Renishaw vola in alto con Airbus A380 Superjumbo
Sotto ogni punto di vista, il nuovo Airbus A380 Superjumbo, che viene costruito in Europa, sarà il più grande aereo commerciale del mondo.
Potrà accogliere fino a 555 passeggeri, avrà un'apertura alare di oltre 80 metri e fusoliera a due livelli, assemblata con tecniche estremamente avanzate e innovative. Fra queste, molti robot che utilizzano i sistemi di encoder lineari RG4 di Renishaw (non raccomandato per i nuovi design, alternativa aggiornata: Encoder incrementale QUANTiC™ con riga RKLC40) per garantire l'accuratezza del posizionamento durante l'assemblaggio delle ali. Le quattro macchine sfruttano più di 1 km di riga ottica a nastro da 40 µm per determinare con precisione la posizione delle staffe mobili. Queste imponenti strutture di 80 tonnellate di peso e alte come un palazzo di 4 piani si spostano su tutta la lunghezza dell'ala per forare, maschiare e rivettare i rinforzi longitudinali ai pannelli.
Un sistema avanzatissimo
Electroimpact Inc, una società con sede negli USA, ha giocato un ruolo importante nella fornitura di macchinari avanzati per l'assemblaggio delle ali degli Airbus prodotti in Europa. I loro prodotti sono stati impiegati per la costruzione dei primi Airbus A320, dei quadrimotori A340 e ora vengono utilizzati nell'assemblaggio delle ali degli enormi A380, attualmente in costruzione.
Dall'inizio della sua collaborazione, per il montaggio dei rivestimenti sulle strutture portanti dei due modelli più piccoli, l'impegno di Electroimpact con Airbus è cresciuto fino a rappresentare quasi il 90% delle proprie entrate (nel 2002). Electroimpact ha iniziato a utilizzare i sistemi di encoder Renishaw per i primi macchinari destinati all'A320 e da allora ha continuato a servirsi di questi prodotti. Due fattori che hanno rappresentato il successo di tale collaborazione sono stati il supporto a livello mondiale fornito da Renishaw e la possibilità di ottenere la scala a nastro per l'encoder lineare RG4 in lunghi rotoli.
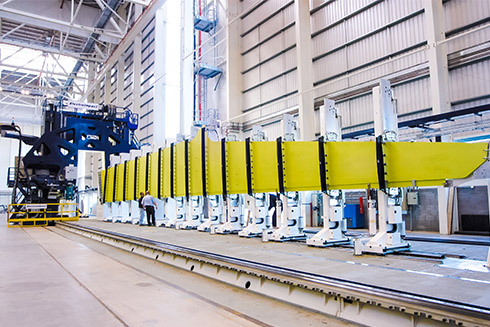
Migliaia di fori
I rivettatori elettromagnetici a bassa tensione (LVER) sono stati progettati appositamente: le gigantesche staffe a doppia torre si spostano su pianali lunghi abbastanza da contenere l'intera ala. Ogni testa deve effettuare migliaia di fori e applicare tutti i rivetti e i bulloni man mano che incontra le combinazioni rinforzo longitudinale/rivestimento e le rispettive colonne di supporto. Le teste devono essere sempre perpendicolari alla superficie del rivestimento e quindi devono essere in grado di regolare la propria posizione in relazione alle diverse combinazioni di centinatura, piano di profilo aerodinamico, diedro, cono e freccia alare presenti sull'ala.
Un elemento fondamentale per il processo è il complesso blocco di testa CNC per forare e rivettare. A sua volta, l'affidabilità di tale componente dipende dall'accuratezza lineare e dalla portata dell’intera struttura a portale che acquisisce dati dal sistema di encoder lineare RG4.
Peter Zieve, presidente e fondatore di Electroimpact, ha affermato dell'applicazione originale Renishaw: "È davvero straordinaria. Garantisce un processo altamente ripetibile e i tecnici non si accorgono neanche della sua presenza. Oggi tutte le nostre macchine vengono progettate prendendo in considerazione i sistemi di encoder lineare di Renishaw".
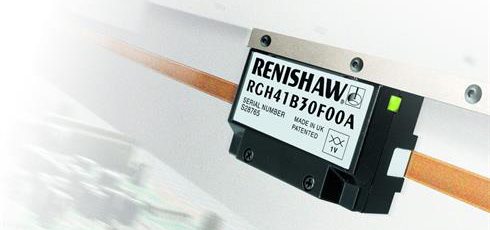
Electroimpact Inc (USA)
Invisibile e discreto
Il sistema RG4 è un encoder lineare aperto e senza contatto che può essere dotato di lettori con risoluzioni da 10 µm fino a 0,1 μm e oltre. Garantisce una velocità superiore a 10 metri/secondo, segnali conformi agli standard industriali e la compatibilità con la nuova riga ottica a nastro 'RGS40' di Renishaw. La riga ottica a nastro autoadesiva è fornita in rotoli, viene tagliata in base alle necessità e installata direttamente lungo l'intera distanza di spostamento della macchina che ha una lunghezza di 160 metri. È protetta dall'ingresso di sporcizia, liquidi e altre sostanze e, una volta installata, risulta invisibile e non richiede alcuna manutenzione. Le quattro linee Electroimpact delle stazioni iniziali 'Stage Zero' per l'assemblaggio delle ali installano tutte un rivettatore LVER e per ciascuna è in fase di costruzione una seconda unità per portare il numero totale a otto.
Risparmio di spazio, tempo e lavoro
Le celle di fissaggio automatizzate rappresentano un'importante innovazione rispetto ai sistemi di rivettatura del passato. Innanzitutto, occupano il 40% in meno di spazio e consentono di ridurre in modo estremamente significativo i tempi di lavoro e la mano d'opera, eliminando la necessità di segnare manualmente i componenti e quindi di dividerli per eliminare le sbavature prima di segnarli nuovamente.
Parlando del progetto relativo al nuovo A380, Zieve ha affermato: "Airbus è venuta da noi è ci ha detto: 'Avete fatto un ottimo lavoro nella creazione dei pannelli. Vorreste occuparvi di fornirci una macchina per la lavorazione dell'intera ala?' A questo punto il nostro contratto, che era già di dimensioni considerevoli, ha assunto proporzioni gigantesche!"