No momento esta página não está disponível em seu idioma. Você pode ver uma tradução automatizada utilizando o Google Translate. Não somos responsáveis pelo fornecimento deste serviço e não podemos verificar os resultados.
Se você necessitar mais ajuda fale conosco.
Pump manufacturer extends the life of their machine tools and reduces downtime by 10%
Aquasub Engineering, a major pump manufacturer based in India, believes the Renishaw QC20-W ballbar is an essential tool; reducing maintenance costs, increasing capacity and reducing scrappage.
The Renishaw QC20-W ballbar system is widely recognised as a preventative maintenance tool for new and installed machines. Aquasub Engineering (Coimbatore, India), part of the Aqua Group, one of the largest pump manufacturing companies in Asia, is using QC20-W ballbar to reduce maintenance costs, increase capacity and reduce scrappage.
With an increasing emphasis on Total Productive Maintenance (TPM), Aquasub started looking for solutions and on discovering that Renishaw had launched a new wireless QC20-W ballbar system, decided to get a demonstration. The scope and precision of data given on various machine errors with a QC20-W test amazed them. With up to 18 separate geometric, plug and dynamic errors diagnosed, this gives far more reliable diagnosis than their existing practices.
The demonstration carried out on Aquasub's machines won their confidence and convinced them that QC20-W ballbar was an essential health check tool for their TPM programme.
To reduce the necessity of purchasing new machines, Aquasub want to maintain their 200 existing machines, many of which are 25 years old. Mr K Senthil Kumar, General Manager, explains, “We would obviously prefer to maintain our old machines and return them to their original condition rather than buying new machines. This a more cost effective option than investing in new machines.”
“If we extend the life of a machine, the improved performance also reduces machine downtime hours, i.e. keeping our machines more efficient and in good condition, they are rarely down. In fact we have seen a 10% reduction in machine downtime. We strive to be more pro-active and have detailed information on each machine so that the operator is aware of the smallest technical issues. In order to extend the life of the machine we are also carrying out regular ongoing tests with QC20-W ballbar. We are now able to carry out 3 plane testing with a single set-up which has reduced our maintenance inspection time by 20%.”
Regular testing is the key
Mr Kumar continues, “test data from each machine is stored in the Ballbar 20 software history function. This allows us to schedule machine maintenance, and take remedial action before part quality becomes an issue. If the machines are in good condition then the component quality will have good repeatability. By incorporating QC20-W into our maintenance program we have significantly reduced scrap and faulty product.”
The QC20-W is even used to test new machines after they are first installed, since damage during shipment from the machine OEM to the Aquasub factory could result in faulty components even from brand new machines.
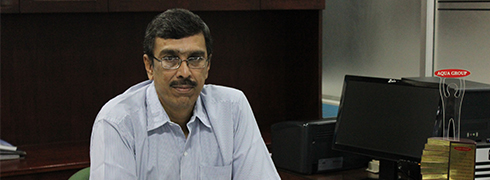
The right tool for the job
Aqua Group has an extensive product range but all are destined for critical applications for agriculture, domestic or industrial water supply. With a capacity to produce 4000 pumps a day, reliability of their 200 machine tools is of crucial importance to maintain deliveries.
Aqua Group has a policy to continually improve its manufacturing capabilities through enhancement of knowledge, skills, technology development and continual improvement. By implementing a Total Productive Maintenance programme they are ensuring that good quality practices are followed and identify scope for further improvement.
Mr Kumar explained, “We used to base our machine performance reliability on an engineer's word so the potential for human error was high. Now the QC20-W ballbar provides us with overall machine diagnostics (circularity, squareness and backlash) from a single test. All the machine data is stored in Ballbar 20 software and creates a log of information about each machine's performance that can be reviewed at the time or offline. We are no longer reliant on an engineer's memory. The Renishaw QC20-W ballbar system is the backbone of our quality system.”