Science, research and analysis case studies
Renishaw is well known for its sector-leading investment in continual research creating strong market positions with innovative products.
Challenge: To replace legacy encoders on the two positioning axes of the main one-metre-diameter Ritchey-Chrétien telescope at the Wise Observatory.
Find out moreChallenge: Precisely control a system of mirrors in order to steer and focus a beam of synchrotron X-rays onto an experimental sample.
Find out moreChallenge: Combatting Abbe error in automated calibration systems.
Find out moreChallenge: To produce cyclindrical test masses for the world space mission MICROSCOPE to an accuracy of 2 µm to 3 µm.
Find out moreChallenge: To reliably differentiate between counterfeit and genuine gemstones while ensuring the gems are undamaged.
Find out moreChallenge: Accurately produce replacement brackets for the Hawker Typhoon aircraft cockpit.
Find out moreChallenge: Support of hexapods designed for the advanced component validation testing in the manufacture of weather satellites.
Find out moreChallenge: Test samples ranging from components for jet engines to medical syringes.
Find out moreChallenge: To etch Ionoptika's full company logo 20 μm wide on a typical metallic screen mask.
Find out moreFind out more
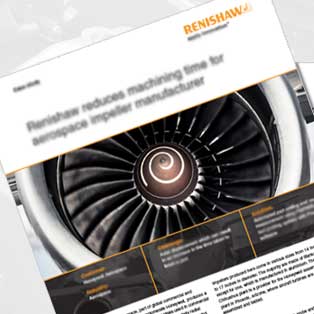
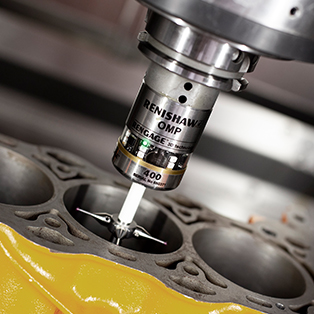