Navigation
Motor engagement
Motor engagement via SPA connector
The UCC AI will begin to engage the servo motors when instructed to do so by the host computer or via the engage button on the MCU, if all the operating functions are in a safe and acceptable condition.
Listed below are possible causes for the motor engagement to fail:
- The system has not yet been configured for motion (i.e. the machine, servo and move parameters have not been sent to the controller)
- A fatal fault has been detected
- The emergency stop system has been activated
- A PICS ‘stop' signal is detected within the system
- An open outer limit switch
- A present or previously present scale reading fault
The process is in two stages, amplifier enabling and contactor energising, with protective delays between each stage.
Analogue amplifier enabling
The UCC AI will first ensure that all its motor demand signals are zero and will then try to enable the power amplifiers by asserting the ‘enable amps‘ signal (servo power amplifier / E-STOP socket, pin 4 or 21).This 'enable amps' signal will be held on for 100 ms to allow the ‘amps OK' signal, from the servo power amplifier, to become valid (the ‘amps OK' signal produced by the amplifier control circuits is an indication to the UCC AI that the servo power amplifiers are not faulty). If this signal does not become valid (i.e. pin 23 of the Servo power amplifier / E-STOP socket, is not pulled low) the controller will abandon the engagement process. The 'amps OK' is invertible, therefore pin 23 of the Servo power amplifier / E-STOP socket, would need to be pulled active.
If no error is detected then the UCC AI will wait for a further period of 1 second before beginning the next stage, to allow the amplifiers to settle after any initial transients.
The diagram below is an example of the recommended circuits that can be used to drive the power amplifier enable inputs and to generate the 'amps OK' signal. The circuits that are used in the installation will vary depending on the amplifiers requirements but must pull the ‘amps OK' input (pin 23) down if all amplifiers are operating correctly.
If the user wishes to signal amplifier failures individually to the main computer, it is recommended that the uncommitted user inputs (machine I/O socket) are used for this purpose.
Wiring to the servo power amplifier / E-STOP socket
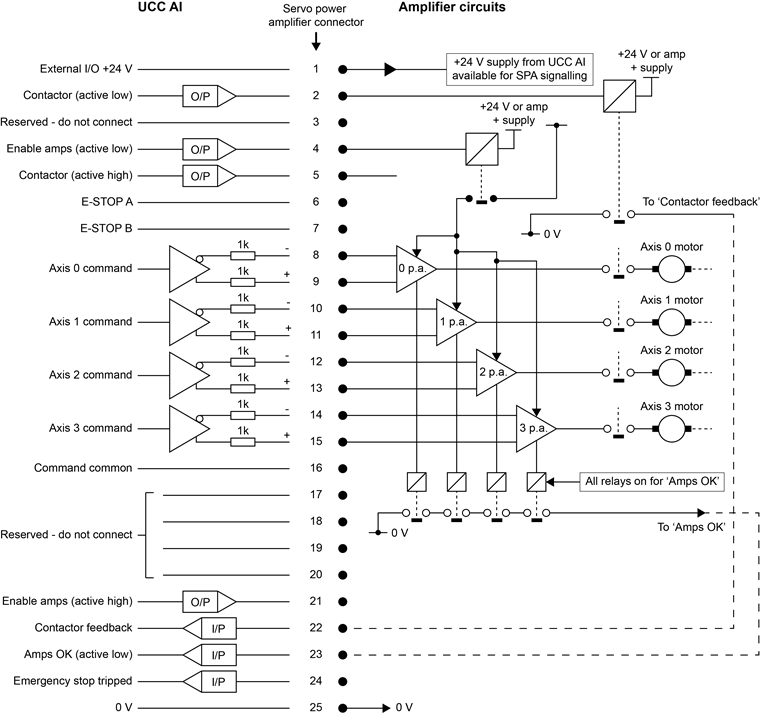
Contactor energising
After establishing that the amplifiers are working correctly, the UCC AI will assert the 'contactor' signal (pins 2 and 5 of the servo power amplifier / E-STOP socket), this should be used to signal the servo power amplifier to apply power to the motors. The UCC AI will keep this output signal asserted for 3 seconds during which it expects the ‘contactor feedback' input (servo power amplifier / E-STOP socket, pin 22) to be pulled low to indicate that the motors are now powered.
If the ‘contactor feedback' signal is not received in time, the contactor (pin 2 and 5) and the enable amps signals (pins 4 and 21) are de-asserted and the motor engagement process is stopped.
If the ‘contactor feedback' signal is received within this 3 second window, the controller keeps all motor commands at zero for another 0.2 seconds before allowing the servo system to begin operating. This is intended to give further protection against sudden machine movements when engaging the motors.
Motor command signals
The UCC AI generates complementary motor velocity command signals for each axis (axis 0 = pins 8 + 9, axis 1 = pins 10 + 11, axis 2 = pins 12 + 13, axis 3 = pins 14 + 15).
Each motor velocity signal is capable of a swing of ±10 V centred on a zero-velocity command of 0 V. A motor command common connection is provided to define this 0 V level (servo power amplifier / E-STOP socket, pin 16, diagram above).
The motor command common signal is also connected to the 0 V and the UCC AI chassis at four star points within the UCC AI.
The UCCassist-2 setting up process will help the user to set the power amplifier gains such that the maximum command signal (± 10 V) will produce 120% of the required maximum axis speed.
If complementary signals are not required, either of the motor command signals may be used as a single ended input, referred to the motor command common line.
Each motor command signal has a series resistor of 1 kohm to protect the UCC AI from inadvertent damage. This will reduce the drive signal to the power amplifiers if their inputs are of low impedance.
Safety
The UCC AI can stop CMM movement using any one of three methods; ‘Contactor' output pin, ‘Enable amps' output pin, the analogue ‘command' outputs. It is strongly recommended that the amplifier is configured to use all three methods of control so that back-ups exist should a fault occur with one method. A recommended configuration is shown in the diagram ‘Wiring to the servo power amplifier / E-STOP socket'.