Navigation
UCC S5 troubleshooting
UCC S5 visual diagnostics
A visual indication of the system status provided by a multicoloured LED on the front panel. The LED provides assistance in diagnosing system faults.
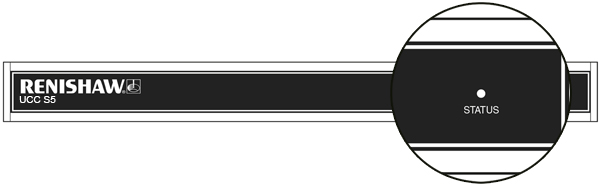
LED status key:
LED | Description |
---|---|
![]() | LED on |
![]() | LED flashing off / on |
![]() | LED flashing green / red |
![]() | LED off |
![]() | LED flashing red / blue |
LED | Description |
---|---|
![]() | No LED - no power to UCC S5 |
![]() | Continuous LED - problem with comms link - reboot UCC S5 and configure IP |
![]() | Slow flash - waiting for download |
![]() | Continuous light - download successful |
![]() | Fast flash (5 Hz) - IP configuration mode |
![]() | Slow flash - controller booting |
![]() | Internal timeout - reboot UCC S5 |
![]() | REVO-2 head has problem - DSP watchdog triggered |
![]() | REVO-2 head has problem - overcurrent detected |
![]() | Fast flash (5 Hz) - communications error - reboot required |
![]() | Slow flash - scale error - reboot required |
![]() | Slow flash - problem with download - reboot required (check file type) |
![]() | Continuous LED - UCC S5 overheated |
![]() | Slow flash - unit does not have controller ID - return to Renishaw |
![]() | Fast flash (5 Hz) - no controller ID in IP configuration mode - return to Renishaw |
Fatal faults
Situations can occur that make it inadvisable or dangerous to continue using the CMM servo system. These are known in this document and UCCassist-2 as fatal faults. A list of fatal faults are shown below and will be indicated through the user's software (for example UCCserver):
- A report of the emergency stop switch being active
- Air pressure is too low
- Crash switch operated, if fitted
- A scale reading failure
- An indicated overspeed (calculated from the rate of change of position)
- Outer limit switch active
NOTE: Other faults not classed as fatal can prevent the CMM's operation.
Motors will not engage / re-engage
Symptoms
Either the servo drives will not engage when the controller has been sent the ‘engage' command, or the drives have disengaged automatically and will not re-engage.
Possible causes (or reported causes)
After the unit is switched on and before the system is allowed to engage, it must be configured for motion (i.e. the machine, servo and move parameters must be sent to the controller).
Any of the 'fatal faults' will prevent the system from engaging. In addition, the following will disengage the servo motors:
- A reported failure from a servo power amplifier (amplifier feedback signal)
- SPA being incorrectly configured.
- The absence of the feedback signal from the motor contactor
The following list can also inhibit drive engagement or re-engagement
- The probe being deflected
- Any inner limit switch being operated or a soft limit exceeded
Tests / cures
UCCassist-2 can be used for further help with this by displaying the system status, the status bytes and signals.
The amplifier and motor contactor feedback signals can also be examined using the ‘input signals' window in UCCassist-2.
NOTE: A scale error will cause the UCC S5 to enter an error state which is not recoverable within a metrology application environment. If a scale error occurs it will be necessary to reinitialise the installation due to the possibility of lost scale counts and metrology being affected.