Renishaw encoders go under the 3DHISTECH microscope
Renishaw's Zsombor Zelena collaborates with 3DHISTECH Ltd, a pathology equipment and services specialist, to provide them with the latest in encoder technology. Watch the video summary below and read the full article for further information and links.
Background
Invented during the 16th century, the first microscope was based on an optical system to magnify samples for analysis. These systems used natural sunlight or a spotlight to illuminate a sample while an operator made freehand sketches. Since then, a number of variants have been developed such as the fluorescence microscope, the electron microscope and the scanning microscope.
In 1900, the first optical micrograph was produced by taking a photograph of a sample through the lens of a microscope. Since then, these photomicrography systems have advanced to the point where multiple photomicrographs are taken and then combined to form ultra-high resolution images. These ultra-high resolution, multi-photomicrograph images are made possible through ever advancing optics, automation and highly accurate position feedback.
Located in Budapest, Hungary, 3DHISTECH designs and manufactures one of the world's fastest and highest-capacity autonomous panoramic digital slide scanners – the P1000.
The P1000 is a highly accurate scanning microscope that enables large pathology labs to capture ultra-high resolution images of medical samples, while operating unmanned for up to 2 days. Building upon 3DHISTECH's successful product range, this new generation of digital slide scanner is the first to have integrated optical and magnetic position feedback encoders for enhanced throughput.
Viktor Varga, Chief Technology Officer of 3DHISTECH, elaborates:
“The P1000 can digitize 1000 slides in one work shift. It has two main components: a digital slide scanner [microscope] and a high capacity slide loader. These components work in parallel to increase the throughput of the system. The microscope has three objectives enabling both immersion and dry scanning. We designed the system to cover any need of a typical pathology or biological laboratory.”
The VIONiC™ digital incremental optical encoder system with RTLC-S stainless steel tape scale has been installed on the three axes of the microscope, and the absolute LA11 magnetic encoder system was selected for the pick-and-place robot of the slide loader. These encoders enable the P1000 to operate at higher speeds than competing products in an accurate and repeatable way.
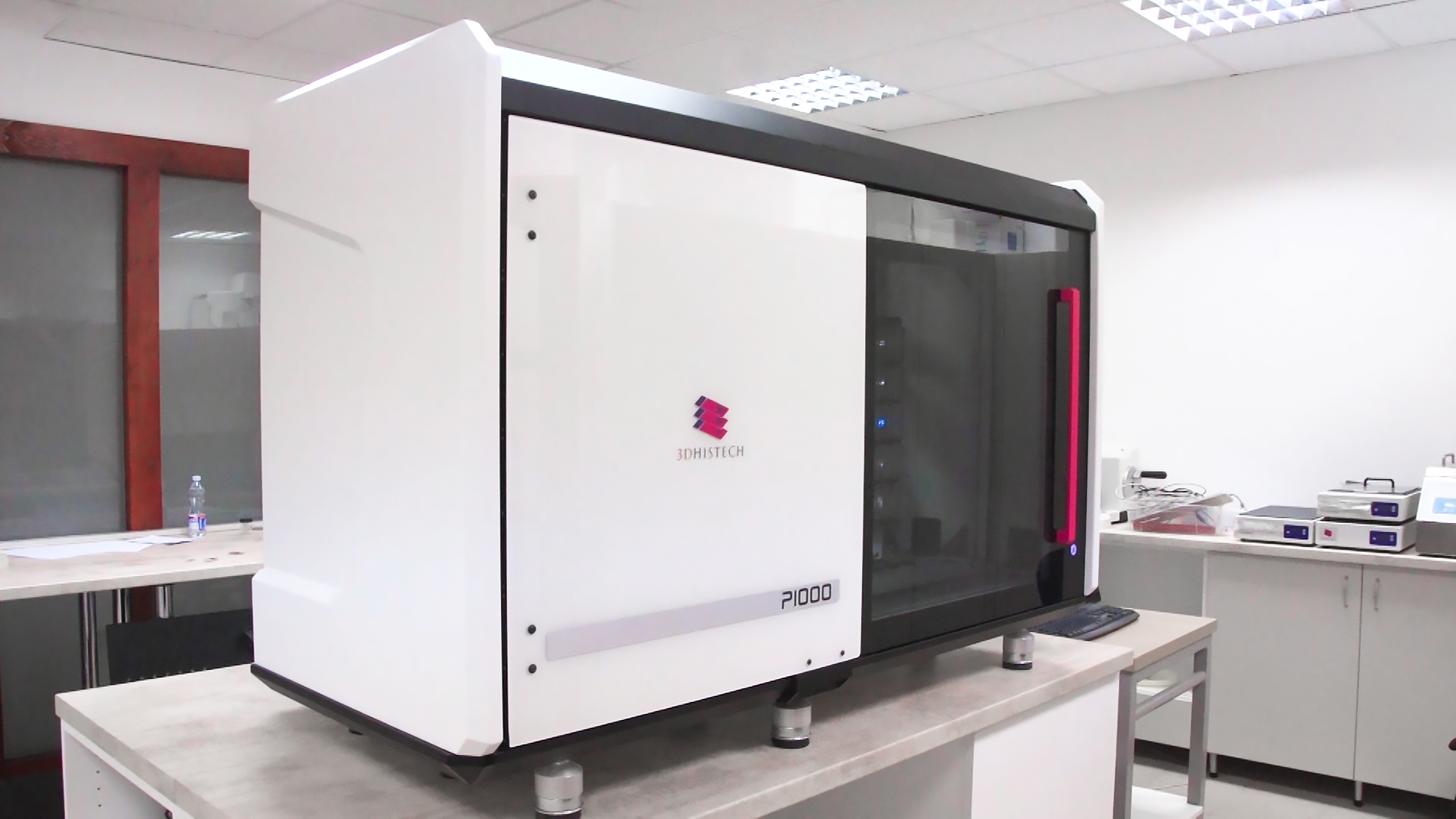
P1000 digital slide scanner in pathology lab
Challenges
The team behind the P1000 had one clear goal in mind: significantly increase the throughput of large pathology labs. They concluded that the system should be of a high capacity and autonomous to achieve this goal.
