Denna sida finns för närvarande inte på ditt språk. Du kan
översätta
den automatiskt
med Google Translate. Vi ansvarar inte för att tillhandahålla denna tjänst och
vi har inte kontrollerat översättningsresultaten.
Kontakta oss om du behöver ytterligare hjälp.
Renishaw calibration systems essential as ‘déjà vu’ hits rebuild specialist Murrall & Lang
The ideal machine, with a bed length of 5-metres, would allow pendulum machining, thereby increasing production. However, new machines of this type were costly and resulted in the company approaching rebuild specialist Murrall & Lang for a solution. Ten years later, it was ‘déjà vu' for the Birmingham-based company, when it welcomed the opportunity to once again re-manufacture the machine, but this time employing the capabilities of Renishaw's calibration and machine tool performance testing systems.
The initial rebuild
Murrall & Lang had already modified a 2-metre machining centre to accommodate pendulum machining in the summer of 1989 and convinced Dana Spicer of the cost benefits. With a contract signed, a Cincinnati 20HC 2500 (2½ metre) travelling-column horizontal machining centre was found in the USA that would machine these parts, if equipped with a suitable front base.
The volume of the axle components dictated that a pallet shuttle system would be economic, allowing unloading and loading whilst machining continued. To accommodate this, Murrall & Lang designed a special shuttle table with two index tables and fixtures, and a CNC movement of 2.5m from one position to the other. Suitable guarding protected the operator. Therefore, in addition to the usual horizontal axes of X (2500mm), Y (1000mm) and Z (600mm) and the shuttle axis, the machine has two indexing axes giving a total of 6 CNC axes. This configuration was arrived at after joint discussions when the machine was first modified in 1990.
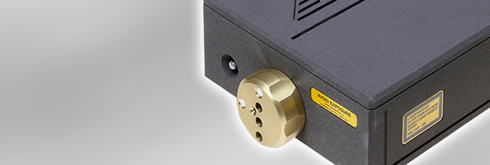
Ten years later....
After producing axles for nearly a decade and having questioned the ability to maintain the machine, Dana Spicer - having once again considered new products, which still proved very costly - decided to have the machine re-manufactured by Murrall & Lang for a second time. Having experienced the benefits of Renishaw's QC10 ballbar systems in the 1990's, Murrall & Lang had no hesitation in utilising this technology and purchasing Renishaw's ML10 laser calibration system to aid the re-manufacture ‘as new', of the Cincinatti HMC for a second time.
Partner, Bob Murrall explained. “We had successfully produced a machine to Dana Spicer's tolerance specifications in 1990 using a second-hand Hewlett Packard (HP) calibration system from a leading supplier. Today, that equipment is neither cost-effective nor comparable to the technological capabilities of the Renishaw systems.”
“It was our experience of the QC10 ballbar system, that led us to invest in the ML10 laser calibration equipment,” added Mr Murrall. “The ballbar is so reliable, it automatically identifies, quantifies and prioritises machine tool errors. In seeing it used here, many of our customers, including Dana Spicer, have subsequently invested in the technology.”
The ballbar is so reliable, it automatically identifies, quantifies and prioritises machine tool errors. In seeing it used here, many of our customers, including Dana Spicer, have subsequently invested in the technology.
Murrall & Lang (UK)
Complete rebuild
The Y2K re-manufacturing process included a complete mechanical rebuild, with all worn parts being reconditioned or replaced, a complete rewiring, the fitting of new digital axis and spindle drives, and a new Siemens 840D CNC control. The process took less than six months and fully met customer specification. To improve reliability, the customer wanted to maintain accuracy by axis calibration and compensation. This required the use of the Renishaw laser calibration system; part of Murrall & Lang's quality control system.
“When you are re-manufacturing a machine, your alignments should be well within achievable levels of adjustment, allowing the alignments set by the original manufacturer to be achieved. In fact, the QC10 ballbar and ML10 laser system allow us to achieve tighter tolerances than was possible when the machine was first manufactured. Whatever we attain here, we can reproduce at the customers' premises. The Renishaw ML10 laser calibration system is portable, easy to use and has built-in temperature compensation, allowing our customers to machine components far more accurately than once possible,” continued Mr Murrall.
Probing for variations
At Dana Spicer, the 20K hp Cincinnati machine, with spindle speeds of 3300rpm, is fed by two 30-tool chain-based magazines. Axle beams are machined from forgings which tend to vary in size due to the forging process. To obtain the best metal conditions, once the component is mounted in the fixture, a spindle mounted Renishaw MP700 high accuracy probe is used to check length and rotation. Corrections are applied automatically to find the component centre, and if necessary to rotate the program dimensions, so as to produce the best component from the forging.
“The rebuild option allows a company to purchase a specific machine at a third of the cost of a new machine. More importantly, the accuracy of Renishaw calibration systems allows us to guarantee achievable tolerances better than the initial machine tool specification,” concluded Bob Murrall.