Encoders hold the key to ultra-accurate motion control
Aerotech, continuing its commitment to the art and science of motion control, looks to Renishaw for versatile, high-precision laser interferometer encoders for its medical stages.
PITTSBURGH, PA – Aerotech is renowned for its high-precision positioning tables, stages and systems. Started in 1970, the company maintains its passion for developing precision motion control solutions for worldwide customers in industry, government, science, and research. Aerotech customers are the “better, stronger, faster,” crowd – always pushing the boundaries of precision – and the company delivers through development of motion control products which factor in variables that cause measurement uncertainty, down to the encoder. A long-time relationship with Renishaw led the company to a compact, yet highly accurate, encoder that enables high-precision measurement simply by being smaller. It discovered that the RLE laser interferometer encoder allowed designers to close the distance to the point of measurement, greatly minimising a key contributor to measurement uncertainty on precision machines.
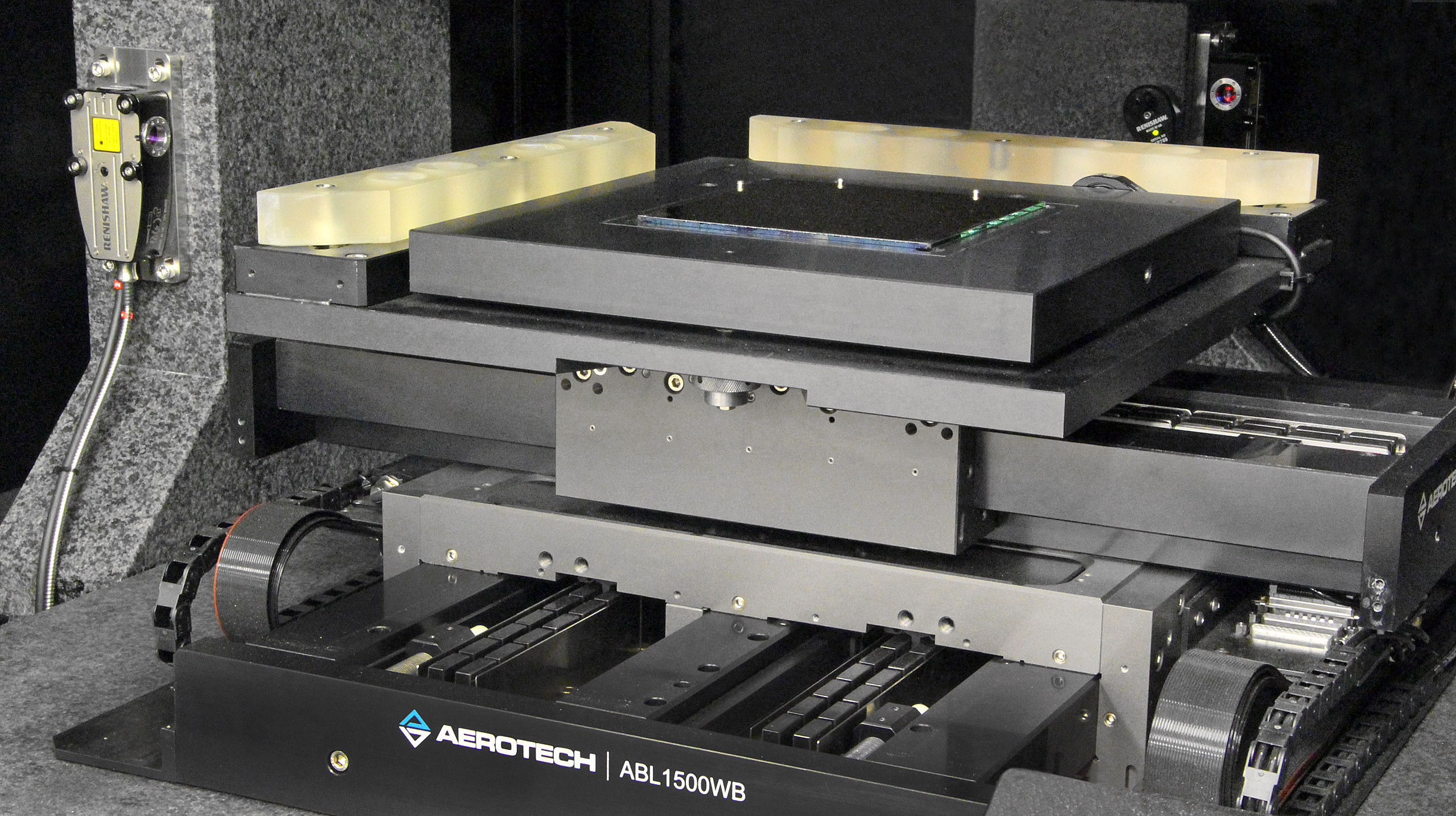
Image courtesy of Aerotech
Background
Today Aerotech stands as the only privately held, globally active, engineering-driven mechatronics company. The company's stages are used in a variety of high-performance applications including: industrial robots, fibre optics and photonics, vision systems, machine tools, assembly, semiconductor equipment, medical component laser machining, micromachining and electronic manufacturing. The company motto is Dedicated to the Science of Motion, and its customers test it regularly. “Our clients require high precision and give us some pretty demanding process specifications,” said William Land, Business Development Manager at Aerotech. “We certainly have industry-specific requirements, but quite often we get customer-specific requirements as well. When supplying today's markets, meeting those individual demands is crucial.”
