Repensar y la eficiencia en la fabricación CNC

Repensar: un reto casi obligado para mejorar la eficiencia
"El visionario comienza con una hoja en blanco y reimagina el mundo" dijo el periodista y autor Malcolm Gladwell. Repensar es un desafío en sí mismo, y replantear un proceso de producción es algo que entraña numerosas dificultades, pero que puede suponer un gran avance. Para ello, se requiere un partner fiable.
Pero, ¿cómo puede el replanteamiento de nuestros procesos mejorar la eficiencia? ¿Cómo podemos identificar y mejorar los puntos críticos? ¿Hasta qué punto es importante reducir los errores de tolerancia? ¿En qué fase podríamos optimizar tiempo y recursos?
En este artículo damos la respuesta a estas y otras preguntas en el contexto de un caso real: el caso ‘Hammond Engineering'.
Una página en blanco: Replantear los procesos en la fabricación
Hay muchos sectores que requieren una producción en serie, la automoción o la electrónica de consumo no pueden permitirse errores o disfunciones en sus procesos. De hacerlo, dejarían de ser eficientes. Por ese motivo, identificar y mejorar los puntos críticos es determinante. Pero, a menudo, poner la página en blanco y volver a imaginar no es tarea fácil.
¿Cómo un pequeño cambio puede alterar toda la línea de producción? Pongamos un ejemplo siguiendo el hilo anterior. Una producción en serie requiere el máximo de precisión posible.
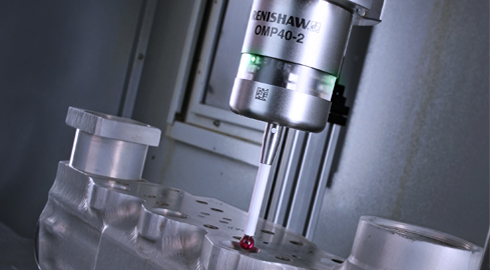
Calcular mal los errores de tolerancia, por ejemplo, puede multiplicar el número de piezas desechadas. Para ello, es casi imprescindible establecer y especificar un rango de error permitido entre el valor medido y el verdadero, especificando la tolerancia más precisa posible para la fabricación de cada elemento.
Si sumamos una medición de herramientas automatizada en el momento óptimo podemos ganar tiempo, calidad, eficiencia, al mismo tiempo que reducimos el error humano.
¿Cómo podemos ayudarle a mejorar el proceso de fabricación CNC?
Descubre las posibilidades reales de los sistemas de inspección y cómo eliminar la variación en los procesos de fabricación.
El caso 'Hammond Engineering': mayor productividad, menor tiempo de respuesta y reducción del error humano
Un claro ejemplo para visualizar la necesidad de repensar el proceso productivo es el de Hammond Engineering, cuya inversión de tiempo en la revisión de sus máquinas, obligaba a interrumpir la producción varias veces al día. La compañía con sede en Bairnsdale, Australia, ofrece servicios como el diseño asistido por ordenador, así como el Mecanizado CNC en línea (fresado y torneado CNC) para diferentes tipos de producción, que van desde la creación de prototipos hasta grandes series industriales.
El tiempo necesario para estos pequeños cambios, como puede ser la alineación de una mordaza, era el momento en el que las máquinas dejaban de funcionar. En una empresa pequeña, en la que la configuración de esta máquina debe modificarse manualmente varias veces al día, el total de minutos dedicados suponía un elevado coste a final del año.
Repensar el proceso productivo en este caso era un reto orientado a aumentar la productividad, reducir los tiempos de respuesta y reducir el error humano.
Como solución, Renishaw planteó el usó de la sonda de transmisión OMP40-2, que calcula alineaciones sin necesidad de intervención. Se trata de una sonda 3D ultra compacta de activación por contacto con transmisión de señal óptica.
Su uso principal es la preparación e inspección de piezas de trabajo en centros de mecanizado. La sonda de transmisión OMP40-2 ofrece mayor precisión y hasta un 90% de reducción de tiempo en los cambios en la configuración de la máquina.
Además, el uso de la sonda también redujo las posibilidades de que un error humano afectara a la producción, gracias al cálculo de ángulos sin necesidad de intervención humana. Ya lo dicen: a veces, las mejores ideas salen de un papel en blanco.
En conclusión: comprender, repensar, ganar
“No puedo creer que haya tardado tanto tiempo en darme cuenta de lo valioso que es el palpado en mi entorno de trabajo”, expusieron desde Hammond Engineering tras la experiencia. Si alineación de una mordaza solía tardar cinco minutos en completarse, con la OMP40-2 la tarea se redujo apenas a un minuto.
En el futuro, también planean utilizarla para la medición en proceso de piezas repetitivas y garantizar así un posicionamiento y alineación correctos. La empresa también planea utilizar la detección de rotura de herramientas para mejorar la fiabilidad y confianza del proceso.
Por cierto, que Malcolm Gladwell también dijo que la clave para una buena toma de decisiones no es el conocimiento, sino la comprensión. "Nadamos en lo primero. Nos falta desesperadamente lo segundo" añadía a esta frase. El conocimiento y la experiencia de Renishaw en diferentes países y sectores le permiten ofrecer un análisis previo para repensar y mejorar cada proceso.
Leer artículo anterior Volver al menú