Stran trenutno ni na voljo v vašem jeziku. Lahko si ogledate strojni prevod, ustvarjen s storitvijo Google Translate. Te storitve ne zagotavljamo mi in rezultatov prevoda nismo preverili.
Za dodatno pomoč se lahko obrnete na nas.
Supporting our customers' sustainability goals
We are improving battery life
Industrial Metrology case study
Machine tool spindle probing technologies are key to process automation.
Spindle probing allows data to be collected at different points in a manufacturing process to check the condition of parts and tools, and machine performance. It can also process trends resulting from environmental changes and manual interventions. This data can be used to automatically adapt processes to the current situation, to avoid producing a bad part. This helps eliminate waste, re-work and manual intervention. Measurements can also be stored for later analysis and used to help identify longer-term process improvements. CNC machine tools that use our spindle probes with radio signal transmission need a radio machine interface for the machine's controller to receive data from the probe. Our QE series radio transmission probing system acts as a combined radio transceiver and machine interface. It also provides the communication for sensors, offering reliable, automated on-machine tool setting, tool breakage detection, part set-up, and part verification. Updates to the probes' electronics and radio transmission deliver an increase in battery life of up to 400% when used with the RMI-QE interface (compared to the previous generation). This gives an industry-leading battery life of up to five years, based on typical usage.
We are proud of the technological advancements this system delivers, and, with the battery life improvements achieved, equally proud of minimising its environmental impacts.
Steve Petersen, Marketing Manager
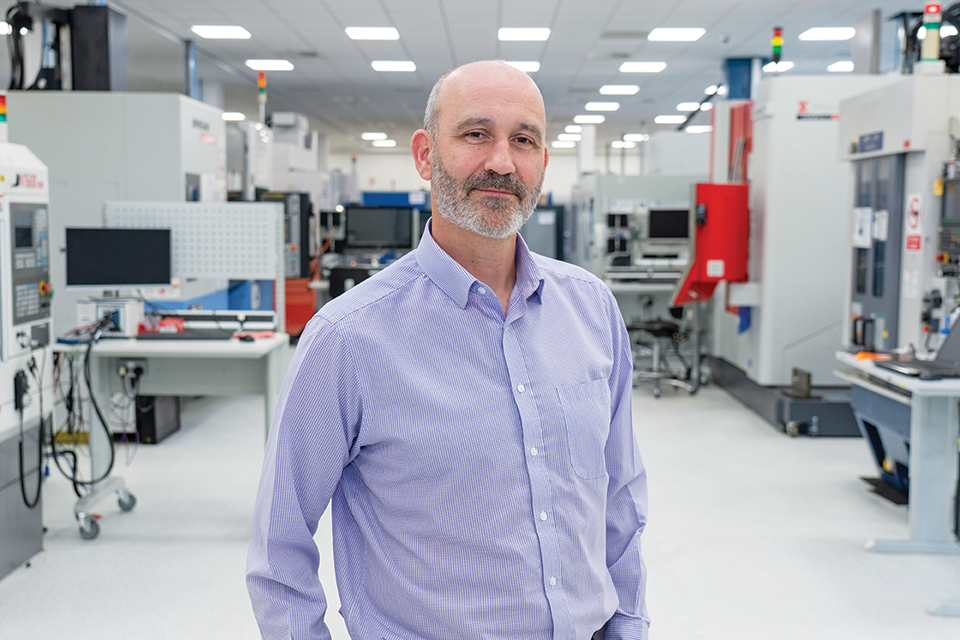
We are reducing energy costs
Position Measurement case study
The FORTiS™ encoder series has been designed to improve machine tool performance, productivity and energy consumption.
In terms of sustainability challenges, the largest source of electricity consumption over an enclosed encoder's lifetime is the compressed air that is fed through the encoder to repel contamination, known as air purge. Thanks to our new DuraSeal™ seals, the FORTiS encoder enclosure offers dramatically reduced air consumption, resulting in lower operating costs and greater system longevity. The FORTiS encoder system offers a 70% reduction in compressed air consumption compared to other optical enclosed encoders. As a result, this can reduce the encoder's attributable CO2e emissions and lower the total cost of ownership for the machine user, since less electricity is required to provide the air purge.
