Renishaw’s RESOLUTE™ absolute encoder supports ITRI breakthrough in multi-axis rotary table design
The term ‘5-axis machining' typically refers to the ability of a CNC machine to move a part or tool on five separate axes at the same time. The machine tool has an indispensable role in modern industry and has recently benefited from the popularity of 5-axis machining centres that greatly enhance flexibility in product design, by enabling precise and detailed machining of complex mass-produced parts.
Rotary tables and machine tools
Everyday items such as smartphone cases and shells for tablet PCs, alongside other metal bodies for consumer electronics, are processed with these advanced machine tools. As multi-axis machine tool technology matures, demand for rotary tables with enhanced accuracy and rotational speed is rising. Taiwan's Industrial Technology Research Institute (ITRI) has addressed this market trend by developing an advanced dual-axis rotary table with integrated Renishaw RESOLUTE absolute rotary encoders and Panasonic serial communication protocols for direct interfacing with Panasonic drives and controllers.
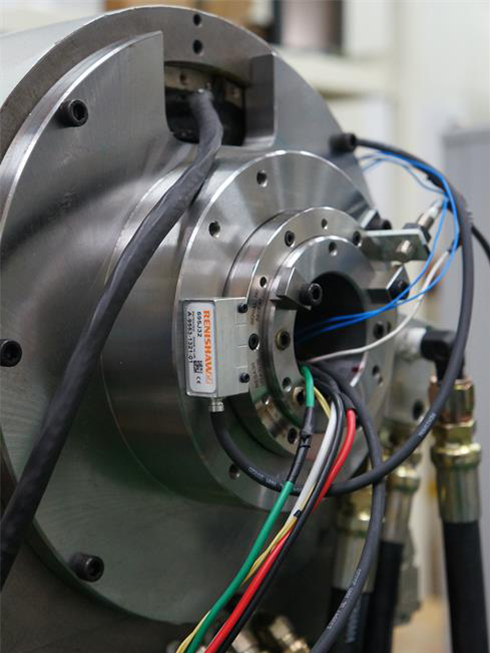
The rotary table is a key part of the machine tool, particularly for complex machine tool operations such as drilling, milling and turning. Machine tool manufacturers have adapted their product offering to suit the processing requirements of customers. Rotary tables allow scalable processing by adding a fourth or fifth axis to the traditional three axes of a CNC machining centre. Modern 3-axis machining centres require multiple setups each with its own fixturing requirements, as the workpiece is static, whereas 5-axis machines enable the user to effectively machine on five sides of a workpiece (top, front, rear, left and right) in one clamping, which significantly reduces total cycle and setup times. On-machine probing may also be applied to reduce set-up time, enhance automation and maintain the accuracy of critical components.
ITRI's senior engineer on the project, Mr. Kuan-wen Chen, outlines their motivation: “Rotary tables on the market are either uniaxial or biaxial (dual-axis) and comprise a workpiece table, external housing, main bearing, servo motor and drive components, an encoder and braking system. In order to reduce costs, all of the components except the servo motor and encoder were either developed in-house or locally procured. After several years' development, the overall build cost of the current ITRI design, when compared with competing international brands, is over 50% lower and our ultimate goal now is to transfer these technologies and solutions to local manufacturers to help them develop competitive rotary tables with high cost-performance (CPI).”
ITRI's rotary table features a 360° full rotation axis and a 170° tilt axis, both with their own direct-drive (DDR) motor which provides high-torque, high-rigidity, low wear and zero mechanical backlash. A RESOLUTE readhead and RESA rotary ring is installed on each axis providing 20-bit resolution and compatibility with Panasonic servo drives and an ITRI-developed controller. The resulting overall positioning accuracy is ±10 arc seconds and repeatability is ±5 arc seconds with a maximum system angular resolution of 0.001° (3.6 arc seconds). The rotary table (Ø250 mm) generates torque values from 170 Nm to 300 Nm, about the rotation axis, and 245 Nm to 440 Nm about the tilt axis.
Mr Kuan-wen Chen, senior engineer, Industrial Technology Research Institute (Taiwan)
ITRI selects RESOLUTE for its DDR application
For ITRI's application, the encoder readhead and scales needed to be compact enough to fit inside the motor housing as an integral part of the servo / mechanism. Mr. Chen continues: “In selecting the encoder system, volume was an important consideration which necessitated an ‘open' type encoder as enclosed variants have external housing, increasing bulk, and are generally not suitable for installation in a DDR mechanism. Although machine tool environments are generally contaminated with metal swarf, oil and coolant, enclosing an open encoder within the motor eliminates any related problems. Moreover, RESOLUTE's high level of ingress protection (IP64) provides further assurance.”
RESOLUTE is one of the few compact, lightweight and high-specification encoders with built-in support for multiple industrial serial protocols. The readhead captures a near instantaneous image of a coded measuring scale, which comprises a single data track with a non-repeating barcode-like strip of 15 μm wide light and dark lines, with low cyclic error to ±40 nm and excellent immunity to scale contaminants. RESOLUTE performance facilitates excellent positional stability leading to smoother velocity control and, hence, better surface finish of a machined workpiece.
Improved production efficiency
The adage: ‘time is money' is especially true with today's shorter product-life cycles, product diversification and fierce competition. Manufacturers are in the pursuit of quality products to meet customers' needs while continuing to enhance productivity and efficiency with a view to minimizing the time-to-market (TTM) for new product launches. As Mr. Chen explains: “Rotary table speed can significantly influence production costs; for example: on a large-scale production line, with a daily throughput of tens of thousands of units, any delays would clearly result in increased overall costs. Absolute encoders, in contrast to incremental types, capture position information on demand and can restart after machine stoppages without first homing to a datum, which allows the machine tool axes to simply resume from the same position after tool changes and setups - greatly reducing the overall production time.”
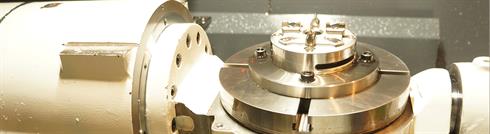
Customized programs
ITRI is committed to the development of new technologies for industry but, as is the case for all leading innovators, the development process inevitably encounters some challenges. Mr. Chen concludes: “We had decided to build a competitive rotary table and in view of the friendly relations, over many years, between ITRI and Panasonic and experience of their products - we opted to use a Panasonic servo-drive but could not find an open absolute encoder on the market that met our specifications while being compatible with Panasonic serial protocols. We contacted Renishaw and they were willing for us to jointly, with Panasonic, develop Panasonic serial protocols for RESOLUTE, which allowed the creation of Panasonic Taiwan's first direct-drive rotary table. We have a long-standing relationship with Renishaw and find their after-sales support to be excellent; we have also purchased their XL-80 laser interferometer.”
Renishaw's products and expertise are well-respected in the machine tool industry. Leading products provide solutions for tool setting, broken tool detection, component set-up, in-cycle gauging and first-off component inspection.
About ITRI
Founded in 1973, Industrial Technology Research Institute (ITRI) is a non-profit R&D organization specialising in applied research and technical services, with the aim of innovating a better future. ITRI is dedicated to keeping industries competitive and has played a vital role in Taiwan's economic growth.
The institute cultivates a number of strategic partnerships with high-profile companies and has overseas offices in Silicon Valley, Tokyo, Berlin, Moscow, and Eindhoven. Its efforts in technological innovation have been recognised by prestigious honours such as the Wall Street Journal's Technology Innovation Awards and R&D 100 Awards.