Diamond styli for metrology applications
Renishaw OPTiMUM™ diamond styli
Support high performance scanning for the toughest applications. Benefit from increased working life and reduction in recalibration and inspection downtime.
The ultimate solution for precision measurement
Harnessing diamond, one of the hardest known materials on earth, OPTiMUM diamond styli are the pinnacle of stylus technology for metrology applications. The diamond-coated styli give you unparalleled wear resistance, no material build-up, and increased flexibility for your most challenging of inspection demands.
We have designed the diamond-coated range of styli to specifically cater for the most aggressive scanning applications. Ruby, Silicon Nitride and Zirconia are all commonly used materials for stylus tips and have been used for many years, performing well in most applications. However, in recent years, technological developments have increased the use of novel and harder materials. Using OPTiMUM diamond styli to perform scanning inspection of parts made with these materials, removes any concerns about stylus wear.
Now available to buy online!
We now offer a range of diamond-coated styli to suit various applications on our Online store.
With stock held locally, benefit from our quick lead times.
Watch our OPTiMUM diamond styli in action
Unlocking potential: Why choose diamond-coated styli?
OPTiMUM diamond styli are the ideal solution for scanning applications that would normally show signs of material wear or pick-up.
To complement the REVO® system's high-performance scanning capabilities, a range of commonly used RSP2 approved styli has been created.
We have also created a range of the most common M2, M3 and M5 styli for other scanning applications.
Using industry findings, we have seen diamond out perform other ball materials in certain scanning applications. Below we have listed some applications where diamond-coated styli perform exceedingly well.
Automotive
Metal spray bore lining: The automotive industry relies on molten metal spraying for cylinder liners, requiring precise measurements, but can be highly abrasive. Diamond-coated styli can last over 200km compared to ruby's 36km.
Aerospace
Large scale aircraft components: In aerospace, diamond-coated styli are preferred for scanning large engine parts due to their superior durability over ruby, significantly extending their lifespan.
Medical
Medical grade titanium orthopaedic implants: Ruby and other conventional stylus materials, have been found to pick-up material and cause part marking during scanning. Diamond-coated styli have been found to significantly reduce this issue.
Technical ceramics
Ceramics such as silicon carbide have many benefits but are extremely hardwearing. Scanning with diamond-coated styli has been proven to last significantly longer than ruby equivalents in these applications.
How can OPTiMUM diamond styli benefit you?
When it comes to inspection challenges, the stylus you choose can make all the difference. Factors like access to workpiece features, inspection times, and probe performance are heavily influenced by the stylus you use.
One of the standout features of our diamond-coated spheres is their ability to maintain their roundness and resist material build-up or premature wear, even when scanning abrasive materials or soft alloys. This not only extends the working life of the stylus but also reduces the need for recalibration and minimises inspection downtime.
The most flexible stylus in your metrology toolkit
Enjoy peace of mind knowing that you always have the right stylus for the job. Some workpiece materials are not compatible with typical stylus tip materials. For example: some types of aluminium cause severe build up on the stylus tip while scanning, which will impact measurement results.
Diamond-coated styli have been shown to perform as well as traditional styli types on a wide range of workpiece materials, all the way from hard and abrasive ceramics to soft Aluminium alloys. Upgrade your metrology toolkit with diamond-coated styli for lasting durability and performance regardless of the inspection challenge.
The Renishaw styli range is comprehensive. Please refer to our precision styli for metrology page for more information.



Avoid premature stylus wear
Scanning on rough or abrasive surfaces can lead to unwanted wear and tear on your stylus. The interaction between the workpiece and the stylus ball can cause abrasive wear, resulting in damage to both.
To avoid this issue, consider using OPTiMUM diamond styli. The highly durable balls can withstand scanning on abrasive surfaces without losing their shape or integrity.
No material build-up
Scanning on soft surfaces, such as aluminium, creates material build-up on the stylus ball.
When a ruby ball is used to scan aluminium, the two materials are attracted to each other and material is passed from the softer surface to the harder surface. This means that aluminium is deposited on the surface of the ruby ball, changing the shape of the ball and meaning that your stylus will need to be changed frequently.
With OPTiMUM diamond styli, workpiece material does not adhere to the ball and any small deposits can simply be wiped off.