Each project as unique as the last
A large portion of Aerotech's business is custom designed motion systems requiring high precision and high throughput. In one example, the company's stages are used to measure parts that are ultimately used as part masters for a high-value production process, so the measurements must minimise uncertainty.
There are several issues that can stand in the way of precision measurement, including environmental changes, thermal expansion, quality of optics, and noise in the feedback loop. However, one major concern and big influence on measurement uncertainty – Abbe offset – can be ‘designed around' with the right encoder. As explained by Land, the Abbe offset is determined by the distance between the measuring feedback device (in this case, the encoder) and the point of measurement.
Uncertainty in the measurement increases the further removed the sensor is from the point of interest. Some stage manufacturers bury the encoders down in the stage due to size and design constraints.
This increases the distance from the point of measurement on the stage to the point of interest in the process. The buried encoders do not detect any tip, tilt, roll, pitch or yaw of the other devices on the stage, causing measurement uncertainty. A more compact encoder can be placed closer to the point of measurement, but measurement accuracy is also a concern.
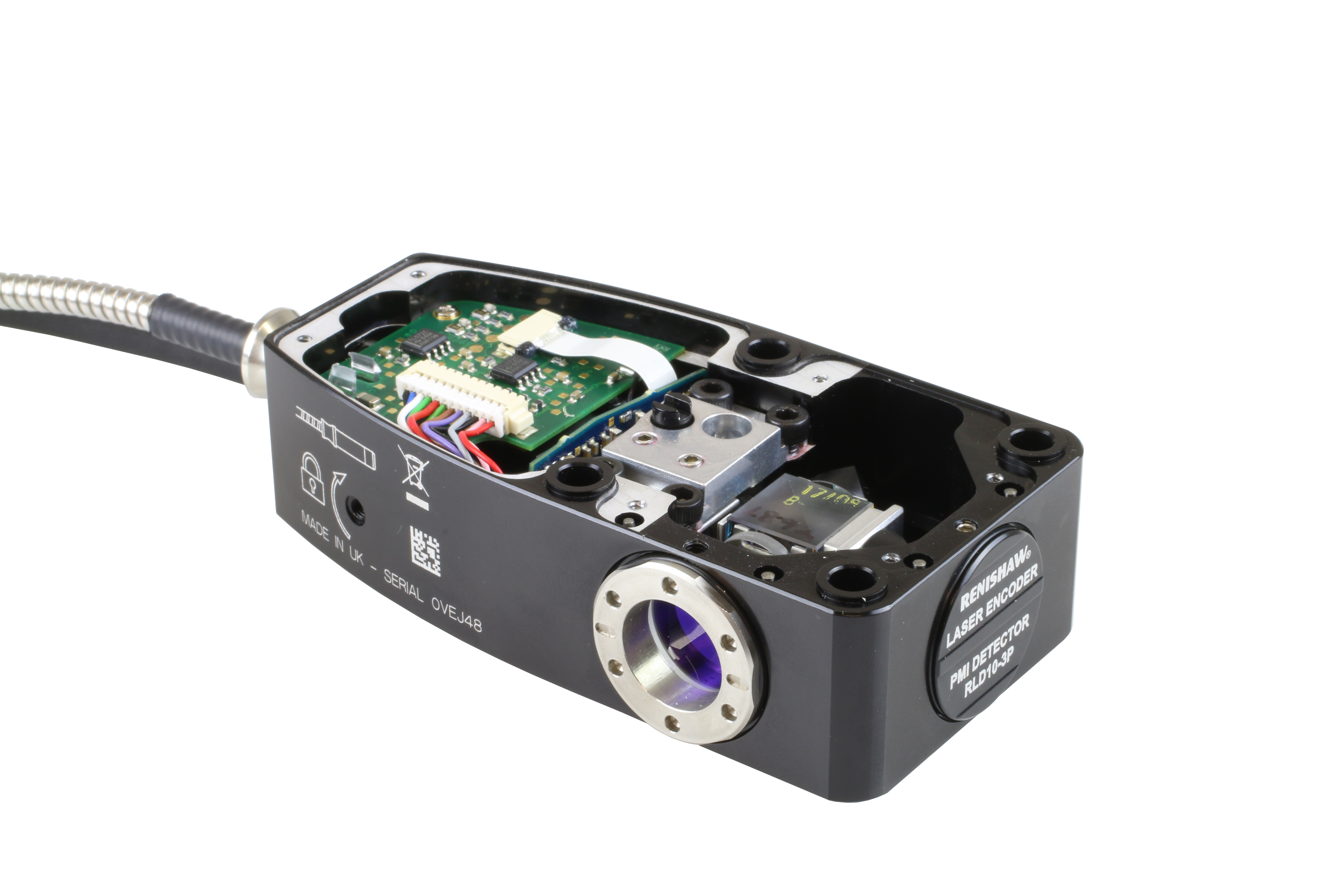
