Our strategy
We are a manufacturing technology powerhouse, and our strategy aims to fulfil our purpose of Transforming Tomorrow Together by creating long-term value for all our stakeholders.
Our strategy for long-term value creation
We pursue leading positions in an expanding range of high-growth markets for our portfolio of sensor- and software-enabled systems products. We target high single-digit average through-cycle organic growth and more than 20% Adjusted operating profit margin while delivering on our ESG strategy, including our commitment to Net Zero.
Our opportunity
Well positioned in markets growing at more than 5% per annum.
Our strategy
Driving consistent outperformance.
Our strategy is underpinned by a robust risk management framework.
We measure our progress against 10 KPIs that reflect financial and non-financial performance.
Our opportunity
We pursue innovation-led growth in both emerging and established markets with a combined addressable value of 6bn, and where manufacturing and societal trends contribute to attractive through-cycle growth rates of at least 5%. We are well positioned to grow market share in fast-moving emerging markets, while building on our first- or second-place positions in many established markets, where we average a more than 20% share.
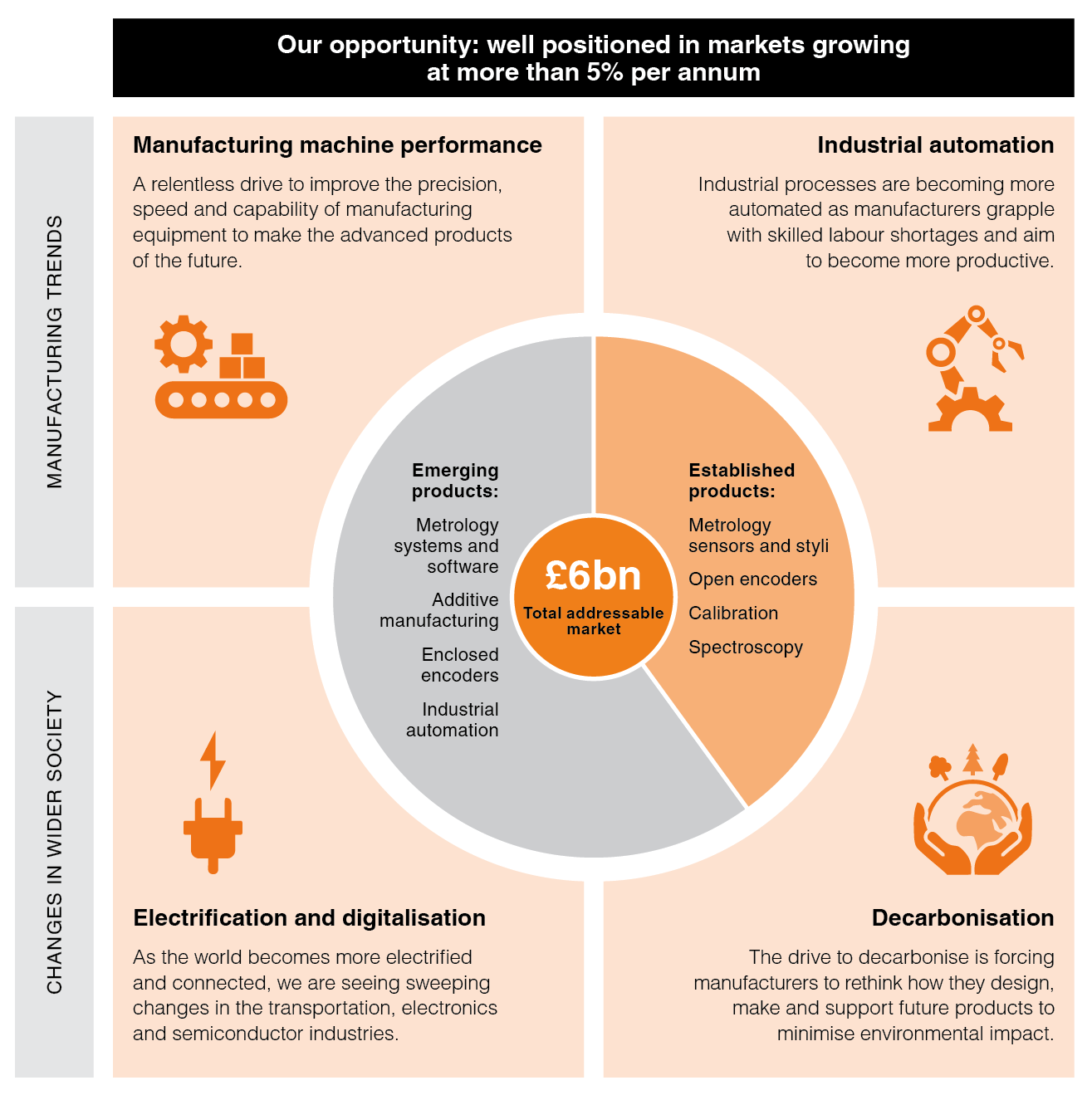
Our three strategic focus areas
To make the most of the opportunities presented by our attractive growth markets, we've identified six strategic priorities, grouped in three core areas, to help drive market growth and help us grow market share ahead of our competition. Our focus on these areas is set within a rigorous risk management framework, which includes our approach to climate risk, and is underpinned by our ESG strategy.
