Equator-X™ dual-method gauge for shop floor inspection
Equator-X™ 500 gauge: two systems in one
The new Equator-X dual-method gauging system brings unique capability to the shop floor with its dual measurement functionality; Absolute and Compare. Users can select the optimum inspection mode for their process challenge, effectively deploying two systems in one.
Absolute mode
In Absolute inspection mode, the Equator-X gauge performs as a high-speed production CMM, providing fully traceable inspection results (ISO 10360-2 = 2.1 μm + L / 300).
Rapid measurement at scanning speeds of up to 250 mm/s, without the need to maintain master parts, is particularly useful for manufacturers with:
• high part variation
• low to medium production volumes
• high frequency of inspection
Compare mode
When used in Compare mode, the Equator‑X gauge delivers ultra-fast, highly repeatable inspection with scanning speeds up to 500 mm/s and ±2 μm repeatability across a wide temperature range. This is particularly useful for high volume manufacturing of parts, where throughput is key and environmental temperature changes are a challenge.
Comparison method
The comparison method is based on the traditional comparison of production parts to a reference master part. A master part is measured to generate a master data set. Each production data set is then compared to the master to determine the actual size of the part and whether it is within user defined tolerances. In factories with wide temperature variation, simply re-master and the system is ‘re-zeroed', ready for repeatable comparison to the master.
Equator-X 500 gauging system's key benefits
Throughput
The Equator-X system is capable of absolute scan speeds of 250 mm/s and comparator speeds of up to 500 mm/s, far higher than conventional 3-axis CMMs. By measuring faster, inspection capacity is increased. This high performance enables inspection to keep pace with machining operations.
Assurance
The Equator-X system provides fully traceable in-process verification of parts to ISO 10360 standards, providing assurance when moving measurement out of the measurement lab and onto the shop floor. The Equator-X gauge provides continuous validation of the production process with real-time feedback.
Flexibility
The ability to choose between two methods of measurement on a single device enables the user to select the optimal method for their application. For example, the absolute method for large varieties of parts or the comparison method for wide variation of environmental temperature.
The compact and lightweight design, without the need for compressed air, makes it easy to deploy exactly where needed, either in-line or at-line.
Precision and speed redefined
The Equator-X system is engineered to deliver high-speed motion with unparalleled measurement accuracy. Designed around the dynamically stiff hexapod structure, inertial drive forces act only in tension or compression significantly reducing speed related errors seen in conventional 3-axis CMM systems.
In addition, the drive and metrology frames are independent, making it possible to optimise the drive frame for high speed motion without compromising metrology performance.
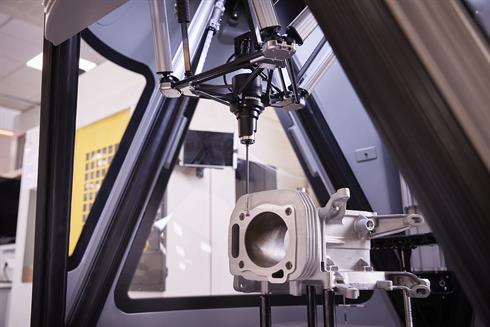
The drive frame
The Equator-X achieves its remarkable speed and performance using six linear motors in a hexapod configuration. These drives apply force directly to the moving probe platform, avoiding the dynamic bending and twisting present in traditional CMMs.
Drives and positional feedback encoders are located above the working volume, away from major sources of contamination, preserving a high level of performance even in a shop floor environment.
The metrology frame
The carbon fibre metrology frame is both rigid and lightweight, essential for maintaining high-speed motion and accuracy. Performance is further enhanced by applying a thermal expansion signature for the carbon fibre struts, which is used to build an overall system thermal compensation model.
Each metrology strut incorporates the RESOLUTE™ absolute optical encoder system; absolute position is known immediately upon switch on.
The probing system
The industry-standard SP25M probe is a highly versatile scanning system allowing users to scan for form, size and position. The SP25M probe with SM25-2 scanning module delivers exceptional performance over the entire stylus range from 50 to 105 mm effective working length for straight styli, and up to 83 mm for cranked styli.
The 6-port rack supplied with Equator-X enables automatic and repeatable changeover between different stylus arrangements.
Equator-X™ gauging systems
Equator-X gauges have been designed for throughput, assurance and flexibility on the shop floor.
Download the product brochure and datasheet to learn more about the dual-method capability of the Equator-X system.
All the information at a glance.
Equator™ gauging systems range for industrial manufacturing
The Equator-X dual-method gauge is part of Renishaw's expanding range of gauging systems for industrial manufacturing.
Powerful software features – the MODUS™ IM software platform
The Equator-X system comes as standard with the MODUS IM software platform, featuring an intuitive and feature rich operator interface coupled with the latest MODUS IM programming software.
Integrating a comprehensive suite of applications on a unified platform, MODUS IM software delivers unparalleled convenience and robust performance.
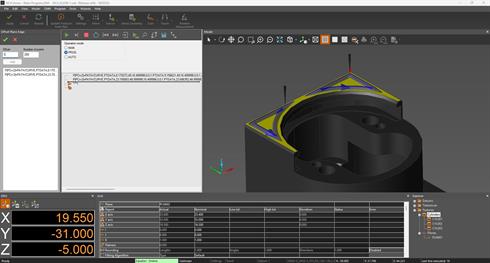
MODUS™ IM DMIS Programmer application
The MODUS IM DMIS Programmer application provides full inspection programming functionality. It supports Equator-X in Absolute or Compare mode and allows the creation of .CAL files for Calibration mode, providing flexibility and the ability to produce turnkey inspection programs.

MODUS™ IM Environment Manager application
The MODUS IM Environment Manager application creates an accurate virtual environment to mimic real-life setups, including the measurement probe configurations available, how those probes are stored in the racks, the styli, calibration equipment and other required information.
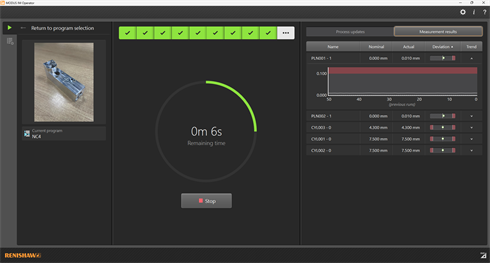
MODUS™ IM Operator application
The MODUS IM Operator application provides an intuitive interface for operators to execute programs, displaying only information relevant for that purpose. Additionally, the generic interface links to helpful applications in the MODUS IM platform and displays essential information, such as remaining program runtime, measurement results for the current run and pass/fail status of the previous 10 runs.
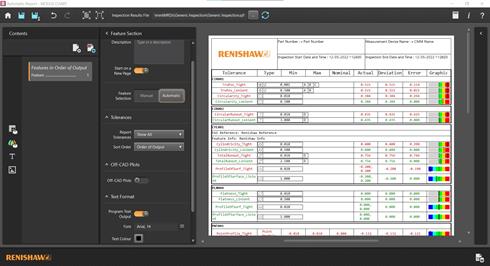
MODUS™ IM CHART application
This standalone application clarifies metrology data by displaying graphical information on the true location on the part using QIF XML files and the part CAD model.The MODUS IM CHART software application creates bespoke PDF reports for viewing and storing measurement results. All standard results tables and form plots are available, along with unique functionality to superimpose points onto a CAD model, reducing the potential for manual errors interpreting results.