航空機用インペラメーカーの製造時間短縮にレニショーが貢献
世界的なエンジニアリング複合企業 Honeywell 社の傘下にある Honeywell Aerospace 社は、民間航空機で使われるインペラやブリスクを大量に製造しています。
事実上の遠心コンプレッサや軸流コンプレッサと言えるインペラの品質は、加工工程を通して維持されるワークのデータムに左右されます。
データムを保てないと、不適合なインペラとみなされ、再加工や補修が必要になり、場合によってはすべてスクラップになります。
加工工程における精度維持のために、Honeywell 社は、世界的なエンジニアリング企業であるレニショーの RMP600 高精度工作機械用プローブ計測システムとマシニングセンター用 PC ベース寸法計測ソフトウェア Productivity+™ の導入に踏み切りました。これらにより、Honeywell 社では、加工前に計測を実施し、工程の初期段階で軸方向のずれ検出ができるようになっています。
背景
この工場で製造するインペラの大きさは、直径 14 インチから 17 インチと様々で、その素材は、1 種類のみアルミで、残りはチタンです。
チワワ工場で製造した製品は、航空機用タービンの組立てと試験を行う、アリゾナ州フェニックスの自社組立て工場に運ばれます。
完成したインペラのデータムが不正確であった場合、設計解析に回されます。設計解析では、そのインペラが使用できるかどうか設計者によって判断されます。
使用工具は約 130 種類であり、Honeywell 社はこの製造工程を 2 週間のスパンで計画しています。加工後のパーツでずれが見つかった場合、解析によって 1 週間余計に時間が費やされます。そして、機械のダウンタイムや計画の遅延につながり、製造時間や製造コストに影響が及びます。
課題
データム中心が軸方向にずれる原因の 1 つには、ワークの不適切なセットアップがあり、不適切なセットアップは、人的なミスや、治具の損傷、前作業で残ったバリなどで生じます。
解決策
Honeywell 社の Manufacturing Engineer である Luis Adrian Gallegos 氏は、インペラ製造工程の最初のサイクルが完了した段階で、製造工程中に発生するずれを減らす方法について品質保証担当の人間と話し合いを持ちました。
「最初のサイクル後、製造工程を強化する必要性は感じていましたが、大きな投資にはしたくありませんでした。そこで、レニショーさんと、高精度小型タッチプローブとソフトウェアを使って、加工前にパーツ計測でずれを検出して、パーツのずれを補正できないか、検討しました。
