Alignment lasers for machine build
What is an alignment laser?
An alignment laser is a precision tool that utilises lasers to accurately align components during build and service of industrial machines such as machine tools, precision stages and semiconductor manufacturing machines. Designed to optimise performance, alignment lasers facilitate high-accuracy measurement, digital reporting and real-time axis adjustments.
The increasing demand for intuitive tools to streamline machine alignment processes has outpaced the effectiveness of many traditional methods.
The XK10 alignment laser offers digital precision for aligning both linear and rotary axes, presenting a modern upgrade from traditional manual methods. This leads to a significant reduction in machine build, maintenance and service time.
Why would you use an alignment laser?
It is crucial to ensure precision during construction of a machine tool to make sure that it is reliable and efficient. Checking the alignment during the build process can prevent errors from being discovered after the machine has been built, which can be more difficult to fix. Regular alignment checks are also valuable during on-site service, maintenance or following a collision.
The XK10 alignment laser provides a quick, easy and versatile alternative to traditional methods, like dial gauges, autocollimators and metrology artefacts. It eliminates the need for time-consuming procedures. It can be used to ensure that linear rails are straight, square, flat, parallel and level. It can also assess spindle direction and coaxiality of rotary machines.
The XK10 display unit digitally records measurements, providing comprehensive error reports and reduces operator error due to manual documentation.
Key benefits
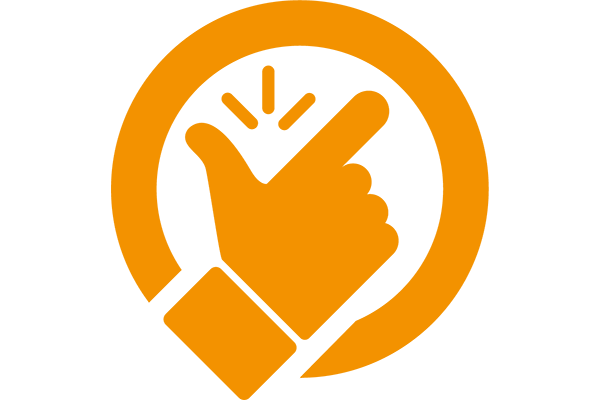
Easy to use
Guided step-by-step measurements reduce the need for highly skilled operators.
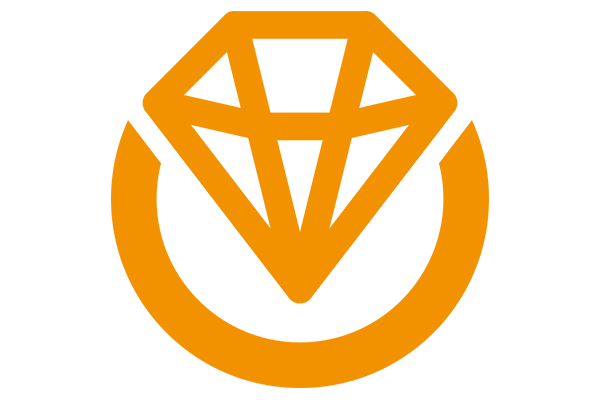
Multi-faceted
Measures rotary axes, spindles and facilitates precision during installation and automation.
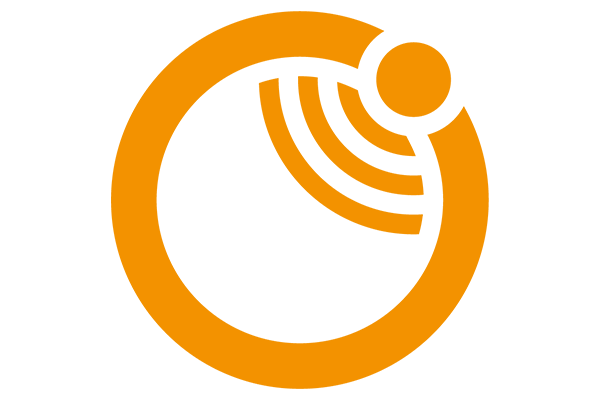
Live readings
Instant view of live readings results and dynamic graphs for efficient alignment and measurement.
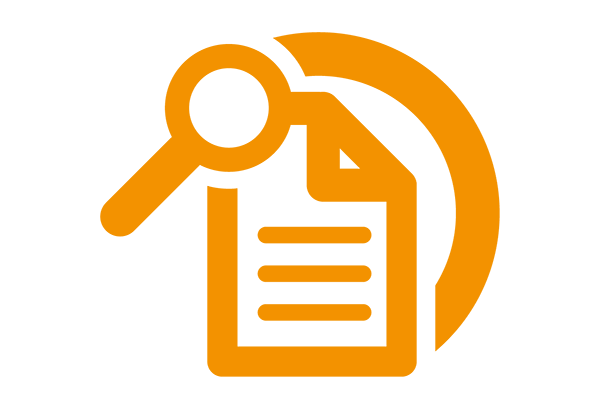
Detailed results
Straightness and parallelism analysis in the CARTO software Explore application, provides insightful actionable results.
