Denna sida finns för närvarande inte på ditt språk. Du kan
översätta
den automatiskt
med Google Translate. Vi ansvarar inte för att tillhandahålla denna tjänst och
vi har inte kontrollerat översättningsresultaten.
Kontakta oss om du behöver ytterligare hjälp.
Reliability
Discover what reliability means to us. Every encoder we design is built to last and put through rigorous tests that go far beyond normal operating conditions.
How far do we test our optical encoders?
One good example is that we operated an ATOM™ readhead at temperatures down to -40 °C (-40 °F). We then added 10 g of vibration and 100 g of shock, just for good measure. Such tests prove the mechanical and design integrity of the product. Of course, we do not do that to every product before it leaves the factory, but instead each ATOM encoder system is continuously tested in-process. It is automatically assembled followed by a final 103 point check to make sure it will not let you down. No wonder our failure rates are so low, and our product is used in so many reliability-critical applications where failure is not an option.
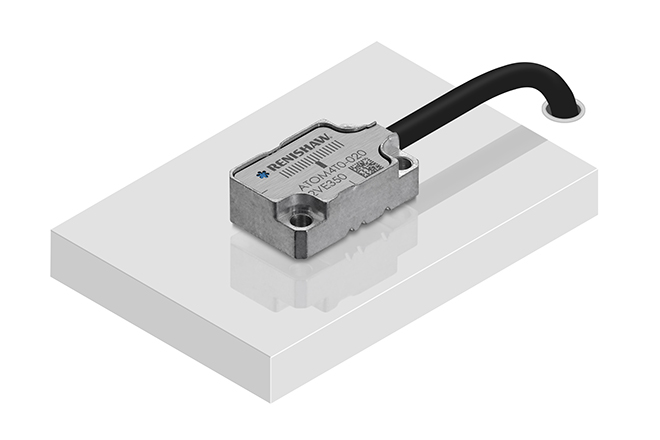
Advanced optical design
All Renishaw incremental encoders feature unique filtering optics for high immunity against dirt, scratches and light oils that can make other encoders miscount. ATOM, TONiC™, VIONiC™ and QUANTiC™ readheads augment this with dynamic signal conditioning, including Auto Gain Control (AGC) and Auto Offset Control (AOC) for even greater performance on dirty scale.
High-flex, UL-recognised cables
Renishaw cables are specially designed for use in highly-dynamic applications, involving rapid moves and constant flexing. Under such demanding conditions, the encoder cable must perform faultlessly for many years. Renishaw use only cables that meet our stringent acceptance criteria, such as the TONiC cable that we specify for 20 million flex cycles at 20 mm bend radius.
Materials
There is no need to put up with fragile glass scales. Renishaw make some of the world's highest accuracy scales, yet uniquely we graduate directly onto tough engineering materials such as ZeroMet™ and hard martensitic stainless steel. Not only does this enable much easier handling during installation, but it also ensures far greater resilience to damage in service.
Total quality assurance system
All key manufacturing stages, from PCB assembly and machining of bodies to cable assembly and final readhead assembly / test are carried out in-house. Unlike many other encoder companies, our scales are also made in-house. This philosophy ensures we maintain total control of product quality at every step.

Fully CE approved
There are two levels of CE approval for noise immunity - all Renishaw readheads achieve the more stringent EN 61326-1:2013 level, which ensures the readhead does not miscount under even the harshest RFI conditions.
Comprehensive warranty
In the unlikely event that something does go wrong, you'll be fully supported by Renishaw. With wholly-owned sales offices in every major industrial country in the world, our trained technicians can help fault-find your machine, no matter where it is located.
If a Renishaw encoder is at fault, we will replace it right away, investigate the failure and send you a comprehensive and honest report into exactly what happened, why it happened and what we have done to ensure it never happens again.
High reliability light sources
Renishaw encoders use only highly-reliable LED light sources. Under continuous operation, however, all LEDs tend to exhibit natural degradation and reduction in light output over extended periods of time. The TONiC readhead is an excellent example of how Renishaw guard against this; any reduction of light output is compensated by a DC light servo which monitors the light output and adjusts the LED brightness accordingly.
Our optical encoders are available in a variety of configurations, including incremental or absolute, and can be linear, rotary, or designed for partial arc applications.
Contact our sales team today
Get in contact with your local office to find out more information and speak to an expert.