色々と検討した結果、無線で通信を行う RMP600 工作機械用プローブの導入に至りました。このプローブを導入したことによって、自動で段取りが行えるようになり、また、我々の製造するインペラのような複雑な 3D 部品の形状を計測できるようになりました」(Gallegos 氏)
加工工程中、レニショー製プローブがパーツの様々な箇所にタッチし、誤差やずれがないか特定します。
「プローブのおかげで、不具合が起きる前に不正確な箇所を検出することができます。以前では、16 時間加工を行いその後 1 時間以上の測定作業を行わないと、1 つの問題も検出できなかったものです。今なら、パーツに不具合があればそれについての警告を受け取って、貴重な加工時間やリソースを無駄にする前に必要な対策を打てます」(Gallegos 氏)
「Honeywell 社はプローブだけでなく、PC ベースの寸法計測ソフトウェアの Productivity+ もマシニングセンター用に導入しました。Productivity+ を導入したことで、プローブ計測ルーチンやインプロセスでの合否判断を加工サイクルに組み込むための、使い勝手のよいプログラミング環境が整いました。ワーク芯出しや寸法計測の作業が簡素化し、段取り作業やパーツ確認、工具確認といった加工工程の中核にあたる部分をアシストしています。また、完了した工程についての情報収集もできますし、後続作業や工程の判断にも活用できるため、工程後のレポートにも Productivity+ は役に立ちます」(Barriga 氏)
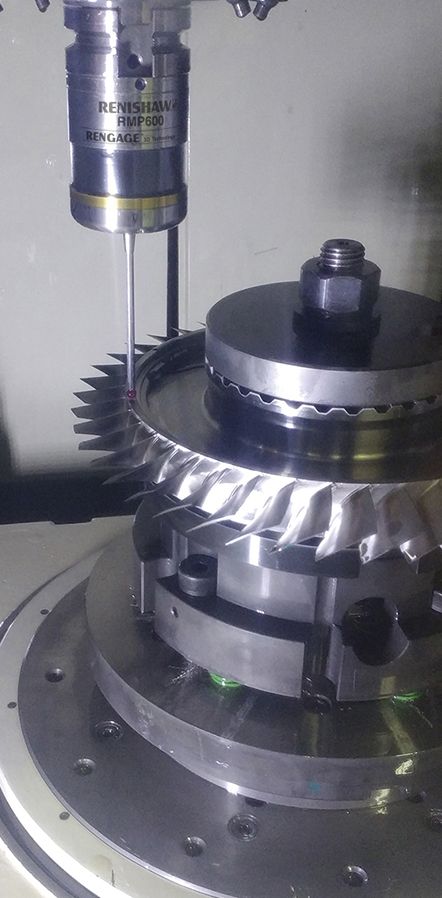
レニショーのプローブとソフトウェアのおかげで、加工工程が想定どおりに実行していると確信を持てるようになりました。導入前は、機械のオペレーターがワークを取り付け、ゲージをセットし、直径や面を確認していましたが、見逃しや読取りミスがあったり治具に損傷があったりした場合には、完成品に不具合がでていました。今は、前もって不具合を見つけることによって、根本から起きないようにしています。
Honeywell Aerospace 社(メキシコ)
結果
レニショーのプローブとソフトウェアのおかげで、加工工程が想定どおりに実行していると確信を持てるようになりました。導入前は、機械のオペレーターがワークを取り付け、ゲージをセットし、直径や面を確認していましたが、見逃しや読取りミスがあったり治具に損傷があったりした場合には、完成品に不具合がでていました。今は、前もって不具合を見つけることによって、根本から起きないようにしています。
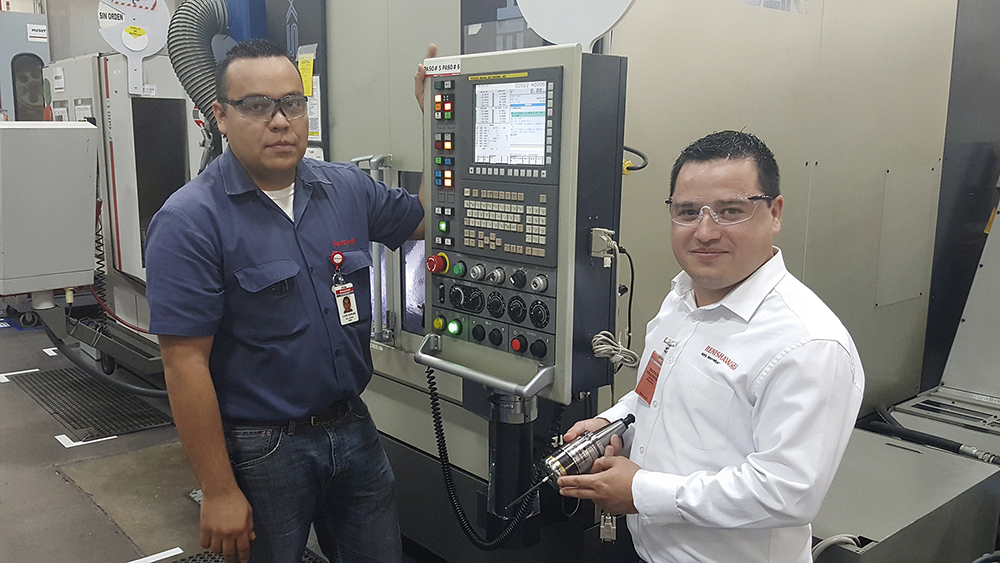
主筆者による承認のもと、Modern Machine Shop Mexico 社により加筆作成
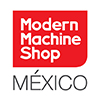