RenAM 500 metal additive manufacturing (3D printing) systems
The RenAM 500 series
Renishaw's industry-leading additive manufacturing (AM) systems use laser powder bed fusion for metal component volume production.
A system for every stage of your AM journey
The RenAM 500 series provides the complete platform for scaling your AM application.
Configurable with one (500S), two (500D) or four (500Q) high-power 500W lasers, and automatic or flexible (Flex) powder and waste handling, utilise the same industry-leading gas flow system, safety and precision digital optics from material proof of concept all the way to volume production.
The RenAM 500 series features a build volume of 250mm x 250mm x 350mm.
Core features of the RenAM 500 series
Common to all RenAM 500 series machines is the same industry leading gas flow system, precision dynamic control and software for connected digital workflows.
Intelligent gas flow system
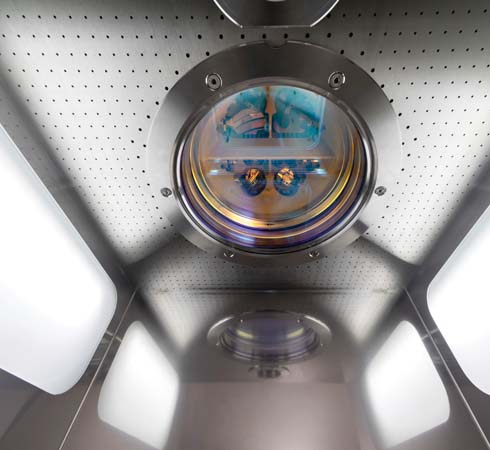
The RenAM 500 series features a high-volume cascading gas system which provides uniform processing conditions as well as superior removal of process emissions from the laser path. The gas circuit includes an intercooler which provides active thermal control, even with 2kW of laser power available. Precise thermal management further contributes to the stable atmosphere and consistent build environment that leads to better and more consistent metallurgy.
Renishaw's dual SafeChange™ filter system efficiently removes process emissions from the gas stream, enables tight control over system pressure loss, and helps precisely maintain optimal gas flow. Individual filters can be swapped out mid-process without interruption and the intelligent pre-conditioning system will ensure no disruption in build conditions.
The RenAM 500 series' fully sealed vacuum chamber enables Renishaw's patented atmosphere generation system to quickly prepare a high purity argon build environment with minimal gas consumption. The combination of vacuum purging and high integrity system sealing also maintains powder quality and increases longevity.
High precision dynamic control
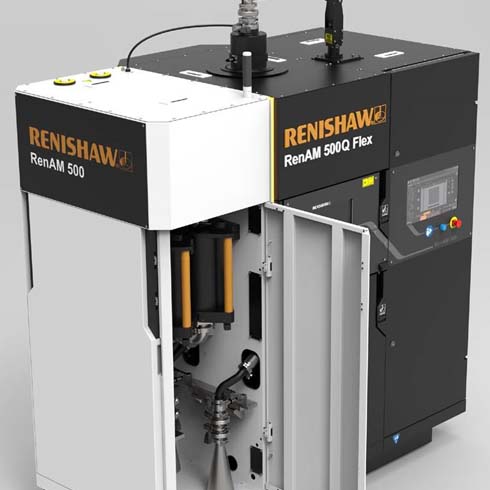
The RenAM 500 optical system features dynamic focusing, enabling all lasers to precisely address the entire bed simultaneously. This flexibility ensures build times are minimised by enabling the laser energy to be optimised over the entire powder bed.
The system uses a monolithic water-cooled additively manufactured galvanometer mounting, designed and manufactured in-house by Renishaw. Unlike separate mountings found on other multi-laser AM systems, the RenAM 500 series design features tight alignment of the optics and internal conformal cooling channels. This is a key enabler for precision laser control.
Harnessing Renishaw's industry-leading metrology technology, the RenAM 500 series features a RESOLUTE™ optical encoder with a 1 nm z-axis resolution for high accuracy positional sensing.
The kinematic recoater mounting ensures rapid and repeatable positioning of the powder spreading recoater blade. Together, these features help maintain a precise relationship between the optical system and the working plane, which is vital for accurate part manufacture. The flexible recoater blade is forgiving for both solid and lattice geometry manufacture.
Exceptional metallurgical performance
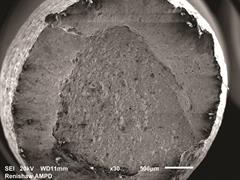
The intelligent gas flow and precision control of the RenAM 500 series enable production of components with >99.9% density, maximised strength and ductility.
The uniform extraction of process emissions, exceptionally low oxygen and moisture content, and consistent optical control, eliminates sources of chemical, micro-structure or mechanical defects.
Download the material datasheets to see representative mechanical properties of the wide range of supported metal powders.
Smart manufacturing technologies
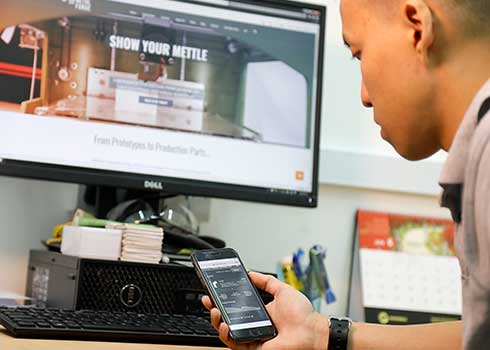
Intelligent sensing technology is utilised throughout the RenAM 500 series, with software solutions tailored for exploiting the benefits of Industry 4.0.
