完全にフィットする Ricardo 社向けダイキャスト
Clacton-on-Sea(イギリス)に拠点を置く Tridan Engineering 社は Ricardo 社からモータスポーツ関連の加工を請け負っており、その一環として複雑な構造を持つダイキャストのアライメントにレニショーの工作機械用プローブを使用しています。パーツの最初のバッチの場合、通常約 2 ヶ月かかるところ、クライアントが求めるクオリティを下回ることなく 17 日で納品にいたりました。
背景
Langham Industries グループの一員である Tridan Engineering 社は 1968 年に設立され、世界中の顧客に業務代行サービスと加工サービスをトータルで提供してきました。60 人の従業員を現在かかえ、AS9100 および ISO14001 の認証を受けている同社は、航空宇宙、防衛、自動車、モータスポーツ、医療、海洋などの分野にサービスを提供してきました。
同社の機械工場はシングルヘッドの CNC 旋削や研削に対応しており、治具・工具部門がその工場にあります。また、同工場内ではマザック製の 5 軸機 Variaxis i-600 や横形マシニングセンター HCN500 など 14 台の CNC マシニングセンターが稼働しています。HCN500 の大半はパレット 2 台構成で、最大 80 個のツールを収納可能な回転ホルダーを備えています。
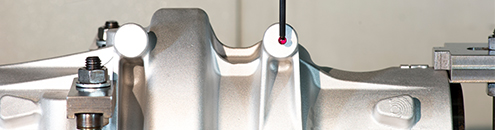
課題
「Ricardo Performance Products 社は、以前我々が製造したラリーカー用の後ろ車軸のテストに問題を抱えていました。設計か強度のいずれかに問題があり、同社は新型の『強化版』車軸をテストする必要にせまられていました。この手のプロジェクトは、顧客とのミーティング、コスト削減のための生産性を考慮した設計の提案、工作機械準備などで 8~10 週間かかるのが常でしたが、テスト施設でおさえた時間枠に間に合わせるには、ちょうど 17 日しか猶予はありませんでした。」(Tridan Engineering 社の Machine Shop Manager、Paul Coupland 氏)
後ろ車軸アセンブリは、カバーとメインケースという 2 個のダイキャストから構成され、それぞれが複雑な構造をしています。メインケースの場合、最初の 2 工程はマザック製の横形マシニングセンターで行います。その後、5 軸マシニングセンターに移して 1 工程行い、完了後また同じ横形マシニングセンターに戻して仕上げを行います。
レニショーの技術を採用した大きな理由は、精度です。レニショー製プローブがなければ、現状の半分のことも実現できていないでしょう。
Tridan Engineering 社(イギリス)
解決策
「弊社の 5 軸機には、レニショー製の高精度プローブ RMP600 が装着されており、最初の工程でカバーのダイキャストを正確に計測することができます。これにより、穴や形状が Ricardo 社の要望する位置にあることを保証できています。同様に、横形マシニングセンターでも、レニショー製プローブ OMP60 で、最初の工程でのメインケースのダイキャストの計測を行っており、顧客への納入パーツの品質を確保しています。Ricardo 社では組立からテスト施設への納入までほとんど時間がないため、このように品質を確保しておくことは最初のバッチ分にとって極めて重要でした。パーツ同士が初めから正確にフィットする必要があり、組立の段階で問題や遅れが発生してもいいような余裕はまったくありませんでした。」(Paul Coupland 氏)
