현재 사용 중인 언어로는 이 페이지를 사용할 수 없습니다. Google Translate을 사용하여
자동 번역된 페이지
를 볼 수 있습니다. Renishaw에게는 이 서비스를 제공할 책임이 없으며 번역 결과를 저희가 확인하지도 않았습니다.
추가로 도움이 필요하시면
저희에게 연락해 주십시오.
“Throw the machining rule book away and get creative”
“Unit cost for a one-off component is the same as a batch of a thousand” says Steve Randerson, Production Manager at Boxtrees Precision Engineering Ltd, Halifax, UK. The company has employed a Renishaw OMP400 high accuracy touch probe and NC4 non-contact laser tool setting system on a Mazak Integrex 200-IV ST to radically reduce non-productive setting. Improvements have also been seen in component accuracy and the consistency of cycle times, with a direct effect on production scheduling, plus the vast majority of post-machining inspection has been eliminated.
Boxtrees make all the machined parts for a large range of educational machine tools supplied by sister company Boxford, along with other sub-contract work.
Mr Randerson explains “Five years ago I did a detailed analysis of our machining operations and found that 40% of machine time was used setting jobs. This had to change, and what better figure to aim for than 0%? That is where we are now. Many companies have moved production out of the UK to reduce costs, we have chosen to cut costs by improving our operation here. We make what we need when we need it, there are no components that have cost us money to produce sat on the shelf not earning us money. The majority of work now is in very small batches, including single parts, but crucially that makes no difference to the productivity.”
The Mazak Integrex, originally fitted with the Renishaw systems when supplied, has been installed at Boxtrees for 11 months, one of three CNC machine tools in active use in a very large machine shop now containing increasingly inactive manual machines.
In that time Mr Randerson has created machining programs for over 200 different components, which can be machined in many different materials, usually mild steel, cast iron or aluminium. Every one of these programs relies on Renishaw part setting and tool breakage detection macro routines to control the process, making the most of the flexibility offered by the Mazak multi-axis mill-turn machine.
Tool life is more important than cutting time
“Everyone talks about reducing the time taken to cut the part,” says Mr Randerson “I'm more interested in minimising tool wear to keep tooling costs down, so we don't cut as fast as we used to, and now get 20% more tool life. I'm also keen to identify that occasional scrap part and make sure it doesn't make its way through to final assembly. If an out-of-tolerance part is assembled into a Boxford machine it can mean a 4-hour strip-down to change it. So the programs use the optimum speeds and feeds for long tool life, cut out any wasteful machine movement, and employ a lot of logic that allows the machine to make ‘intelligent' decisions according to the feedback from the probe systems.”
The Mazak Integrex is used for twin-spindle billet work during the day when the operator is present, with many different shapes and sizes of billets, whilst overnight it runs un-manned, with material supplied by a bar feed. In both cases final part inspection is performed by the touch probe on the machine, with measured values recorded in a text file. This is fed back to the production scheduling system as a permanent record of the critical dimensions of the component and whether any feature was out of tolerance i.e. a scrap part. The OMP400 is an ultra compact probe, ideally suited to multi-axis machines thanks to innovative RENGAGE™ technology, which brings unrivalled 3D measurement performance.
Billet work during the day
The dimensions of each individual raw billet vary considerably, often over or under size. The first operation after it is loaded will always be to check the billet length using the OMP400 touch probe, which is loaded into the machine spindle from the tool changer, like a cutting tool, when needed. In some cases the billet can be over size by up to 8mm – the program changes the number of cuts used on the first face accordingly.
If it is undersize the billet is rejected before the machine wastes time attempting to cut it. Features on the billet may be measured by the touch probe during the machining cycle, for example checking a bore before adding a keyway. Critical features on every finished part are inspected to decide whether the part is within tolerance: in some cases extra datum features are actually added to the design to enable easy measurement of the critical features.
Un-manned overnight bar work
During the day the production scheduling system, on a networked PC in the planning office, is ‘loaded up' with machining jobs to run overnight according to orders received, often on that day. These will all be of one material, typically mild steel, cast iron or aluminium, but the quantity of parts can be set to any value from 1 upwards. The schedule automatically adds the relevant machining program, drawing it in from a database, and then adjusts it according to the quantity required. Any mixture of jobs can be added in any order, all of these cut from standard bar stock. The Mazak Matrix controller is based on a PC, which is connected to the Boxford group network, and receives the NC machining files across the network.
The machine is left to run at the end of the day, with the touch probe and tool setting probe systems trusted to be the eyes and ears of the operation. If a finished part is out of tolerance the logic in the program does not employ the parts catcher to remove the finished part when it is parted off; instead it falls into the swarf bin, so there is no chance of bad parts going to assembly. At this point the machine is programmed to make another of the same part, so that enough parts are ready in the morning. Good parts are collected on a parts conveyor, with part dimensions recorded and reported back to the SPC system.
Mr Randerson carefully analyses the data “One of the main reasons for any machine to start producing bad parts is thermal drift. Assuming the machine is run up to temperature this can be caused by a change in ambient conditions. We don't heat the machine shop overnight so it can gradually drop by more than 10°C easily. The Mazak is very thermally stable, far better than others, but the measured data from the probe allows the logic in the program to compensate for this during the night.”
Expensive scheduling software?
