Inspectietijd turbineschoepen met 50% verkort
Europea Microfusioni Aerospaziali, een producent van turbineschoepen in Morra De Sanctis bij Avellino in Italië, voert deze controles nu uit met behulp van de PH20 5-assige tasterkop van Renishaw. Ten opzichte van controles met een 3-assig systeem zijn de cyclustijden tot 50% verkort.
Achtergrond
Europea Microfusioni Aerospaziali (EMA) behoort tot de Rolls-Royce Group, een wereldleider in de productie van aandrijfsystemen voor civiele en militaire vliegtuigen, schepen en onderzeeërs en van turbines voor industriële energieproductie.
In Morra De Sanctis heeft EMA onder meer een fabriek van 20.000 m2 waarin het bedrijf ultranauwkeurige stator- en rotorschoepen maakt in speciale legeringen voor hoge-, midden- en lagedruktrappen van turbines voor zowel de burger- als de militaire luchtvaart. Verder worden er schoepen gemaakt voor industriële turbines waarmee elektriciteit wordt opgewekt.
Meer dan tweederde van EMA's productie is bestemd voor gerenommeerde klanten in de luchtvaartindustrie in Italië en elders in de wereld, waaronder moederbedrijf Rolls-Royce, AgustaWestland, Ansaldo Energia, Avio, Turbocare, Siemens en MAN. Ongeveer 25% van de militaire vliegtuigen in de wereld is uitgerust met Rolls-Royce motoren, en vele daarvan bevatten EMA producten.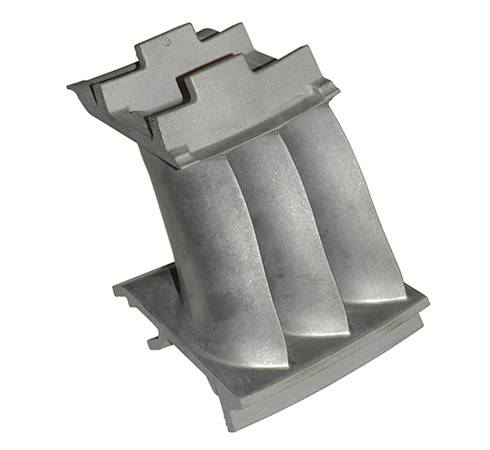
Sinds de invoering van de Renishaw PH20 tasterkop kunnen we aanzienlijk besparen op zowel de meettijd als het aantal styluswissels die tijdens de controlecyclus uitgevoerd worden. Het gebruik van de MODUS™ software heeft ook onze programmeertijden verkort en geoptimaliseerd. Het is ons gelukt om de cyclustijden te verkorten met 30 tot 50%, en in sommige gevallen zelfs met meer.
Europea Microfusioni Aerospaziali (Italië)
Uitdaging
Turbine- en vliegtuigmotorschoepen worden gemaakt van hoogwaardige legeringen die bestand zijn tegen zeer hoge temperaturen en drukken. Hun vorm is meestal complex, om de efficiëntie te maximaliseren en de spanning en materiaalmoeheid te verlagen. En toch worden ze gemaakt met een van de oudste productietechnieken die de mens kent: gieten.
EMA heeft een brede reeks microgiettechnologieën geperfectioneerd, waaronder die om schoepen te produceren met enkelvoudige kristallen metaallegering. Het bedrijf is ook gespecialiseerd in het verlorenwas-microgietproces, dat begint met het creëren van wasmodellen op basis van metalen mallen.
Deze wasmodellen worden vervolgens gecoat met een keramisch materiaal dat hoge temperaturen kan weerstaan. De was wordt verwijderd en de keramische omhulling vormt de mal voor de superlegering. Eenmaal gestold en afgekoeld ondergaan de gegoten onderdelen een warmtebehandeling en worden ze nabewerkt. Alle componenten worden gecontroleerd op maatnauwkeurigheid en structurele integriteit, met behulp van ultrageluid, röntgenstraling en vloeistofpenetratietests.
Een efficiënt proces ontwerpen om de maatnauwkeurigheid te controleren van turbine- en vliegtuigmotorschoepen is een uitdaging, want het gaat om complexe productgeometrie en controle van echt iedere schoep.
Oplossing
Ingenieur Vittorio Caggiano, manager kwaliteitscontrole: "We moesten een oplossing vinden waarmee we de efficiëntie van het dimensionale verificatieproces konden verbeteren naar een groter aantal producten per tijdseenheid.”
Om dit te bereiken had het bedrijf de keuze uit investeren in nieuwe meetmachines, of verkorten van de cyclustijd per meting en zo de capaciteit verhogen van de al bestaande meetmachines in de fabriek.
“Tot een paar jaar terug werkten onze CMM's met 3-assige PH10 tasterkoppen met indexering, die hun beperkingen hadden wat betreft beweging en de tijd voor styluswissels", vertelt Vittorio Caggiano. Deze beperkingen kwamen voort uit de complexiteit van de producten, aangezien in elke meetcyclus vaak van stylus gewisseld moest worden.
"We hebben nauw samengewerkt met technici van Renishaw om een betere oplossing te vinden. Ook hebben we onze producten naar Renishaw in Turijn gestuurd voor meettests. Na die tests concludeerden we dat de beste oplossing was om te investeren in nieuwe meer flexibele en efficiënte PH20 5-assige tasterkoppen, en eveneens in de MODUS meetsoftware. Renishaw bracht de nieuwe tasters aan op onze bestaande meetmachines, en de mensen van Renishaw SpA schreven er vijftig meetprogramma's bij toen ze hier bij ons training gaven.”