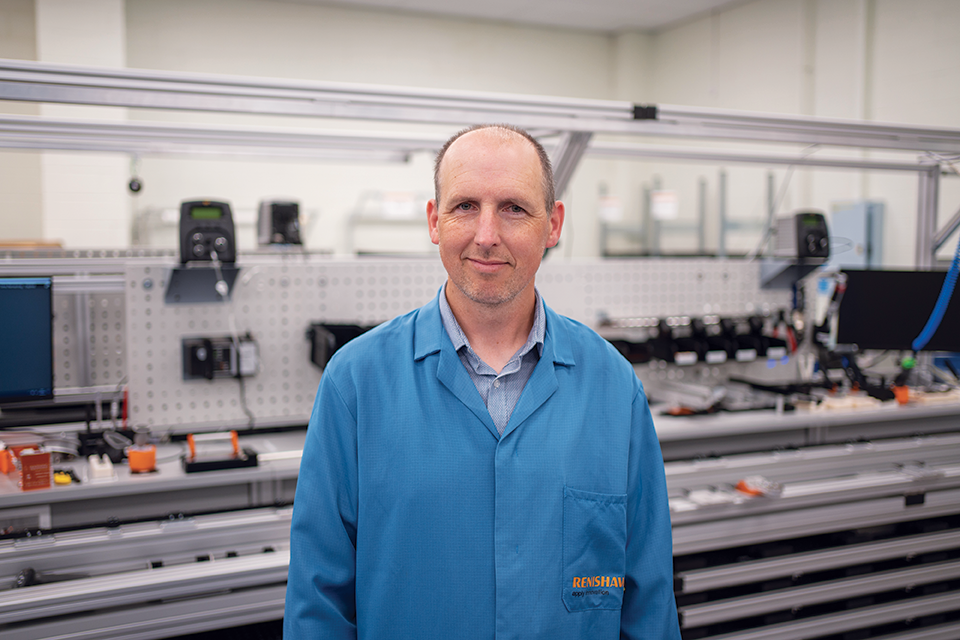
Five years of accelerated life testing have enabled the development of our new advanced DuraSeal lip seals. These offer excellent resistance to wear and machine tool lubricants, superior sealing and contamination protection.
Ian Eldred, Principal Mechanical Engineer
We are helping customers make more efficient products
Additive Manufacturing (AM) case study
With help from our metal AM technology, UK-based Domin Fluid Power Ltd (Domin) has disrupted the hydraulics industry by redesigning servo valves from first principles. This has achieved a better performing, more sustainable product at a lower price point.
Due to its inherent design freedom, AM allows Domin to build complex parts, free of tooling and with minimal operations and assembly. For example, metal AM provides the ability to design complex geometries with internal features that can significantly enhance efficiency in fluid applications. It produces parts with good strength-to-weight ratio and requires less material than conventional machining, as it only forms metal where required. “We believed that metal additive manufacturing was the final puzzle piece and were confident we could generate true industry change and make a positive impact,” explains Marcus Pont, chief executive officer of Domin. “By combining additive manufacturing with other innovations like high-speed motor control, modern electronics, big data and connected technology, there is real potential for disruption.” “Most hydraulic systems today only operate at 23% efficiency, resulting in the wastage of billions of kilowatt-hours every year,” adds Pont. “Globally, hydraulics produces twice the CO2e emissions of the aerospace industry.”*
This year, Domin installed a RenAM 500Q AM system at its new Technology Centre near Bristol, UK.
*Oak Ridge National Laboratory, Estimating the Impact (Energy, Emissions and Economics) of the U.S. Fluid Power Industry, December 2012
Over its lifetime, each of these game-changing valves has the potential to save multiple tonnes of CO2e. Using them we can spearhead the advance of the fluid power industry towards a sustainable future.
Marcus Pont, Chief Executive Officer of Domin Fluid Power Ltd
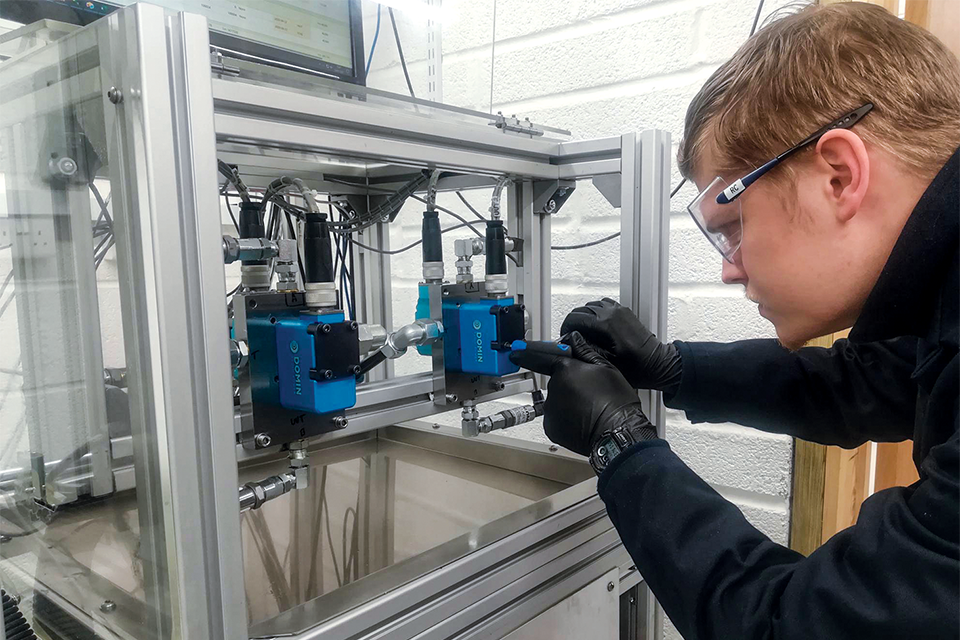
INEOS Britannia - Sailing towards a sustainable future with AM
Additive Manufacturing (AM) case study
Renishaw has supported the British challenger for the America's Cup since 2016. For the current campaign, Renishaw supplies INEOS Britannia with magnetic encoder solutions and additively manufactured parts, plus expertise in position measurement and Raman spectroscopy.