“To avoid this altogether, we use the RLE20 laser interferometer encoders. They consistently perform well, and with them, the offset is minimised allowing the measurement point to get as close to the tool point or point of interest as possible,” said Land. “The Renishaw encoders' measurement axes nominally intersect with the camera axis at the point of measurement. There is practically zero offset between where the lasers are measuring and where the measurement on the part is being taken. The RLE compact laser heads give us good design flexibility while maintaining good stability.”
We consistently exceed the specifications of customers with Renishaw's encoders. We try to offer a best-in-class experience to our customers and attribute part of our continuing success to the technology advancements that companies like Renishaw offer.
Aerotech (USA)
Small, simple, accurate
With simple system architecture and accuracy, Renishaw encoders have a lot of implementation benefits, like direct integration into assemblies. The RLE20-DX-DG laser interferometer encoders, used by Aerotech, have a high digital resolution and are a double pass homodyne with a maximum resolution setting of 10 nm. With laser interferometer technology, the wavelength is the basic unit that represents the measuring device. The wavelength stability, therefore, is directly correlated to the measurement repeatability. The laser tubes used by Renishaw are referenced against those certified by the National Physical Laboratory (NPL) to ensure they meet wavelength stability standards.
Land said that Aerotech technicians even take these encoders with them into the field. “With the ease of setup and use, we take these devices out to recalibrate machines. Because of the size of the readhead and the size of the overall system our guys put them in a case and take them to the factory to calibrate in-house,” said Land.
