Innovation Matters 2022: レニショーの製造現場から
少量小ロット生産成功の秘訣
レニショーへようこそ。このインタビュー記事では、レニショーの熟練製造チームに所属するメンバー、Steve Jay と Antony Spill が有する知識を紹介します。両名は、英国にある世界有数規模の製造施設の中の 2 拠点で、主に製造プロセスの改善に取り組んでいます。そこで彼らが活用しているのが、少量小ロット生産プロセスの開発期間を短縮するための画期的なソリューションです。
Steve Jay
役職: Low Volume Production Group Leader
勤務地: Miskin
担当: 新パーツや少量品の CNC 加工生産 (対象: 4mm~4m のコンポーネント加工、積層造形によるパーツ製造)。開発中の最新システムや製品のための生産プロセスの作成。
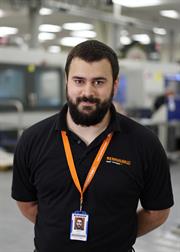
Antony Spill
役職: Low Volume Production Group Leader
勤務地: Stonehouse
担当: CNC 加工プロセスの新規導入管理。現行プロセスの見直しと改善 (効率化を促進して生産目標や品質目標を達成するため)。少量生産のロットサイズは、最大でパーツ 300 個/年。なおこのエリアでは、カスタム製品も製造。
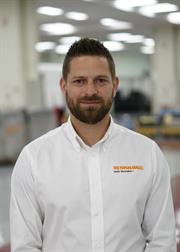
レニショーでの少量生産とパーツ製造作業について
Antony Spill: 効率的で「ローコストでも高品質を確保できる」プロセスを導入することが、我々の大きな目標です。一方で、レニショーが相手取る業界向けのカスタム製品や個別生産品のためのプロセスを短時間で構築するために、「少量」ということを我々のメインの現場にとって別物と捉えています。
少量生産に携わるオペレータたちは、新コンポーネントの製造プロセスに、新規 CAM プロセスから機械の設定と稼働まで、一貫して責任を負います。新規プロセスの立上げは 1 回の 8 時間シフト以内に完了するのが通常です。CAM ソフトウェアを使った新パートプログラムの作成、機械の設定、パーツ加工をこの時間で終わらせます。短時間で効率的なプロセスを確立するには、使用する機械を常にベストな状態にしておく必要があります。そのために我々が行っているのが、QC20-W ボールバーを使った定期ヘルスチェックです。ボールバーなどの自社製品のおかげで、機械の状態が、合格品をアウトプットできる間違いのない状態であることを把握できていますし、そういった状態を維持できています。
新しいコンポーネントに取り組む際には、我々はプログラム作成よりも、段取りと加工の開発に時間を割くようにしています。工作機械の精度が十分で、設計通りにパーツを間違いなく製造できるとわかっているからです。
Steve Jay: 我々の少量生産の規模が南ウェールズにある Miskin 工場にまで拡張したのは、2018 年のことです。大型コンポーネントの需要の高まりに対応するため、そして積層造形の生産能力を増強するためです。また、カスタム製品や特殊品の要望が増えてきたことも理由のひとつです。
機械の状態を維持する方法
パーツ加工プロセスの開発にかかる時間や稼働開始までにかかる時間を短縮するために、さまざまな機械ヘルスチェックが導入されています。
- パフォーマンスチェック: QC20-W ボールバーを使った機械キャリブレーション (複数プロセスで実施)
- ヘルスチェック: OMP400 を使用 (立形ミーリング機)
- ワーク座標系のエラーマッピング: OMP400 を使用 (複合機)
- 上/下刃物台工具計測: OLP40/スタイラスアセンブリを使用 (複合機)
メーカーを悩ます、現在の主な課題 3 点
効率化
AS: 部門の効率を高めるために、画期的なアイディアを導入しています。
品質コストの削減
AS: 主に少ない準備で長く製造を続けてスクラップ削減を目指すことで、品質コストの削減に取り組んでいます。