INEOS Britannia uses additive manufacturing (AM) processes to manufacture some metal parts such as the mainsheet sheave end'. AM is a versatile manufacturing technology that allows near-net shape production of a wide variety of complex functional shapes. It offers exciting new design opportunities for combining and optimising parts, potentially reducing tooling and material costs.
In this application, AM can significantly reduce the waste, scrap and embodied carbon* associated with the manufacture of parts, when compared with traditional CNC machining.
INEOS Britannia has used Renishaw's RenAM 500 AM systems to manufacture numerous metal parts on its race and test yachts.
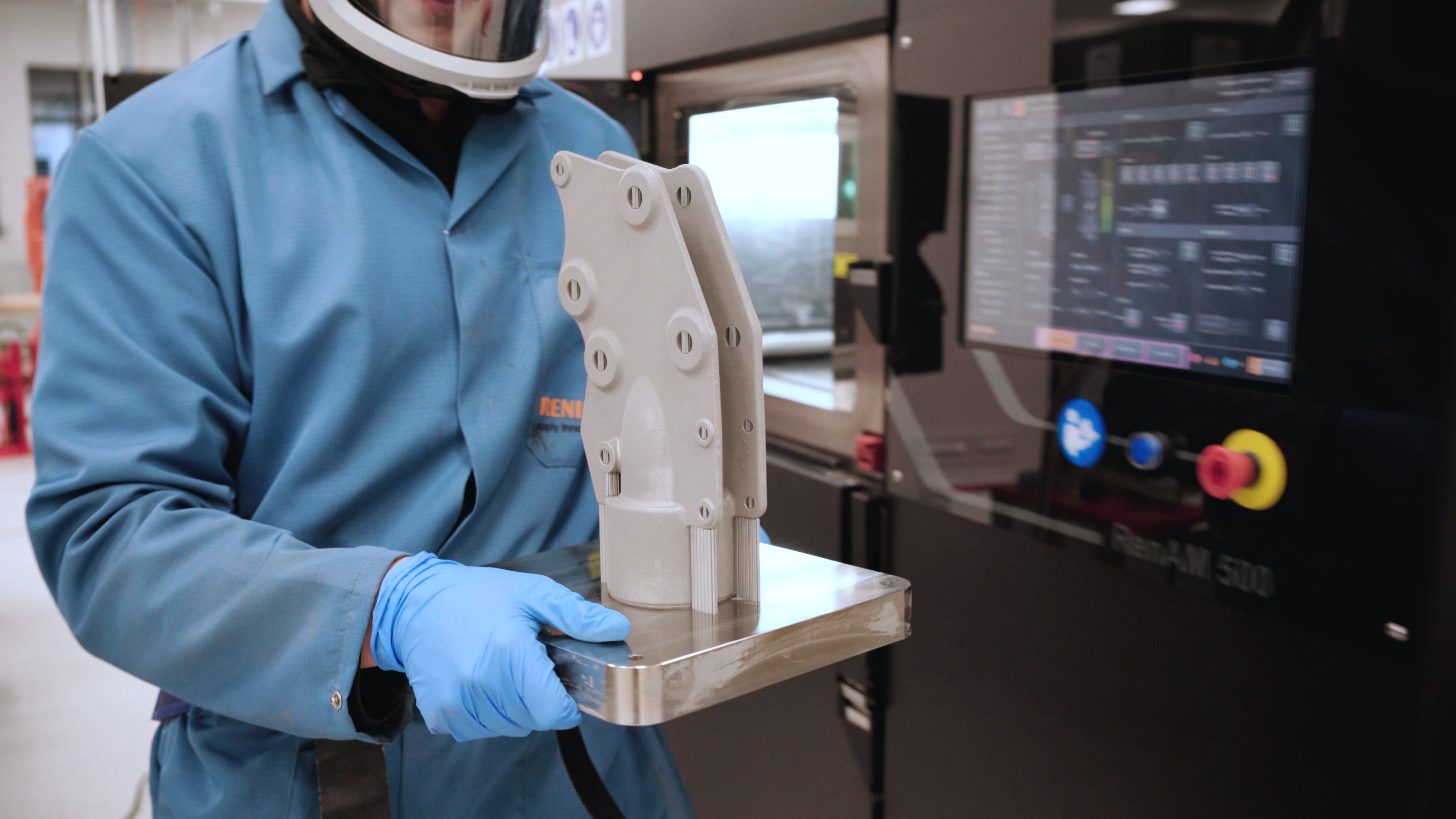