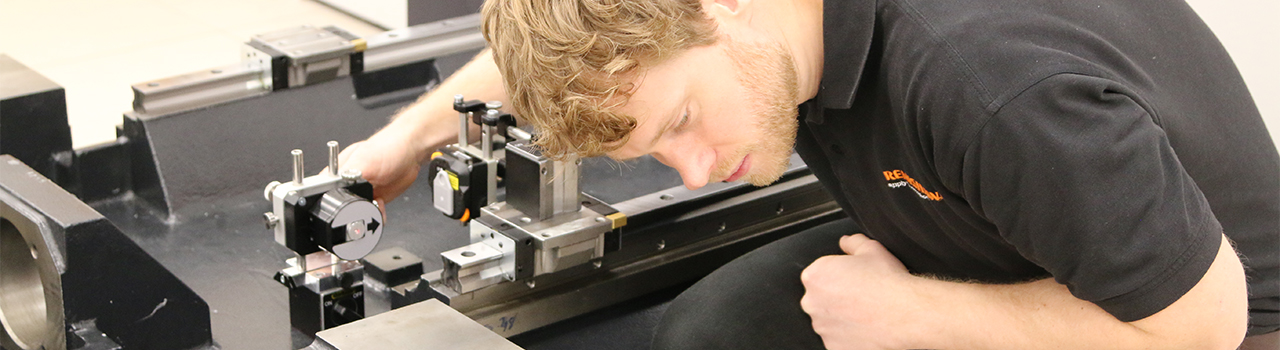
System overview
The XK10 launch is the primary laser source for most types of measurement. It is used with the M unit for geometric measurements up to 30 m. The S unit and M unit contain both transmitters and receivers which can be configured in different ways based on the measurement set-up.
The XK10's machine tool fixturing kit is designed to improve repeatability and accuracy in measurements. Measurements are taken and recorded with the XK10 display unit. This allows up to 30 hours of portable operation with the rechargeable battery.
The straightness and parallelism analysis feature in CARTO Explore creates custom reports. This provides reliable results for checking and correcting machine alignment.
Renishaw can provide calibration training from experienced engineers to ensure optimal product performance.
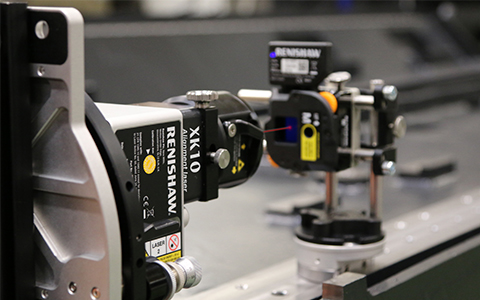
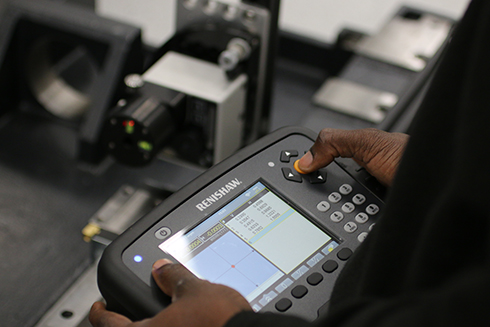
Key features
Flexibility - multiple measurements for different machine configurations from a single kit.
Automatic analysis - immediate measurement results, with live displays for adjustment and easy export to .xml file or CARTO.
Intuitive software - guides you through the set-up and measurement process, quickly and easily. Visit calibration software downloads for the latest version.
Wireless connectivity - ensures flexibility within the set up and measurement.
Easy fixturing - designed for repeatable, accurate results and reduces set-up time.
Rotating head - allows easy beam pointing from the launch unit with the capability to measure flatness using a series of grid points.
XK10 alignment laser accessories
Browse our range of mounting accessories and replacement parts.
XK parallelism kit
The XK parallelism kit is an additional accessory required to carry out parallelism measurements. It allows two nominally parallel straightness measurements to be carried out without moving the launch.
Accurate - 90° deflection of the laser beam. Versatile adjustments allow ease of alignment.
An optional tripod mount kit is available for use with a tripod when there is no space to directly mount the launch.
Straightness measurement
Measure vertical and horizontal straightness along an axis with the XK10 alignment laser system.
Used during the machine build process to ensure accuracy when mounting and aligning stages and guideways.
Spindle direction measurement
XK10 measures the angle at which a spindle or chuck is pointing.
This can be used for any spindle or chuck alignment, to ensure that it points in the same direction through a full 360° rotation.
Crucially, the XK10's reference mount has allowed us to capture and record accurate machine profiles, without the need for a linear guide rail. Not only has this reduced evaluation time, but it has provided greater insight into a variety of key data, which in turn will further improve the repeatability and accuracy of our measurements.
Mazak Europe, UK
Discover our case studies
Discover our machine calibration and optimisation products designed to improve the performance of precision motion systems.
FAQs
What is the beam measurement range for the XK10 system?
The XK10 launch unit can measure up to 30 metres when used with the M unit. When the M unit and S unit are used for different configurations, they can measure up to 20 metres.
What is the recommended recalibration schedule for the XK10 alignment laser?
The recommended recalibration period for the XK10 alignment laser when used in a 'normal' environment is two years. To find out more, visit our calibration service, repair and recalibration web page.