SJ: Miskin 工場で製造する平均パーツのサイズ、コスト、加工にかかる時間が大きくなったことで、この課題が際立つことになりました。品質コストについては、インサイクルパーツ寸法検証などのものづくりソリューションを用いて改善を継続しています。
顧客満足度の確保
AS: 目指しているのは完璧な顧客満足度です。エンドユーザーだけでなくアセンブリプロセス内の次作業でもです。
SJ: 我々がカスタム品や特殊品用にパーツを供給するとき、たとえそれが初めてのときでも、不具合のないパーツを供給できないことはほとんどありません。
最初のスクラップを避けるのが重要な理由とは。特に大型パーツの場合
AS: 結局のところ、効率と品質コスト削減の組合せです。わたしたちの現場では、形状の位置を特定したり、仕様どおりに加工されているかを確認したりするのに、プローブ計測を使用しています。大型のコンポーネントになると複数にわたる加工作業に数時間かかることもあります。そこで、位置ずれやサイズ公差外ということで NG 品になってしまうと、効率面でもコスト面でもよくありません。これはシンプルなプローブ計測で防ぐことができます。部門として達成すべき重要な課題です。
SJ: 時は金なり、です。用いる手段や扱うコンポーネントが変化を続ける中、レニショーが提唱するコンセプト「Productive Process Pyramid (ピラミッド型高生産性プロセス)」の重要性をますます実感しています。各層で着実に意識して改善を進めることで、効率化と品質コストの削減が進みます。
レニショー工場で働くことについて
AS: レニショーの工場で、いろいろな役割で働く機会を得られたのはとても幸運でした。その経験がなければ、今現在のように勤務できていなかったでしょうし、周りに経験や知識を共有できていなかったと思います。この思いは現場でみんなが持っています。現場では、チームワークやチーム内での知識共有が重要で、一人ではうまくやっていけませんからね。
現場の方針のひとつに、使用している機械プラットフォーム数の簡素化があります。機械のタイプが多いとその分トレーニングが必要になってリソースの問題に発展する可能性があります。リソースに問題が起こると、そこがボトルネックになり、供給に問題が発生する可能性があります。そこで、使用する機械やプロセスが標準化されていれば、リソースを効率的に配置できるようになります。部門目標を達成できるようになりますし、人員の配置転換が容易に行えるようになります。
最も使用する機会の多いレニショー製品とその理由
AS: わたしは、チャレンジや力を合わせて対処する問題を見つけるのが好きです。我々はソリューションを届ける存在です。そしてこの思いを部門内の全員が持てるように努力しています。部門の業務を改善するためにレニショー製品の画期的な新しい使い道を考えることは、わくわくすると同時に難しいことでもあります。ですが、レニショー製品を思うように扱えるのは非常に貴重なことです。
最近の例として、これはわたしが最近関わった中で最も満足できたことでもありますが、廃棄寸前の機械を生まれ変わらせたことがありました。レニショーのテクノロジーを駆使して機械に隠された真の問題を探り当て、確固としたソリューションを適用したのです。
SJ: 積層造形システムです。非常に優れたテクノロジーです。設計者たちの想像力をかきたててくれますし、それに生産性の高いワークセンターとして我々の部署内でも稼働しています。実にすばらしいシステムです。
少量生産を成功に導く秘訣とは
AS: 稼動時間に比較して準備時間が長いため、最初から最後まで短時間で完了するプロセスを確立しておく必要があります。例えば、工作機械が確実に精度よく動くようなプログラムの作成方法を採用するなどです。
わたしは機械のエラーマッピングに取り組んでいます。初期プロセスの開発時間を延ばさずに、最初の加工から合格品を出せるようするためです。例として、段取りのパフォーマンスが非常に悪い機械の話があります。
- 大型の複合加工機 (ツインスピンドル、B 軸、タレット)。
- 機械内で位置決め誤差が複数発生。
- この位置決め誤差を把握できていないと、段取りのパフォーマンスが低下。1 回の小ロット生産を稼働するのに平均で 8 時間 (8 時間以上かかるのが大半)。
