Deze pagina is momenteel niet beschikbaar in uw taal. U kunt met behulp van Google Translate een automatische vertaling bekijken. Wij zijn niet verantwoordelijk voor deze dienstverlening en het vertaalresultaat is niet door ons gecontroleerd.
Heeft u meer hulp nodig, neemt u dan contact met ons op.
Process setting
Automated setting using probing can be up to 10 times quicker than manual methods.
The controls in the process setting layer of the Productive Process Pyramid™ establish the relationships between the machine, the part and the tools before cutting starts. These automated, predictive controls ensure that the first cuts are correct.
Ensure that first cuts are accurate
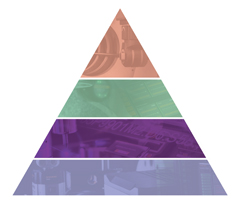
The process setting layer of the Pyramid deals with sources of variation such as the location of the part, the size of tools, and offsets on the machine, aligning the machining activities to the actual location of the part.
These are predictive controls applied just before metal cutting starts.
Tool setting establishes
- length from the spindle gauge-line to establish a height offset, and to check that length is within the specified tolerance
- diameter when spinning to establish a tool size offset
Part setting establishes
- component identification to select the correct NC program
- position of a datum feature to establish a work co-ordinate system (WCS)
- billet/component size to determine stock condition and roughing cut sequence
- orientation of a component (relative to machine axes) to establish the co-ordinate rotation
Machine setting establishes
- alignment of a rotary axis, indexer or fixturing elements required to position and hold components
- position of an indexer's centre of rotation and/or reference points on fixture elements
Predictive controls
Automated setting using probing can be up to 10 times quicker than manual methods, freeing up more time for cutting metal.
Probing is also predictable – you'll know how long setting will take and can plan accordingly.
Setting processes that use on-machine probing can be fully program controlled, so that skilled operators are no longer needed to take measurements, make calculations and input offset changes.
Renishaw's workpiece inspection probes, tool setters and Productivity+™ software are essential tools for fast, automatic and repeatable set-up of metal cutting operations.
Documents
-
Brochure: Meetoplossingen voor de beheersing van uw procesproductiviteit [nl]
Vergroot uw productierendement samen met de specialisten in procesbesturing
-
Witboek: De sterksten overleven - het belang van de procesbesturin [nl]
In zware tijden proberen fabrikanten hun operationele kosten te verlagen, maar ze zijn niet altijd in staat om dat op te lossen door productievere machines te kopen. Als die route afgesloten is, zijn er dan nog mogelijkheden om de kosten drastisch te verlagen zonder bestaande machines te vervangen? Dit artikel bespreekt vier gebieden waarop aanzienlijk te besparen is voor bedrijven die bereid zijn om hun bewerkingsprocessen op een andere manier te besturen.