What is the scheduling software that can do all this - surely it must be expensive? The surprising answer is Microsoft Excel. The key to such a comprehensive system is actually just the creative thinking and logic employed by Steve Randerson to bring all the data together and control the process, using spreadsheet commands. The same document within the program includes many functions, including recording orders received, measured values of finished parts, SPC analysis, and a database of machining programs.
Some in the machine tool industry argue that it is not good practice to measure on the same machine that could have introduced errors when cutting the part. However Mr Randerson disagrees, “We are working within typical tolerances of 10 to 12 microns, well within the positioning and measuring accuracy of the machine. The first part in a production run will get a full inspection off the machine, along with other occasional independent checks, but we don't really need to bother. The probe system on the machine keeps proving to be much more accurate than the manual inspection devices we used to use for every component before. It was because we relied on devices like plug gauges that bad parts used to get through to assembly.”
The Integrex is fitted with a Renishaw NC4 non-contact laser system which can set the tools for length and diameter initially, but can also be used for a rapid breakage check, looking for a significant change in length.
Small delicate tools are checked after every use while the less vulnerable tools might not be checked at all, but it can also depend on which material is being cut. The same tool can be used for 6 different materials, so on aluminium it might not be checked, but on cast iron it is checked periodically. If a tool breakage is detected the machine does not stop, as Mr Randerson doesn't want to lose production time or be missing one part - an identical ‘sister' tool will be loaded instead and machining continues.
Design for manufacture
Components have been re-designed to enable and improve machining on the Integrex. A high capacity 120-tool changer system was purchased with the machine, but even this would not accommodate all the tools that were needed previously, especially when provision has to be made for sister tooling. Steve Randerson gave the designers a far shorter list of tools that could be used to machine all the jobs in all the different materials - a number of changes were made to accommodate this. Not only that, but they also took a far more sensible view on tolerances and surface finishes, with blanket tolerances on surfaces thrown out and each feature closely examined to see what was actually necessary for function and appearance.
Tool control and part setting on a Mazak VTC300 machine
Boxtrees also have a Mazak VTC300, a CNC machine tool with a long fixed bed which can be divided in half with a solid screen (although occasionally the screen is removed for very large jobs), all 3 axes of movement being in the machine head. The operator can be safely loading a job on one half of the bed, while the machine is cutting on the other, but the machine used to spend a lot of time idle while it was being set. A spindle-mounted Renishaw touch probe was fitted which is now used to set the job accurately, eliminating the need to make or purchase elaborate fixtures, but also removing the need for manual part setting.
The VTC has the capacity to hold 48 tools, using a tool recognition system based on a chip on the tool shank, but was not supplied with a tool setting system leaving the potential to make mistakes loading the wrong tool data. Renishaw retrofitted a NC4 laser system to control the tool setting procedure, and by employing logic routines in the machine program the machine cannot go wrong anymore. Machining is now right first time, every time.
Boxtrees Precision Engineering and Boxford educational machine tools
Boxtrees is part of the Boxford group of companies. Currently 90% of Boxtrees work is for Boxford educational machine tools, along with jobs for other parts of the Boxford group - RJ Mobility, making customised wheelchairs, and Protex Developments, making fume cupboards for the Pharmaceutical industry. Boxtrees also takes on a large variety of sub-contract work, customers including 600 Lathes and Renold Gears, and now has available capacity to take on more.
Demand for Boxford educational machines is currently very strong, barely affected by the current recession that has hit so many manufacturing companies, and helped considerably by export orders. Many countries realise the importance of training students in the use of CNC machine tools - Boxford are currently working on an order for 136 machines for schools and colleges in North Africa.
Boxford machines are available in a wide variety of configurations, including CNC lathes, VMCs, cleverly designed combined lathes and machining centres and CNC Routers. The most significant constraint on machines is the need to fit through a standard doorway as very few schools have the loading doors found in industrial premises.
All machines are controlled by software that runs on a PC, which also includes comprehensive CAD/CAM packages to train students in the use of graphical design tools, with full simulation of designed parts and machining processes. The machines are the final part of the process, turning the students' 2D and 3D CAD designs into physical parts. School children and students with no manufacturing experience can design a complex part and start machining it on a Boxford machine within 5 minutes.
Boxtrees demonstrates outstanding efficiency
Steve Randerson has proven how correct integration of the Renishaw part and tool setting probe systems with the Mazak machine tools, along with innovative software, can result in a highly efficient system for production of small batches of complex components. As Steve concludes, “Machine set-up time has plummeted, we are talking zero instead of hours. We used to have a backlog in production, not any more.”
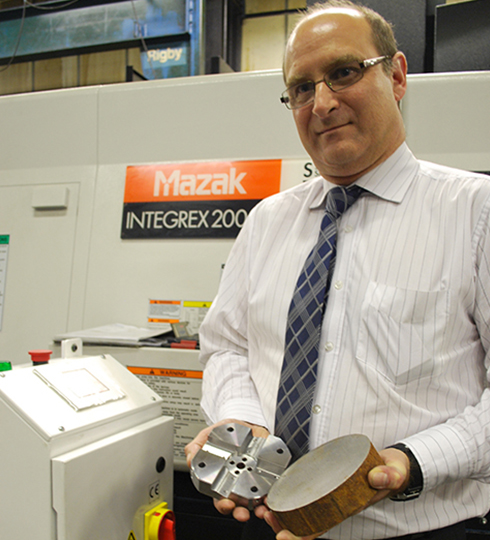