del componente in senso orizzontale, direttamente dal file CAD, ha prodotto nell’area più vulnerabile, una distorsione fuori tolleranza di 0,375 mm. Per eliminare questo errore, abbiamo lavorato insieme al team di Renishaw, giungendo a una soluzione sofisticata basata sulla simulazione a elementi finiti.”
Alex Garcia, Application Engineer di Renishaw, ha spiegato: “Utilizzando il software di terze parti Simufact Additive, siamo stati in grado di simulare perfettamente il processo di fusione su letto di polvere del sistema RenAM 500S. In sostanza, questo ci ha permesso di determinare un preciso fattore di compensazione che poteva essere usato per ‘pre-distorcere’ con accuratezza il design del componente.”
Analisi del componente del fodero prodotto in titanio con tecnologia additiva e software Simufact
Risultati
Attraverso la stampa 3D in metallo, Angel Cycle Works è ora in grado di realizzare componenti per foderi in titanio, precedentemente lavorati a mano, garantendo un alto livello di uniformità, con peso e resistenza migliorati e in quantità tali da soddisfare la domanda dei propri clienti.
La decisione controcorrente da parte di Optimus3D di costruire i componenti in maniera orizzontale, utilizzando il software di simulazione per adattare il progetto alla produzione, ha portato il livello di deformazione da 0,375 mm a 0,086 mm, ampiamente entro la tolleranza richiesta di 100 µm.
Questa innovativa soluzione di stampa 3D in metallo fa sì che ogni camera di lavorazione della RenAM 500S possa produrre 50 componenti alla volta in tempi molto brevi. Di conseguenza, il costo dei pezzi si è drasticamente ridotto e le operazioni della catena di approvvigionamento sono state riorganizzate.
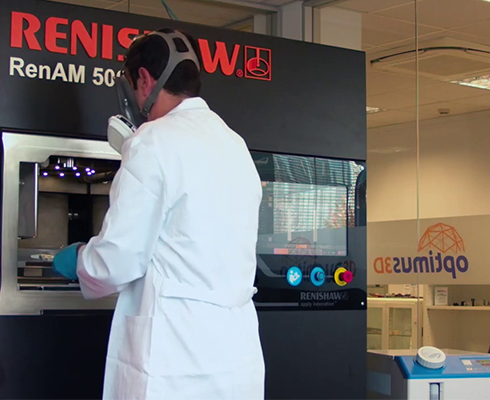
Il sistema Renishaw RenAM 500S presso la sede centrale di Optimus3D nel Parco tecnologico di Álava, nel nord della Spagna