On-machine scanning probes with SPRINT™ technology
Unlock the potential of high-speed, high-accuracy, on-machine scanning probes with SPRINT technology from Renishaw. Our unique scanning probe for CNC machine tools captures exceptionally accurate 3D data, taking your manufacturing processes to the highest level.
Enhance your manufacturing processes with on-machine scanning
With unique 3D sensor technology, the OSP60 scanning probe with SPRINT technology provides the ultimate probing capability for users of CNC machine tools.
Incredibly responsive to surface variation and capable of detecting sub-micron movement at the probe stylus tip, our scanning probe captures 1,000 true 3D data points every second. Offering precision scanning and point measurement capability, it is the ideal solution for a diverse range of industrial applications.
Discover its unbeatable benefits:
- Rapid part measurement. Scanning provides incredible time savings with on-machine inspection and job set-up, increasing profitability and productive machining time.
- Determine feature form. Determine surface high-point / low-point or full feature form measurement.
- In-process control. Capture workpiece measurement results and keep on-machine processes under control, automatically. Output results for further analysis, or for quality assurance purposes.
Flexible and versatile probing
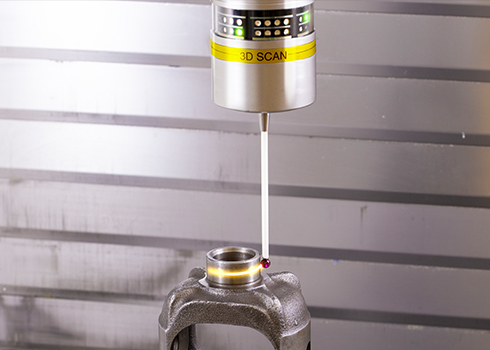
On-machine scanning opens the door to probing applications that were previously impossible or cycle-time prohibitive. It gives the ability to capture more detailed information, during manufacturing processes, than ever before.
Providing highly accurate 3D touch-trigger measurement capability coupled with high-speed, high-density 3D scan data, Renishaw scanning technology allows you to optimise overall cycle times and increase throughput of existing machine tools.
The OSP60 machine tool probe is an incredibly flexible solution. It can perform part set-up, in-process verification, 3D fitting, adaptive machining, and surface condition monitoring all using the same stylus configuration. Make the next step in your productivity journey and incorporate on-machine scanning onto your machine.
The results we have gained from the investment have far exceeded our expectations. Our accuracy in fine milling of bladed disk is more than four times better and the related labour costs have halved.
Technopark Aviation Technologies
One probe, unlimited capabilities
High-speed part set-up
Use touch points or scanning cycles to rapidly set-up your workpiece. Use the results to set or update work co-ordinate systems. Critical for high-volume manufacturing environments such as automotive, medical and mass-market electronics.
3D feature fitting
Measure 3D features such as cones, cylinders, spheres, or circular sections using multiple scan paths. Use resulting data to perform a fitting operation before machining. Provides a flexible scanning strategy for parts with interrupted or incomplete features.
3D surface capture
Perform rapid inspection of complex, free-form component geometry that is common in the aerospace and medical industries. Such as blade leading and trailing edges, impellers, tibial trays and femoral joints. Also, highly applicable in the power and energy sector.
Adaptive machining
Generate component-specific cutting toolpaths for near-net-shape parts such as castings. By adjusting the nominal toolpath point, it can match the true shape of the scanned component. Ideal for deburring and chamfer-cutting operations and dramatically simplifies copy-cut applications.
Surface condition monitoring
Dedicated measurement macros determine component surface condition and detect excessive waviness, surface peaks, and steps. Essential for sealing and mating faces in applications where leak protection is critical.
Machine health check
Verify machine tool performance in less than one minute. Integrate cycles into CNC machining programs to provide confidence in machine condition and performance capability before critical manufacturing operations.
Innovative SPRINT technology
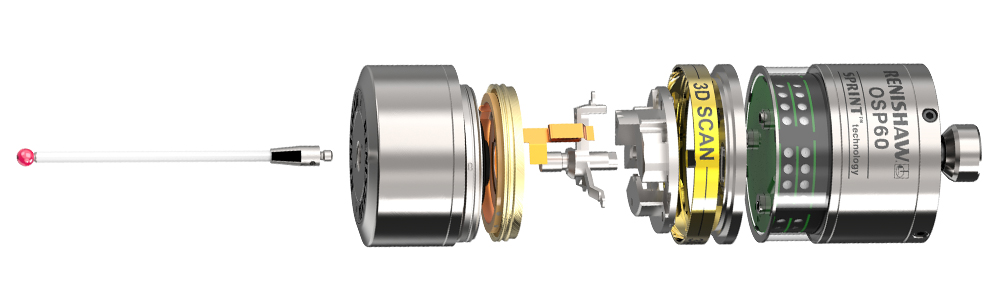
Based on a dual planar spring design, the OSP60 with SPRINT technology measures the full 3D deflection magnitude, and the XYZ direction components. This allows the probe to be responsive to resurface variation, enabling accurate high-speed measurement of complex free-form and prismatic surfaces.
Two concentric rings are installed within the probe assembly: one fixed to the probe body; the other fixed to the stylus mount, which then moves with the stylus. Capacitance measurements between the circuits on the rings allow the probe to accurately record stylus tip deflections.
Powerful scanning software
Suitable for use in a diverse range of industrial applications, the OSP60 offers a flexible approach to programming. Options include traditional macro-based applications, CAD/CAM-style solutions, and graphical user interfaces (GUIs). This breadth of choice makes on-machine scanning an accessible solution irrespective of programming experience.
All programming options provide prismatic measurement support as standard. Additional packages, designed to support specific industrial applications, extend system capability.
Save measurement results to machine variables, export to file, or output to Renishaw reporting packages. Renishaw Central, Scan Data Viewer, and MODUS CHART all support display of scanned measurement data.
Compatibility with third-party software analysis and reporting applications further extend the flexible and powerful capability of the scanning system.
Our probing software brochure is available to download below for more information.
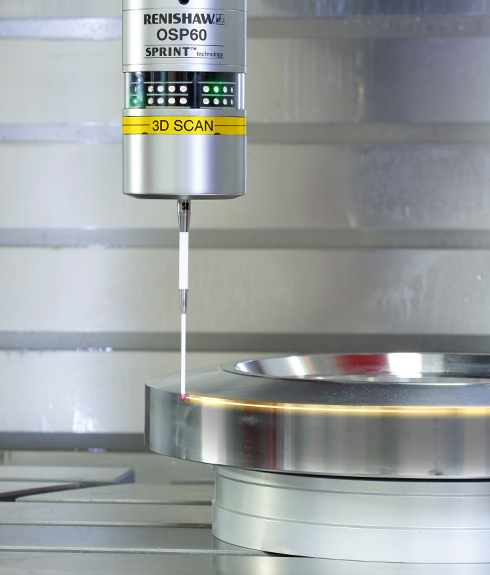
Next steps
To request more information or buy, submit a contact form to speak with your local office.
Contact us
Downloads
Brochures
Capability notes
Data sheets
Looking for support?
Contact us or visit our technical support library for installation manuals, user guides and compliance information.