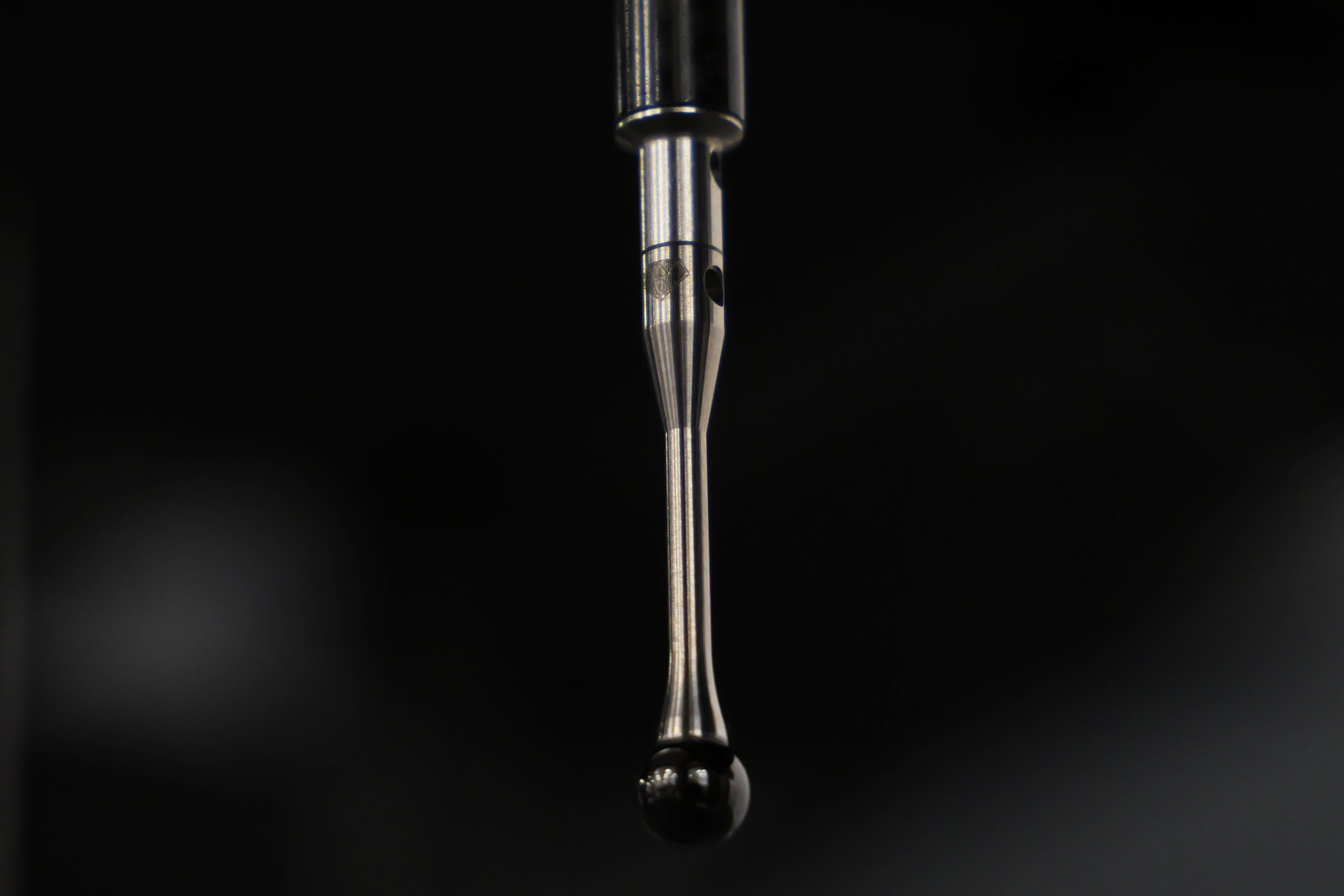
Saving you money long term
When considering your stylus choice you may want to understand other factors above just the purchase price. Considerations such as the usable life of the stylus, the cost of labour and CMM downtime costs all factor into the total cost of ownership. Diamond-coated styli are being proven to work harder for longer with less interventions, saving you money in the long run. In some cases, the ruby alternative might work out to have a higher cost if it needs to be replaced frequently.
Diamond cost saving example (scanning a hard material):
In a practical application, a traditional ruby-tipped stylus began to wear out after just one month of aggressively scanning a hard material, which started to negatively impact the metrology results. In contrast, a diamond-coated stylus was shown to last an entire year under the same conditions without any degradation in performance.
Ruby | Diamond | |
Cost of stylus | £50 | £430 |
Lifetime of stylus (months) | 1 | 12 |
Labour and CMM cost (per hour) | £80 | £80 |
Time to replace and recalibrate stylus (minutes) | 15 | 15 |
Overall cost in 12-months | £840 | £450 |
Buy online
Head over to our Online store to buy from our comprehensive range of precision styli.
Technical papers
Additional reading
Contact our sales team today
Get in contact with your local office to find out more information and speak to an expert.