Embedded in the in-house designed optical system are LaserVIEW and MeltVIEW hardware which provide high bandwidth monitoring of both the output laser intensity and optical emissions from the AM process across the near-infrared spectrum. CameraVIEW provides layer-by-layer images for powder dose monitoring.
This rich process monitoring data can be visualised, compared and further data processed in near real-time through Renishaw's InfiniAM software suite. The voxel-based visualisation toolset enables high resolution analysis of each component weld as well as powder dose. As part of Renishaw's open ethos, the software architecture supports user plugins, enabling custom algorithmic manipulation of the data to suit research and production environments.
Renishaw Central, our manufacturing data platform, provides real-time connection to monitor, record and analyse RenAM 500 series sensor data, as well as Renishaw's portfolio of industrial metrology products. Through the web interface, or mobile app, you can monitor in-progress atmosphere, powder and temperature data from the machine, or drive insight through historic build analysis.
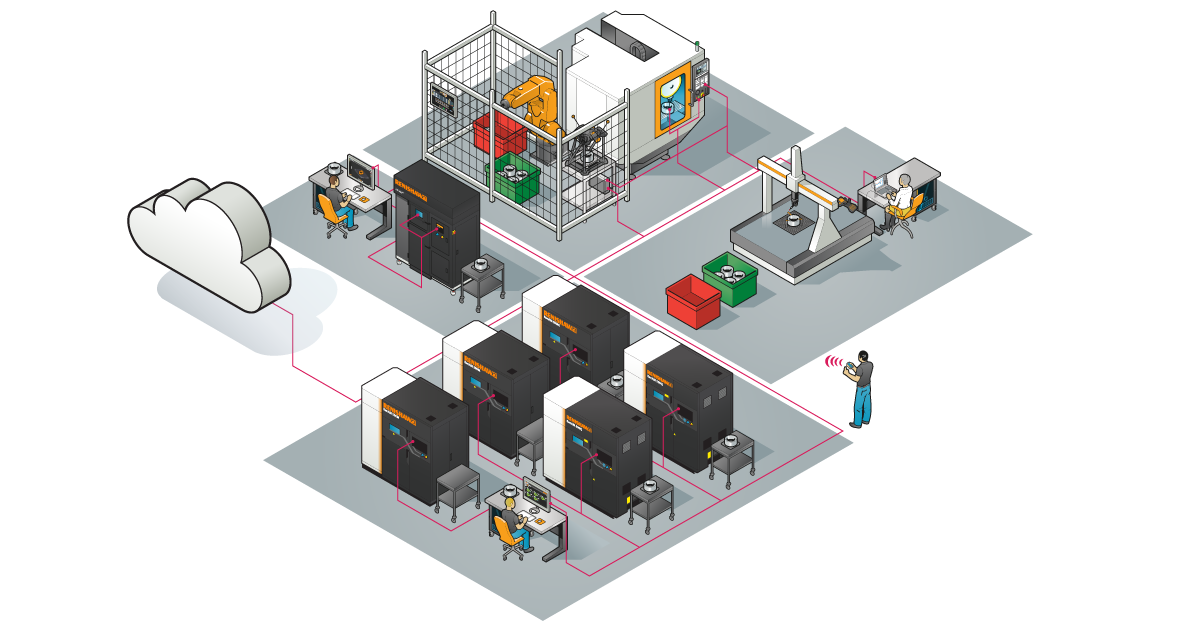
As well as supporting standard connection interfaces such as MTConnect, Renishaw Central is built as an API that can be directly consumed into existing ERP and MES software.
In support of your preferred digital workflow, Renishaw's AM build preparation software QuantAM is available as a Post Processor in a wide range of industry leading CAD/CAM packages, by direct consumption of the API, or as a standalone application. The standalone application offers a stage-based workflow to easily guide users from parametric or triangulation CAD, through orientation, support generation, build layout and slicing. All print settings are open and editable by default, with design-of-experiment tools ideal for custom material optimisation.
Configurable powder management
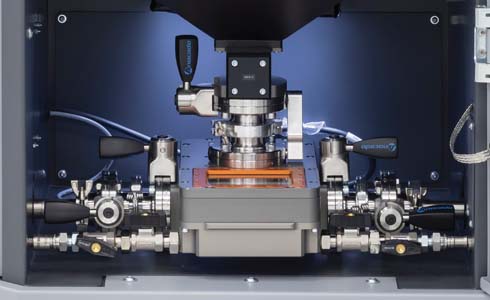
The RenAM 500 series can be configured with either closed loop powder recirculation or an open gravity fed system. Coupled with four high powered lasers addressing the entire build volume, powder recirculating reduces operator intervention and delivers ultra-productivity and lower part costs for volume production.
The open gravity fed system (Flex) has a simplified powder pathway, which is suited to users who want to regularly swap build materials. All elements of the powder module can be quickly cleaned or replaced to prevent material cross-contamination. RenAM 500 Flex systems can be converted in-situ to have powder recirculating, enabling seamless transition between material research and production phases of application development.
Find out more
Explore the possibilities presented by advanced additive manufacturing by visiting our AM guide to learn more about how we make exceptional quality cost-effective components, or read case studies from RenAM 500 series customers.
Visit the AM guide Read case studies Find your local office Contact us
Finance options
Renishaw's in-house finance options are simple and competitively priced, enabling you to choose the most appropriate solution for your business.
Learn moreFixed monthly costs to match your cashflow requirements.
A hire purchase/capital lease agreement with Renishaw provides all the benefits of ownership without the initial capital outlay. After a deposit you pay regular instalments covering capital repayment, interest and maintenance.
Operating lease for additive manufacturing equipment
Low monthly payments, no disposal worries and a purchase option at the end of the agreement. An operating lease gives you maximum flexibility.