During a scanning procedure, a stage with the sample is moved in the horizontal plane, along the X and Y axes, while the lens is adjusted vertically to maintain image focus. The higher the magnification, the greater the accuracy required to ensure accurate stitching of multiple photomicrographs to create a high resolution image.
The majority of digital microscopes have a single vertical axis (Z-axis) encoder. In cases where the sample stage operates without encoders, there is no direct feedback to the controller. The engineers who developed the P1000 used encoder feedback from the positioning process to enable operation at much higher speeds without compromising accuracy: higher automation reduces the level of operator interference required between micrographs, which translates to less time taken per slide and higher process throughput.
The depth of field (the focal range over which the image is well focused) of the lenses used in these microscopes spans hundreds of nanometres (nm) and, therefore, excellent motion control is required. The optimal distance between the lens and the sample is calculated by image processing software and is based on the fuzziness of the captured images. The P1000 creates a ‘map' before each scanning run by measuring the Z-height of points all over the sample in order to determine the correct focal distance and then extrapolates the captured data over the whole sample. This makes the scanning process faster, simpler, more stable and more accurate.
3DHISTECH specified a high resolution encoder, ultra-precise mechanics, and a fine-tuned process control system with a short control response time. These requirements are challenging in terms of mechanical and electrical engineering. Engineers had to minimise the stick-slip effect, and create a control loop with precise feedback for driving a piezomotor with a 100 nm step-size. The readhead's resolution and noise level (non-repeatable errors) were the most important performance parameters that influenced selection of the encoder system.
For the pick-and-place robot of the slide-loader, a high accuracy encoder was unnecessary as wide setup tolerances and easy installation were more important, as was reliability. When designing the microscope, the engineers chose the same encoder specification for each axis to simplify installation and servicing. They also selected cut-to-length scales, which allows the stocking of compact tape scale reels.

Pathological tissue sample on slide
The encoder systems are surprisingly easy to install and set up in light of their performance.
3DHISTECH (Hungary)
Solution
The pixel size on each captured image is 0.25 to 0.08 μm. The machine uses a pre-defined overlap of approx. 10 μm and precise encoder feedback is required to accurately stitch together thousands of images.
Since the step-size of the chosen piezo-motor is 100 nm, the required resolution of the encoder is 50 nm to allow sufficient servo-bandwidth. The depth of field of the lens with the highest magnification factor is 0.2 μm, which gives every design parameter a sizable safety margin. The sample holder slides on a granite block to minimise frictional forces and vibration transfer from the outside.
