Automated workpiece set-up boosts forestry equipment manufacture
To meet rising demand for its market-leading range of forestry equipment, Tigercat Industries Inc. aimed to boost production efficiency and output at its manufacturing facility in Cambridge, Ontario, Canada.
By automating workpiece set-up using Renishaw machine tool probing systems and software, the company achieved 75% reduction in setup times and a 40% increase in available time.
Background
A manufacturer of premium quality forestry equipment, Tigercat prides itself on providing the lowest cost per tonne timber harvesting solutions. From its base in Ontario, Canada, the company exports its products to busy logging operations throughout the world.
With a strong engineering culture, Tigercat thrives on the design and continuous improvement of all kinds of forestry machinery.
Its broad product range features both tree-length and cut-to-length machines and includes feller bunchers, skidders, loaders, harvesters and fellers. They are big, strong, robust machines, typically weighing in at 25 tonnes.
Since logging crews often need to rely for example on a single drive-to-tree feller buncher for continuous operation, machine reliability is always a paramount concern. Just one machine down can cause a whole felling operation to stop. For Tigercat this means that robust construction, high uptime and a long useful lifespan are key product design requirements.
At its Southern Ontario, Cambridge site, Tigercat manufactures the larger steel components for its wheel-based forestry equipment, most notably its feller bunchers, a gold standard in the logging sector since 1992. Busy production line operations include laser cutting, machining, manual and robotic welding and assembly.
Challenge
In the face of increasing global demand, Tigercat set itself the task of increasing production efficiency and throughput through greater use of automation. A wide-ranging review of existing production processes identified workpiece set-up as a particular area for improvement.
Plant-wide standardisation on a new automated workpiece probing solution would need to accommodate the very large scale and diversity of Tigercat's thick gauge steel high-tolerance parts, as well as the range of different production line operations.
Probes would need to be capable of accurately inspecting critical, hard-to-reach features and be robust enough to operate in close proximity to new automated welding cells.
At the same time, the company also wanted to utilise the MazaCheck health check diagnostic capabilities of its Mazak Versatech V100N, a production-critical 5-axis double-column machining centre for very large parts.
We settled with just one company that we felt comfortable with and that fits perfectly with our engineering culture. That company was Renishaw. They provide good technical support, their on-site technicians are very knowledgeable, and I'd describe their equipment as top-notch.
Tigercat Industries Inc. (Canada)
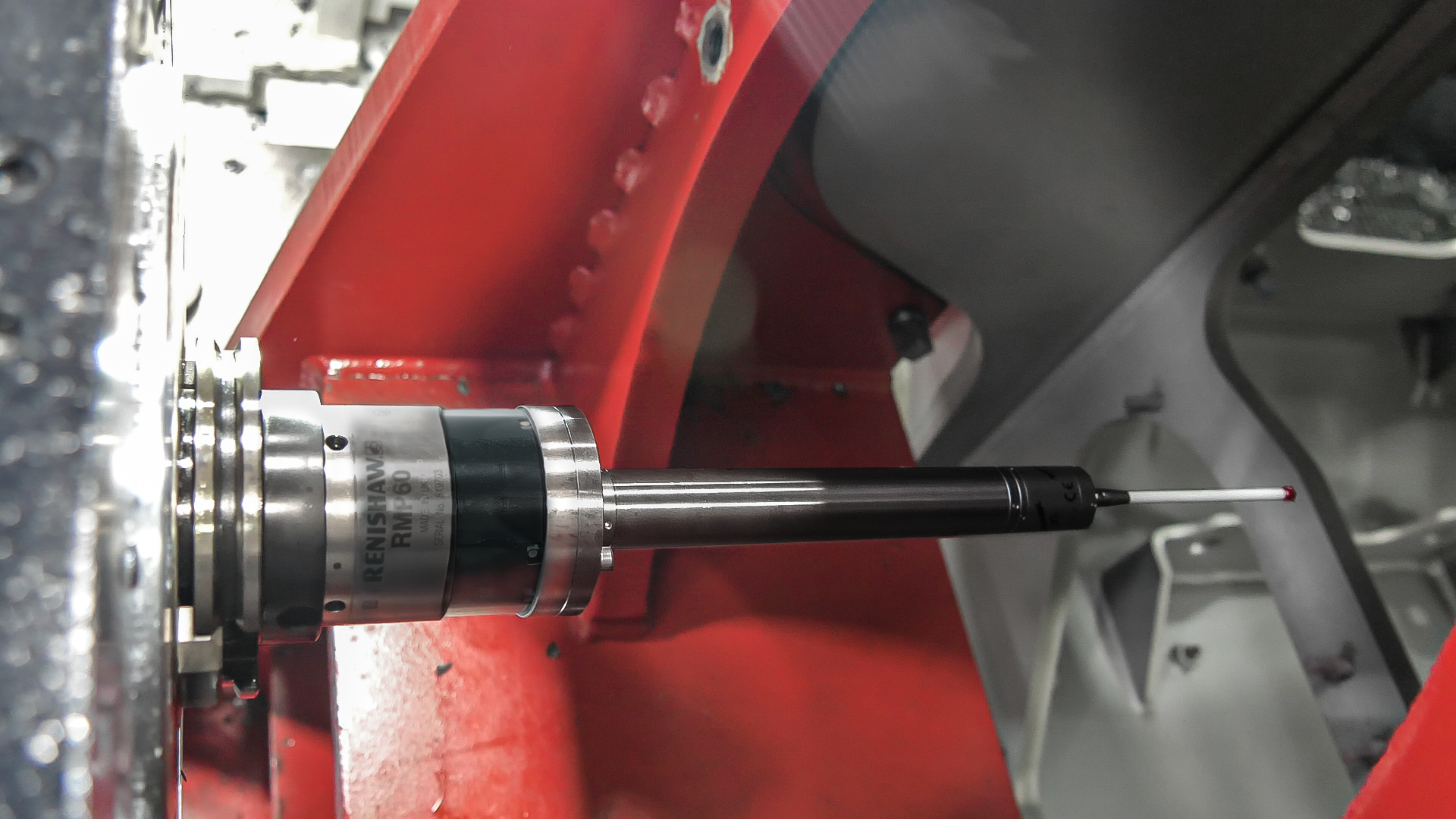
Solution
A review of a wide range of machine tool probe technologies led to the selection of Renishaw's high-accuracy touch probes with radio transmission and, PC-based probing software.
