VIONiC™ optical incremental encoder series
The VIONiC encoder series is Renishaw's highest performing incremental optical open encoder. It provides direct digital position feedback with superior metrology, high operating speeds and excellent reliability.
Enhance your motion control
The VIONiC readhead integrates Renishaw's market proven filtering optics and advanced interpolation technology. This provides ultra‑low Sub-Divisional Error (SDE), excellent dirt immunity, and eliminates the need for additional adaptors or separate interfaces.
VIONiC readheads are compatible with a wide range of linear, partial arc and rotary scales, from low expansion ZeroMet™ scales, to highly accurate REXM rings. So, for versatility and uncompromising metrology, choose the VIONiC encoder series. Designed with intuitive auto calibration mode, VIONiC encoders are easy to install.
The VIONiC encoder is compatible with both the ADTpro-100 standalone encoder diagnostic tool and the ADTi-100 diagnostic tool, both of which are compatible with the ADT View software. They provide in-depth advanced diagnostic information to aid optimisation of encoder installation and in-field fault finding to satisfy the most demanding motion control applications.
Datasheets and technical documents
Further information about the technical specifications of the VIONiC encoder series, such as datasheets and installation guides, are available from our technical downloads section.
Watch our introduction to VIONiC incremental encoders
What form of motion do you need to measure?
Linear
Scale type | Scale name | Accuracy | Scale pitch | Coefficient of thermal expansion at 20 °C | Supplied length |
Stainless steel tape | RTLC20 | ±5 µm/m | 20 µm | 10.1 ±0.2 µm/m/°C | Up to 10 m (> 10 m on request) |
Stainless steel tape with track option | RTLC20 with optional FASTRACK™ | ±5 µm/m | 20 µm | 10.1 ±0.2 µm/m/°C | Up to 10 m (> 10 m on request) |
ZeroMet™ spar | RELM20/RELE20 | ±1 µm for up to 1 m, then ±1 µm/m | 20 µm | 0.75 ±0.35 µm/m/°C | Up to 1.5 m |
Stainless steel spar | RSLM20/RSLE20/RSLC20 | ±1.5 µm up to 1 m, ±2.25 µm up to 2 m, ±3 µm up to 3 m, ±4 µm up to 5 m | 20 µm | 10.1 ±0.2 µm/m/°C | Up to 5 m |
Narrow stainless steel tape | RKLC20-S | ±5 µm/m | 20 µm | Matched to substrate material when scale ends are fixed with end clamps | Up to 20 m (> 20 m on request) |
Partial arc
Scale type | Scale name | Accuracy | Scale pitch | Coefficient of thermal expansion at 20 °C | Supplied length |
Narrow stainless steel partial arc tape | RKLC20-S | ±5 µm/m | 20 µm | 10.1 ±0.2 μm/m/°C | Up to 20 m (> 20 m on request) |
Rotary
Scale type | Scale name | Accuracy (depending on ring diameter) | Scale pitch | Coefficient of thermal expansion at 20 °C | Ring diameter |
Stainless steel ring | RESM20/REST20 | Graduation accuracy: ±3.97 to ±0.38 arc seconds | 20 µm | 15.5 ±0.5 µm/m/°C | 52 to 550 mm |
Ultra-high accuracy stainless steel ring | REXM20/REXT20 | Installed accuracy: (≥ 100 mm diameter) ±1 arc second | 20 µm | 15.5 ±0.5 µm/m/°C | 52 to 417 mm |
Key benefits
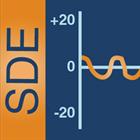
Ultra-low Sub-Divisional Error
Advanced interpolation technology for ultra-low Sub-Divisional Error (SDE) of typically <±15 nm; the lowest of all Renishaw optical encoders.
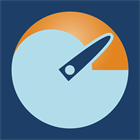
High speed
Resolution as fine as 2.5 nm, maximum clock rate of 50 MHz and speeds up to 12 m/s. Speeds of up to 3.63 m/s at a resolution of 0.1 µm.
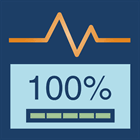
Advanced Diagnostic Tools
Optional in-depth advanced diagnostic information to aid optimisation of encoder installation and in-field fault finding.
Optional Advanced Diagnostic Tools
Renishaw optical encoders can generally be installed using just the set-up LED on the readhead but an Advanced Diagnostic Tool (ADT) can be used to help with more challenging installations. These tools provide detailed real-time encoder data to assist in fault finding and to avoid lengthy machine downtime.
The VIONiC encoder is compatible with two Advanced Diagnostic Tools: the ADTpro-100 and the ADTi-100.
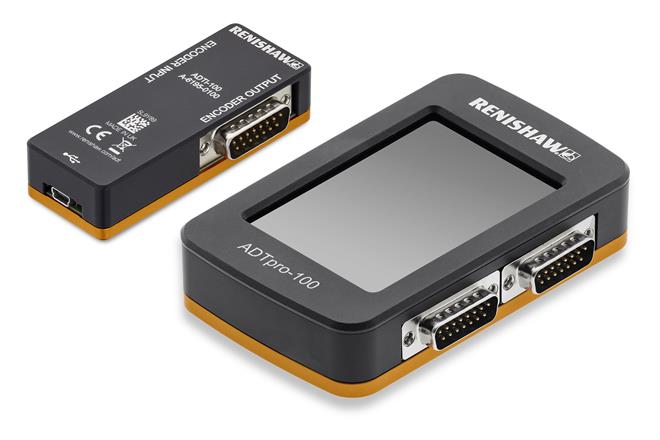
The ADTpro-100:
- Is a handheld, standalone encoder diagnostic tool – no computer or other equipment is required.
- Features an integral colour touch screen.
- Is easy and intuitive to use with plug-and-play functionality to aid system set-up and calibration.
- Interfaces with the optional ADT View computer software, which allows encoder data to be saved as a record of the system setup and performance. ADT View can also be used to update the ADTpro-100 firmware
The ADTi-100:
- Interfaces with the intuitive ADT View computer software.
- Provides comprehensive real-time encoder data feedback to aid more challenging installations and diagnostics.
- Assists system set-up, calibration and signal optimisation along the entire axis.
- Allows encoder data, such as signal strength vs position along the axis, to be saved as a record of the system setup and performance.
Both the ADTpro-100 and ADTi-100 can be used standalone or in-line, connected between the readhead and the controller as part of the control loop.
Discover our range of open optical encoders designed to meet your industrial automation needs.