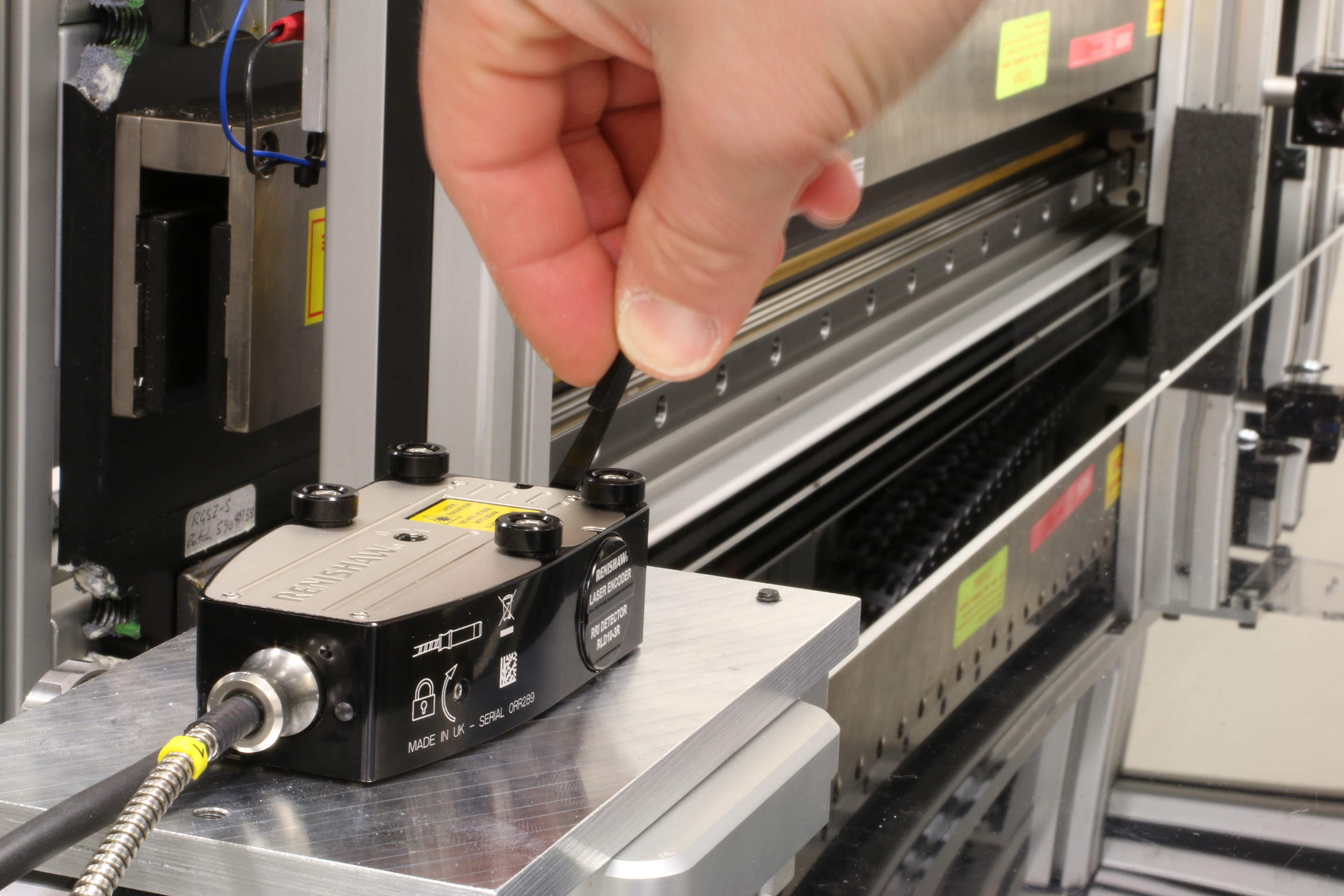
Good ingredients enable better products
Customers in many markets require accurate motion control to position and test sensors in equipment such as interferometers, autocollimators, vision systems, and antennas. These are high-precision applications that are continually pushing the limits of precision measurement, and they depend on Aerotech to provide it.
In turn, Aerotech actively seeks partners that can provide process knowledge to customers, complement its capabilities, and deliver high-performance automation control solutions for these demanding applications. “We consistently exceed the specifications of customers with Renishaw's encoders,” said Land. “Our philosophy of building superior motion control systems starts with designing, manufacturing, and purchasing superior components for use in our technology. We try to offer a best-in-class experience to our customers and attribute part of our continuing success to the technology advancements that companies like Renishaw offer.”