David Hodder, Machine Shop Supervisor, Tigercat said, “We were actually looking at several different companies for the provision of the machine probing systems we needed. We settled with just one company that we felt comfortable with and that fits perfectly with our engineering culture. That company was Renishaw. They provide good technical support, their on-site technicians are very knowledgeable, and I'd describe their equipment as top-notch.”
Designed to aid workpiece set-up and inspection on multi-tasking machines and machining centres, the flexible RMP60M spindle-mounted radio transmission probe was deployed by Tigercat throughout its Cambridge production line. Drawing on Renishaw's wide range of compatible ceramic stem and ruby ball styli, the company was able to develop automated set-up solutions, customised to meet the specific demands of Tigercat's many large and varied workpieces.
The RMP60M's proven kinematic resistive probe mechanism, combined with its unique frequency hopping spread spectrum (FHSS) radio transmission provided Tigercat with a robust solution capable of tolerating any signal interference effects from welding processes and overcoming any line-of-sight challenges.
Operating in the 2.4GHz waveband, the RMP60M machine probe is compliant with radio regulations in all major industrial markets. It offers a variety of activation options, an adjustable trigger force and measurement repeatability of ±1 μm 2σ.
Renishaw RMI-Q combined radio transceiver and machine interfaces were employed throughout the plant, converting signals from the RMP spindle probes into voltage-free solid state relay outputs for the machine controllers.
For Tigercat's Mazak Versatech V100N 5-axis machine, an RMP600 probe was specified. A compact, high accuracy touch probe equipped with the same FHSS radio communication capability as the RMP60M, it provided Tigercat with all the benefits of automated workpiece set-up along with the ability to measure complex 3D part geometries to unrivalled sub-micron levels.
The probe uses Renishaw's RENGAGE™ technology (a combination of proven silicon strain gauges and ultra-compact electronics) and delivers high-accuracy measurement even when using long and custom styli – ideal for Tigercat's applications which often require measurement of features in hard-to-reach locations.
Finally, Renishaw's simple-to-use Productivity+™, PC-based software was used to seamlessly program and integrate inspection routines within the V100N machining cycles.
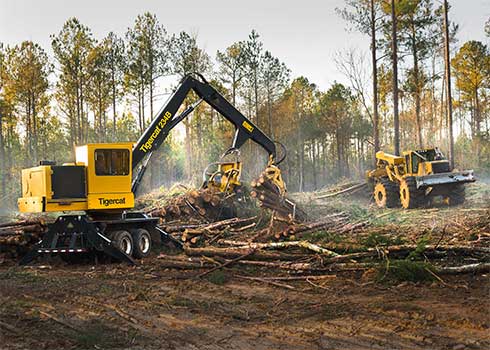
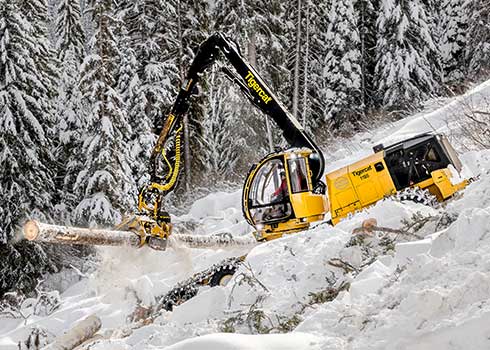
Results
The new machine probing systems log and record every part they touch. If a part cannot be aligned correctly or does not conform to specification, the operator is immediately notified. Data can be collected to track machine and process performance over time.
Since Tigercat partnered with Renishaw on automated machine probing the company has achieved a 40% increase in weekly production figures, and expects further improvements to be made going forward.
There is also now a greater consistency in day-to-day part production and a new-found freedom to be able to move machine operators across machining centres when production demands dictate. The risk of human error has been virtually eradicated and operator safety has been improved by eliminating manual operator interventions.
Over time, Tigercat has evolved its use of probing from basic part set-up (pre-machining) to fully integrated, in-process control and part verification, all before the part leaves the machine bed. It has led to improvements across the board, in terms of machine cycle times, part quality and operator safety. It is also being used for machine health checks, giving Tigercat even greater confidence that all of its production processes are perfectly up to specification.
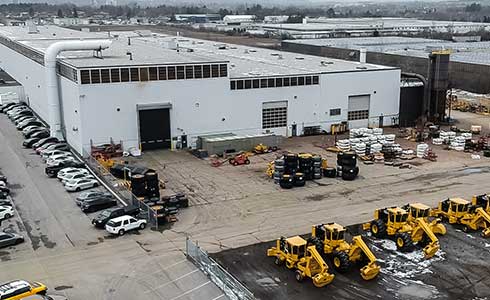