ATOM DX™ optical incremental encoder series
Performance in miniature
ATOM DX builds on the market proven optical system of the ATOM™ encoder platform and integrates Renishaw's high-performance interpolation technology, reducing system size and removing the need for additional adaptors and interfaces.
Constructed with Renishaw's integrated set-up LED, for an intuitive and simple installation process based on the well established auto-calibration routine, ATOM DX is ready to install straight from the box. ATOM DX is compatible with both the ADTpro-100 standalone encoder diagnostic tool and the ADTi-100 diagnostic tool, both of which are compatible with the ADT View software. They provide in-depth advanced diagnostic information to aid optimisation of encoder installation and in-field fault finding to satisfy the most demanding motion control applications.
ATOM DX readheads can be used with a wide range of linear, partial arc and rotary scales to meet most application requirements, and comes in two formats: cabled and top exit variants with either 20 µm or 40 µm scale options.
Datasheets and technical documents
Further information about the technical specifications of the ATOM DX encoder series, such as datasheets and installation guides, are available from our technical downloads section.
Watch our introduction to ATOM DX incremental encoders
What form of motion do you need to measure?
Linear
Scale type | Scale name | Accuracy | Scale pitch | Coefficient of thermal expansion at 20 °C | Supplied length |
Stainless steel tape | RTLF | 20 µm: ±5 µm/m 40 µm (high accuracy): ±5 µm/m | 20 µm/40 µm | ~10.1 ±0.2 µm/m/°C | Up to 10 m (> 10 m on request) |
Glass spar | RCLC | ±3 µm/m | 20 µm/40 µm | ~8 µm/m/°C | Up to 130 mm |
Narrow stainless steel tape | RKLF-S | 20 µm: ±5 µm/m 40 µm (high accuracy): ±5 µm/m 40 µm: ±15 µm/m | 20 µm/40 µm | Matched to substrate material when scale ends are fixed with end clamps | Up to 10 m (> 10 m on request) |
Partial arc
Scale type | Scale name | Accuracy | Scale pitch | Coefficient of thermal expansion at 20 °C | Scale max length |
Narrow stainless steel partial arc tape | RKLF-S | ±15 µm/m | 40 µm | 10.1 ±0.2 μm/m/°C | Up to 10 m (> 10 m on request) |
Rotary
Scale type | Scale name | Graduation accuracy | Scale pitch | Coefficient of thermal expansion at 20 °C | Disc outer diameter |
Glass disc | RCDM | ±0.5 µm (disc ø up to 100 mm) ±0.7 µm (disc ø over 100 mm) | 20 µm/40 µm | ~8 µm/m/°C | 17 mm to 108 mm |
Key benefits
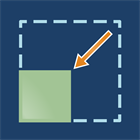
Miniature head
Fits into the smallest applications with heights as low as 7.85 mm. Cabled and top exit variants available.
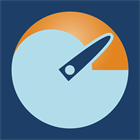
High speed
Maximum speeds up to 20 m/s and a range of high-speed interpolation options.
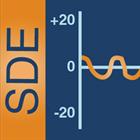
Velocity control
Renishaw's latest interpolation technology, with updated signal processing algorithms to reduce Sub-Divisional Error (SDE).
Renishaw's encoder range allows for very easy and flexible system integration. We almost always use the Renishaw ATOM encoder and, more recently, the ATOM DX encoder for our more compact micromachining systems.
Lasing Microsystem S.A. (Spain)
Optional Advanced Diagnostic Tools
Renishaw optical encoders can generally be installed using just the set-up LED on the readhead but an Advanced Diagnostic Tool (ADT) can be used to help with more challenging installations. These tools provide detailed real-time encoder data to assist in fault finding and to avoid lengthy machine downtime.
The ATOM DX encoder is compatible with two Advanced Diagnostic Tools: the ADTpro-100 and the ADTi-100.
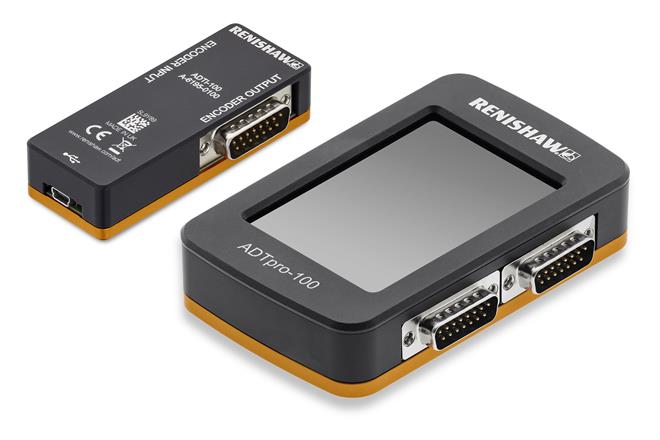
The ADTpro-100:
- Is a handheld, standalone encoder diagnostic tool – no computer or other equipment is required.
- Features an integral colour touch screen.
- Is easy and intuitive to use with plug-and-play functionality to aid system set-up and calibration.
- Interfaces with the optional ADT View computer software, which allows encoder data to be saved as a record of the system setup and performance. ADT View can also be used to update the ADTpro-100 firmware
The ADTi-100:
- Interfaces with the intuitive ADT View computer software.
- Provides comprehensive real-time encoder data feedback to aid more challenging installations and diagnostics.
- Assists system set-up, calibration and signal optimisation along the entire axis.
- Allows encoder data, such as signal strength vs position along the axis, to be saved as a record of the system setup and performance.
Both the ADTpro-100 and ADTi-100 can be used standalone or in-line, connected between the readhead and the controller as part of the control loop.
Discover our range of open optical encoders designed to meet your industrial automation needs.