Deze pagina is momenteel niet beschikbaar in uw taal. U kunt met behulp van Google Translate een automatische vertaling bekijken. Wij zijn niet verantwoordelijk voor deze dienstverlening en het vertaalresultaat is niet door ons gecontroleerd.
Heeft u meer hulp nodig, neemt u dan contact met ons op.
Material innovation through metal additive manufacturing
Uniform Wares partnered with Betatype to explore the advantages of additive manufacturing (AM) technology, pushing the boundaries of design in an industry traditionally centred around heritage.
The two companies worked closely together, using Design for Additive Manufacturing (DfAM) principles and AM technology to overcome limitations faced by more traditional manufacturing methods. As a result, they produced a superior quality, mesh 3D printed titanium watch strap which is featured in Uniform Wares' 2019 collection.
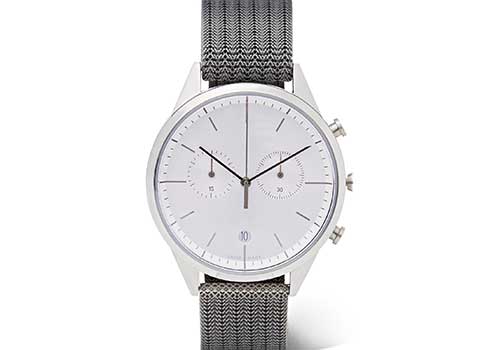
Background
Uniform Wares, a luxury watchmaker established in 2009, set out with an objective to build a brand whose entire creative output was designed and developed in its London-based studio, working exclusively with local and international partners who share the company's devotion to detail. They pride themselves on creating contemporary time pieces that embody character and distinction through intelligent design, not branding. Uniform Wares teamed up with Betatype specialists in advanced design and additive manufacturing, to design and develop a unique woven AM watch strap for their new PreciDrive M-Line collection.
Launched in October 2018, the watch strap is manufactured by combining Betatype's unique scanning technologies with Renishaw's AM250 additive manufacturing technology. Using a titanium T5 alloy material made it possible to create a strong, yet lightweight ‘metal fabric' strap which has already gained popularity and prestigious reviews from clients of Uniform Wares. Betatype and Uniform Wares have worked together for over three years, refining their woven material to mimic and exceed traditional fabric behaviour while benefiting from the mechanical strength and lightness of titanium. They continue to explore designs and technology that exploit the detail and precision that AM can offer, driving material innovation in watch manufacturing and other creative industries.
Challenge
In an industry centered around traditional designs, methods and heritage, Uniform Wares has always been an innovator, experimenting with technologies like AM to achieve more with their designs. Previous Uniform Wares watches had featured a mesh-like bracelet manufactured using more traditional methods. “We used a huge, cumbersome machine to weave steel cable into the mesh pattern, which we then had to cut to size and weld working parts onto it.” Michael Carr, Creative Director, Uniform Wares. When Betatype presented an idea that could simplify the process by allowing the woven strap to be printed in any texture or grain, incorporate new materials and produce less waste, Uniform Wares was keen to get involved.
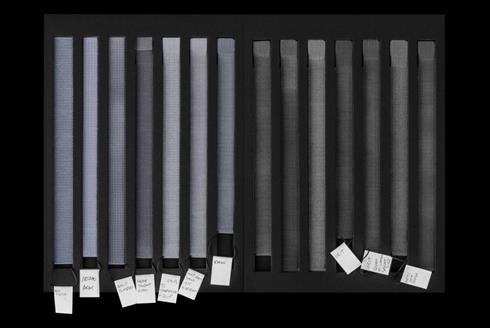
While we are always taking prompts from heritage and traditional processes in the watch and other industries, we also like to push things forward.
Uniform Wares (UK)
Solution
Founded in 2012, Betatype has worked across a variety of industries such as aerospace, automotive and medical sectors to design and develop functionally advanced components using AM. Betatype applied its unique multi-scale approach to exert greater geometric control over the watchstrap designs and used Renishaw's AM technology to bring the Uniform Wares watchstrap to life.
Taking full advantage of working together to create a design specifically for Additive Manufacturing, Uniform Wares and Betatype were able to make the most of additive technology to create a strap that was more accurate and intricate than any previous design. The bracelet is made up of over 4,000 interlocking links and weighs just 10.5 g.
The asymmetric design of these links allows each side of the strap to have a different bend radius, meaning it can easily fit over the hand, allowing flexibility, whilst remaining secure on the wrist. The strap uses microscopic ‘teeth' and a new type of directional clasp interlocking with the mesh itself, which can only be achieved using additive manufacturing, to hold the watch in place.
“Every element of the [watch] bracelet has been engineered exactly as it needs to work. The radius at which it curves, the flexibility and stiffness at each point – every link incorporates fine adjustments. It represents bespoke engineering at every point,” said Carr.
By controlling the laser's scanpath, exposure settings and material microstructure – down to the micron – of each link in the strap, Betatype was able to achieve the best possible fit and mechanical performance of the watch strap. By optimising laser powder bed fusion, Betatype's processes also mean that the watch straps can be produced in smaller batches, more quickly. Uniform Wares no longer needs to order hundreds or thousands of watch straps five months in advance – they can now order 60 and they can have them in under a week. “This is a real gamechanger for us,” explained Carr.
Working together with Betatype means that the PreciDrive M-Line collection is designed, developed and manufactured in London and finally assembled with care in Switzerland, amplifying Uniform Wares' ethos to work only with select local and international partners.
Results
With an initial objective to prove the validity of - and innovate with - AM in the watch industry, the results that Betatype and Uniform Wares achieved far surpassed any expectation. This collaboration has produced, without compromise, a commercially viable product. It is is superior in terms of quality and level of detail, and has demonstrated the power of AM and the freedom it can bring to design for manufacture.
Sarat Babu, Managing Director at Betatype explained “When we looked at all of the reviews [of the new watch strap] that were coming out, none talked about the additive manufacturing. They talked about it as a product which works and is superior in terms of the way it behaves, the quality that it provides, and that's really the measure of when you get to an end use part. It's not just that, this is an additively manufactured watch strap, it's because it's one of the best metal watch straps that you can buy today.” Betatype and Uniform Wares are already in discussion regarding future projects to continue an exciting journey of additive manufacturing and its influence on the creative industry.
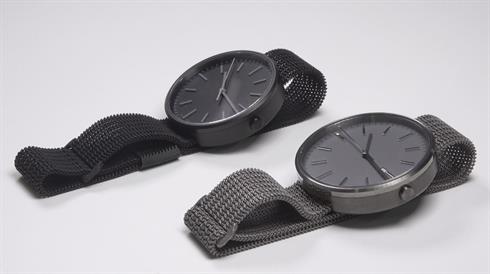