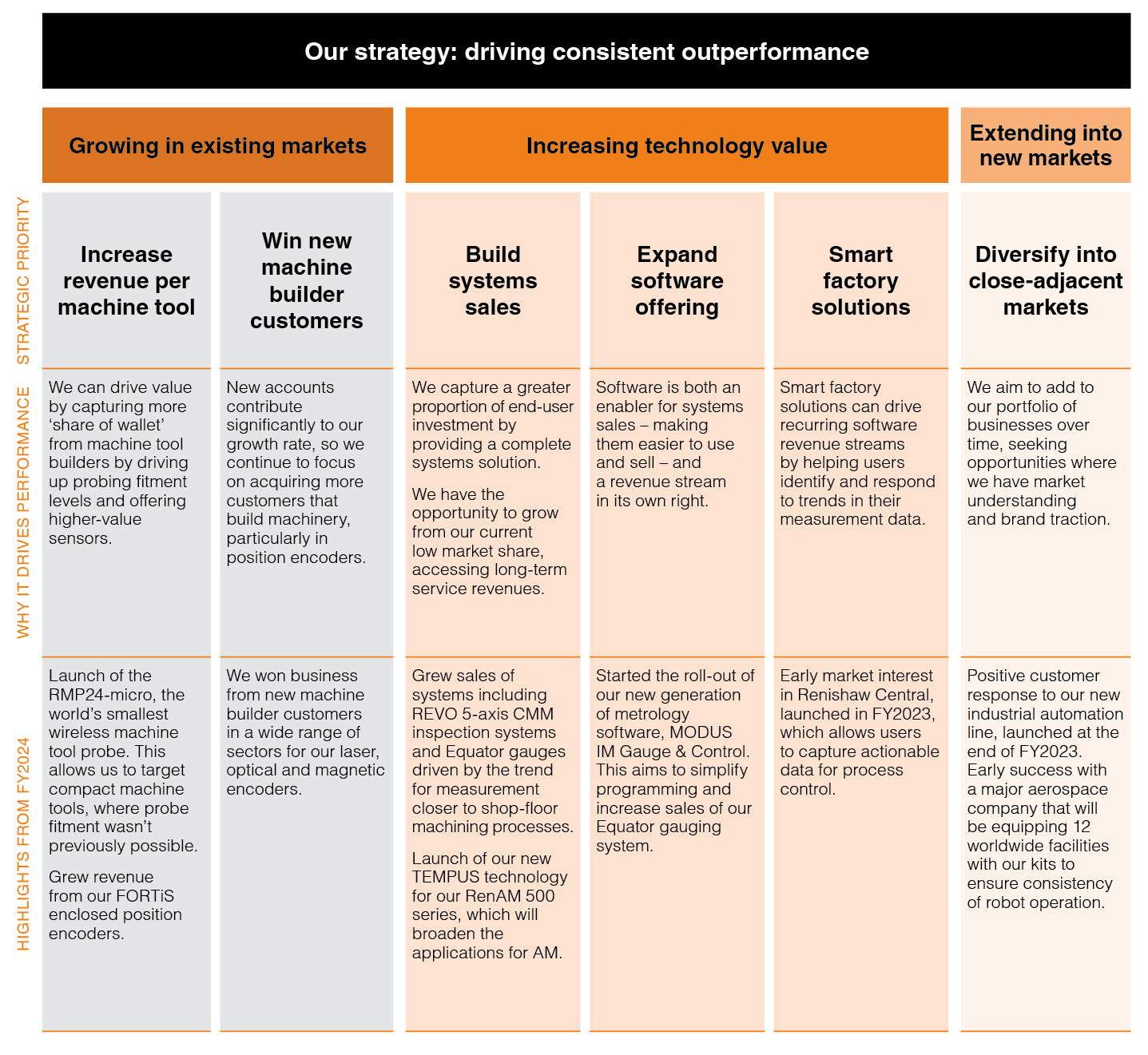