- この非効率的な状況によって、供給上の問題も日常的に発生。
- OMP400 を導入したことで機械内で軸間の誤差を特定可能になり、誤差のマッピングの効率が向上。
- このヘルスチェックを 2 週間に 1 回実施して、位置決め誤差を検出してマクロに格納。そしてこのマクロを、新規機械セットアップ時に呼び出してワーク座標系を更新。
- このプロセスに加えて、上刃物台のプローブで下刃物台の工具を計測することで、機械の全軸間での精度を完璧に確保 (機械のエラーマッピング)。
- 平均の段取り時間が従来の半分に。生産時間と品質コストの点で非常に高い改善効果。
SJ: オペレータたちは誰もが最初に「どうやってこれを加工しよう?」と思うものです。ですが、コンポーネントや形状の寸法確認を重視してみると、まったく別のアプローチになることも少なくありません。例えばワークの向きや固定です。パーツをインサイクル計測する手段を確立し、機械から取り出す前に、パーツそのものやトラブルの原因になりそうな寸法が問題ないと確認できる。これはほんとうに価値のある技術です。
Dave Miles
役職: Manufacturing Engineering Manager
勤務地: Stonehouse、Miskin
レニショーは 1973 年の創業以来、成長を続け、製品を多角的に展開しています。ここ 20 年以上にわたって製造部門に身を置いたことで、豊富な経験ができ、さまざまな課題を体験できました。製造プロセスの改善に一心に取り組むチームと一緒に働けて、喜ばしいです。
Steve Roberts
役職: Machine Shop Manager
勤務地: Stonehouse、Miskin
レニショーに 30 年以上勤めてきましたが、その間レニショーのものづくりはすっかりと様変わりしました。工場の規模が大きくなり、世界有数の工場や施設を有して製造業をけん引する存在になっています。私個人としては、日々の生産の課題に取り組む、献身的で有能なチームの一員として働けて光栄です。顧客の納期要求に応えるべく奮闘し、我々のものづくりのノウハウをさらに蓄積できる機会を常に探しています。
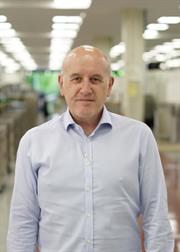
レニショーの Miskin 工場と Stonehouse 工場について
Our operations
- 加工プロセス: RAMTIC (Renishaw Automated Milling, Turning and Inspection Centre: レニショー自動複合加工機検査センター、プリズマテックコンポーネントの製造)、複合加工機 (中型パーツの単発生産)、主軸台移動型旋盤 (小型パーツの旋削) など
- 各種計測作業 (インサイクルゲージングシステム、全自動三次元測定機測定など)
- 仕上げ作業 (酸化処理、レーザー刻印、バリ取り、切削工具製造用の研削、レーザー切削)
- スタイラスの組立て設備、積層造形、エンコーダ製品、自動表面実装エレクトロニクス組立てライン (Miskin)
製造品
- レニショー製品に組み込むパーツ (Stonehouse 工場と Miskin 工場。両方の工場で類似のプロセスを構築することで、汎用性を確保し、不測の事態への備えに)
- TP20 や OMP40 といった小型プローブ用のパーツから、REVO® 5 軸測定ヘッドや RenAM 500Q 積層造形システムなどの大型製品
使用しているレニショー製品
- OMP40、OMP400、RMP60、RLP40、NC4、TS27R、MP250 などの工作機械用プローブや工具計測アーム
- QC20-W ボールバー、XL-80 レーザーシステム、AxiSet™ (機械のキャリブレーションに使用)
- Equator™ ゲージングシステムや PH10、SP25、TP20、MODUS を使用した三次元測定機
Miskin (ウェールズ)
未来型のスマートファクトリコンセプトを現行技術で実践
面積: 460,000sq ft
人員数: 550 人
Stonehouse (イングランド)
英国における最も効率的な精密製造施設のひとつ
面積: 100000sq ft
人員数: 220 人