ダイキャストを加工する際、作業の起点となるデータムなどを確立する必要があります。Tridan Engineering 社では、レニショーの工作機械用プローブ技術を用いてダイキャストの位置を計測してアライメントを行うことで、在庫状況のあらゆる変化に加工工程を自動的に適応させています。つまり、ワーク座標系が自動的に各パーツに自動的にアライメントされるようになっているのです。パーツを適切にセットアップすることで、加工中に素材の不足(アンダーカット)がなくなります。Paul Coupland 氏の言葉を借りるとすれば、「ダイキャストの『身』が、適切な場所にある必要がある。」ということです。
この工程では、空のダイキャストの計測データをデータムや加工した形状の位置や向きに対してアライメントする必要があり、ここでレニショープローブが役に立ちます。プローブ計測こそが、効率、品質さらに工作機械の性能と精度を最大まで高められる広く定着した方法なのです。プローブ計測は、最新の CNC コントローラに内蔵した標準的なルーチンにより、加工作業により簡単に組み込めるようになっています。
カバーとメインケースは別々に加工した後、ボルトでアセンブリ化し、横形マシニングセンターで加工します。
その後分割し、仕上げ工程として再度横形マシニングセンターでそれぞれに穴を加工し、2 個 1 組で保管します。しかし、工程はここで完了ではありません。「Ricardo 社用に加工したダイキャストの全バッチに添付して、パーツの全限界寸法を詳細に記載した FAIR(First Article Inspection Report:初回製品検査レポート)を我々は提出しなければなりません。この作業には、我々自身もお客様にも安心してもらえるようレニショー製プローブヘッド PH10MQ を装着した三次元測定機 (CMM) を使用しています。PH10MQ にはレニショー製キネマティック式タッチトリガープローブ TP20 など様々なアタッチメントを組み合わせています。」(Paul Coupland 氏)
CMM にレニショー製プローブを採用したことで、ダイキャスト上の扱いにくい形状や内側にあるへこみへのアクセスが可能になっています。この CMM はまた、加工したダイキャストの初回測定にも使用されており、その一方で、レニショー製プローブヘッド MH20i やアタッチメントを装着した Tridan Engineering 社の手動 CMM も形状によっては測定に使用されています。「レニショーの技術を採用した大きな理由は、その精度です。レニショー製プローブがなければ、現状の半分のことも実現できていないでしょう。さらに、レニショーは積極的にサポートしてくれるため、実はまだ修理関連部門のお世話になったことはないのですが、製品が故障するようなことはありえないでしょう。」(Paul Coupland 氏)
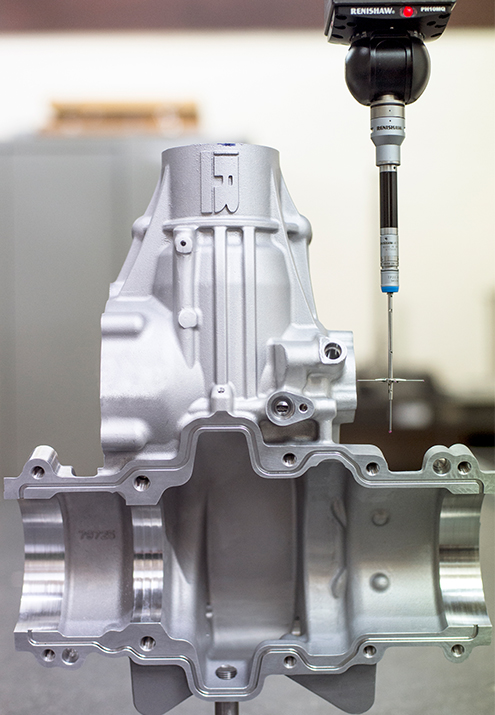
レニショーは積極的にサポートしてくれるため、実はまだ修理関連部門のお世話になったことはないのですが、製品が故障するようなことはありえないでしょう。
Tridan Engineering 社(イギリス)
結果
レニショー製工作機械用プローブを使って正確かつ効率的にダイキャストをアライメントでき、さらにレニショーの CMM 技術に基づく寸法計測をできるようになったことで、指定された短期間で品質の良い製品を納品することが可能になりました。
「スピードと効率が大きな収穫であったことは間違いありません。パーツの複雑さや計測対象の形状数などを考えると、手動で計測しなければならないとしたらおそらく 2、3 日はかかっていたでしょう。加えて、関連する公差のことも考慮に入れると、手動計測はほぼ不可能だったでしょう。」(Paul Coupland 氏)
Tridan Engineering 社が Ricardo 社と密接に連携し、休みなく稼働したことで、テスト予定日前日の午前 10 時に問題なく加工できた新しい車軸のダイキャストが顧客の手に渡り、高い満足を得るに至りました。
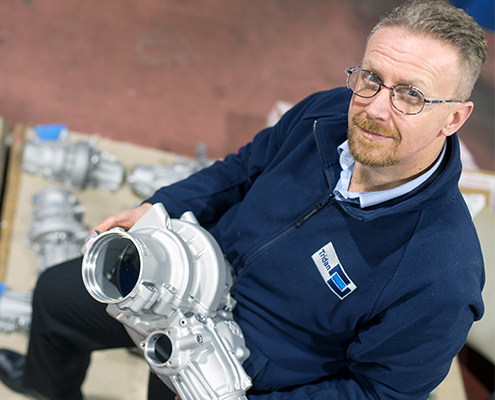