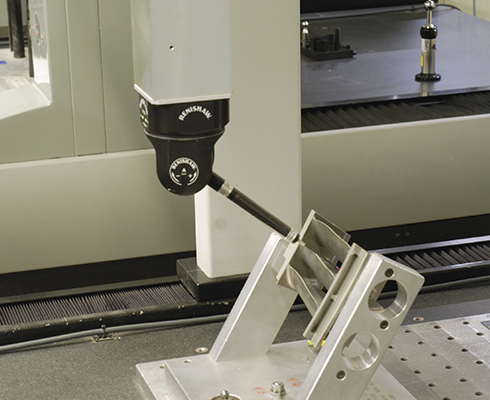
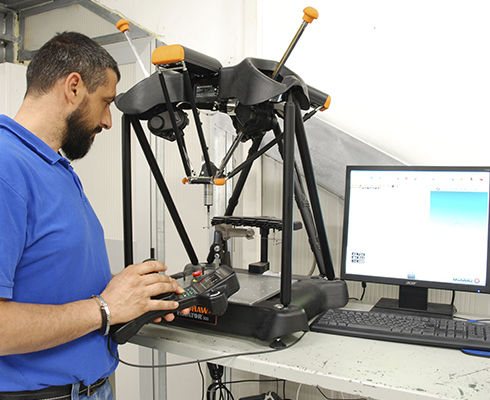
Resultaten
"Over het eindresultaat zijn we bijzonder tevreden", voegt CMM-programmeur Maurizio Rullo toe. "Sinds de invoering van de Renishaw PH20 tasterkop kunnen we aanzienlijk besparen op zowel de meettijd als het aantal styluswissels die tijdens de controlecyclus uitgevoerd worden. Het gebruik van de MODUS software heeft ook onze programmeertijden verkort en geoptimaliseerd. Het is ons gelukt om de cyclustijden te verkorten met 30 tot 50%, en in sommige gevallen zelfs met meer!”
EMA investeerde verder in een Renishaw Equator™ flexibel meetsysteem, waarmee het bedrijf de geometrie en vorm van grote series onderdelen snel en efficiënt kan controleren.
“Dankzij de Renishaw Equator konden we alle benodigde controles voor bepaalde componenten samen pakken, terwijl we die vroeger uitvoerden met diverse meetinstrumenten. Het resultaat is dat we de controletijden van in grote series gemaakte onderdelen sterk verkort hebben", zo besluit Maurizio Rullo.
Renishaw PH20 en MODUS software
De PH20 heeft unieke bewegingen om meetpunten op te kunnen nemen door alleen de tasterkop te bewegen en niet de CMM-structuur. Met alleen de snelle roterende bewegingen van de kop worden sneller punten opgenomen, met betere nauwkeurigheid en herhaalbaarheid. Bovendien is dankzij de 5-assige beweging geen tijd meer nodig om de kop te indexeren.
Dankzij zijn onbeperkte positionering kan de PH20 optimaal bij vormen komen, zodat wisselen van stylus minimaal nodig is. Door de 5-assige simultane bewegingen zijn op de CMM grotere producten te meten, aangezien rond het product slechts minimale ruimte nodig is voor meetkoprotaties. De PH20 lijnt zichzelf automatisch uit met het coördinatensysteem van het product, wat stylusbotsingen voorkomt en nauwkeurige opspanning overbodig maakt.
De voor de PH20 ontwikkelde unieke ‘afgeleide kalibratie’-techniek bepaalt de meetkoporiëntatie en tasterpositie in één actie, zodat onder allerlei hoeken na elkaar gemeten kan worden.
De PH20 kan zichzelf automatisch uitlijnen met het werkcoördinatensysteem, wat botsingen voorkomt en ingewikkelde opspanning overbodig maakt.
Dit exclusieve snelle kalibratiesysteem bepaalt de oriëntatie van de meetkop en taster in één actie, en maakt het mogelijk om onder alle hoeken te meten.
Dankzij de MODUS meetsoftware zijn complexe metingen en het programmeren van meetcycli eenvoudiger geworden. Met de software zijn offline geavanceerde programma's rechtstreeks vanuit CAD te ontwikkelen, met simulatie, botsingdetectie en controlefuncties op het scherm voor het tasterpad. Dit maakt het mogelijk machinestilstand te minimaliseren: de programma’s zijn klaar vóór gebruik op de machine, en het testen kost maar minimale tijd of is helemaal niet aan de orde.
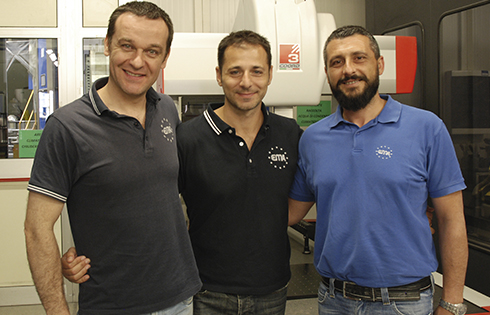
Overgenomen uit een origineel artikel van Ernesto Imperio (Tecnologie Meccaniche)