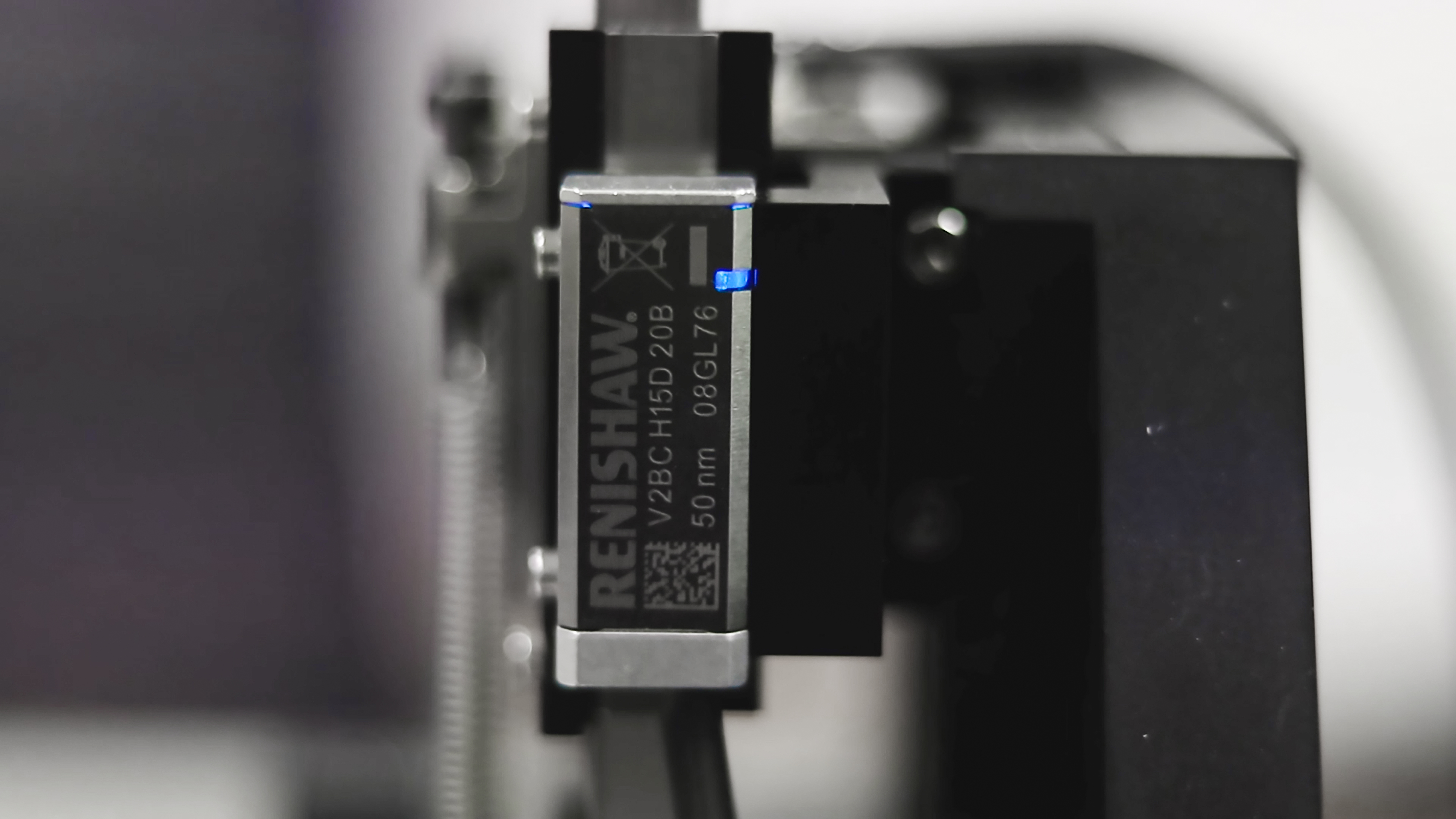
VIONiC encoder in-situ
The engineers of 3DHISTECH decided to use VIONiC incremental encoders on the slide scanner to eliminate the latency associated with the conversion of absolute position into serial communication signals. They connected the encoder output directly to the microcontroller responsible for moving the axes to enable ‘real-time' feedback. The chosen encoder is required to provide high resolution position feedback with low cyclic error (SDE), noise and jitter.
The VIONiC series is Renishaw's ultra-high accuracy, all-in-one digital incremental encoder for both linear and rotary applications. VIONiC combines all necessary interpolation and digital signal processing inside the readhead, with cyclic error as low as <±10 nm and resolutions down to 2.5 nm. It has many customizable parameters, from resolution and edge separation to connector-type and cable lengths. Unrivalled ease of set-up and calibration is supported by an Advanced Diagnostic Tool (ADT), which includes user software that allows remote control and monitoring of VIONiC's set-up and calibration routines.
This set-up tool is ideal for factory production-line installation as it allows remote, advanced calibration features. The ADT is used by 3DHISTECH during readhead installation due to unavoidable obstruction of the line-of-sight to the set-up LED. The ADT makes production-line installation much easier; previously when checking the readhead's signal or optimum rideheight, the encoder system had to be hard-wired into the controller of the machine and further fine tuning took many iterations. With the ADT, the readhead can be connected to a laptop via a USB connector, even with no power in the machine.
In terms of mechanical design, the aim was to minimise mechanical vibrations, which is why the engineers decided to use 5-phase stepper motors instead of 2-phase. The 5-phase motors produce less vibration due to a lower torque ripple and this is critical to ensure optimum scanning performance. The Z-axis of the microscope is directly driven by a linear piezomotor to provide the required smaller step-size, high speed and rapid direction changing. Friction was minimised by the use on each axis of crossed-roller bearings with an anti-creep cage.
The pick-and-place robot comprises three belt-driven axes with encoder feedback. In this case, the LA11 magnetic encoder by Renishaw's associate company RLS is the ideal solution as it is a true-absolute encoder system with a large rideheight tolerance. The controller uses SPI protocol (Serial Peripheral Interface - an absolute signal protocol), so the LA11 encoder with RS422 (a digital 5 V-potential incremental signal protocol with twisted pairs) parallel output is the optimal solution for the robot to achieve the specified accuracy of ±0.1 mm. Furthermore, the true-absolute measuring principle protects the samples in the event of unexpected shutdowns: after a power outage the encoder reports its position immediately upon power restoration without the need for time-consuming homing cycles.
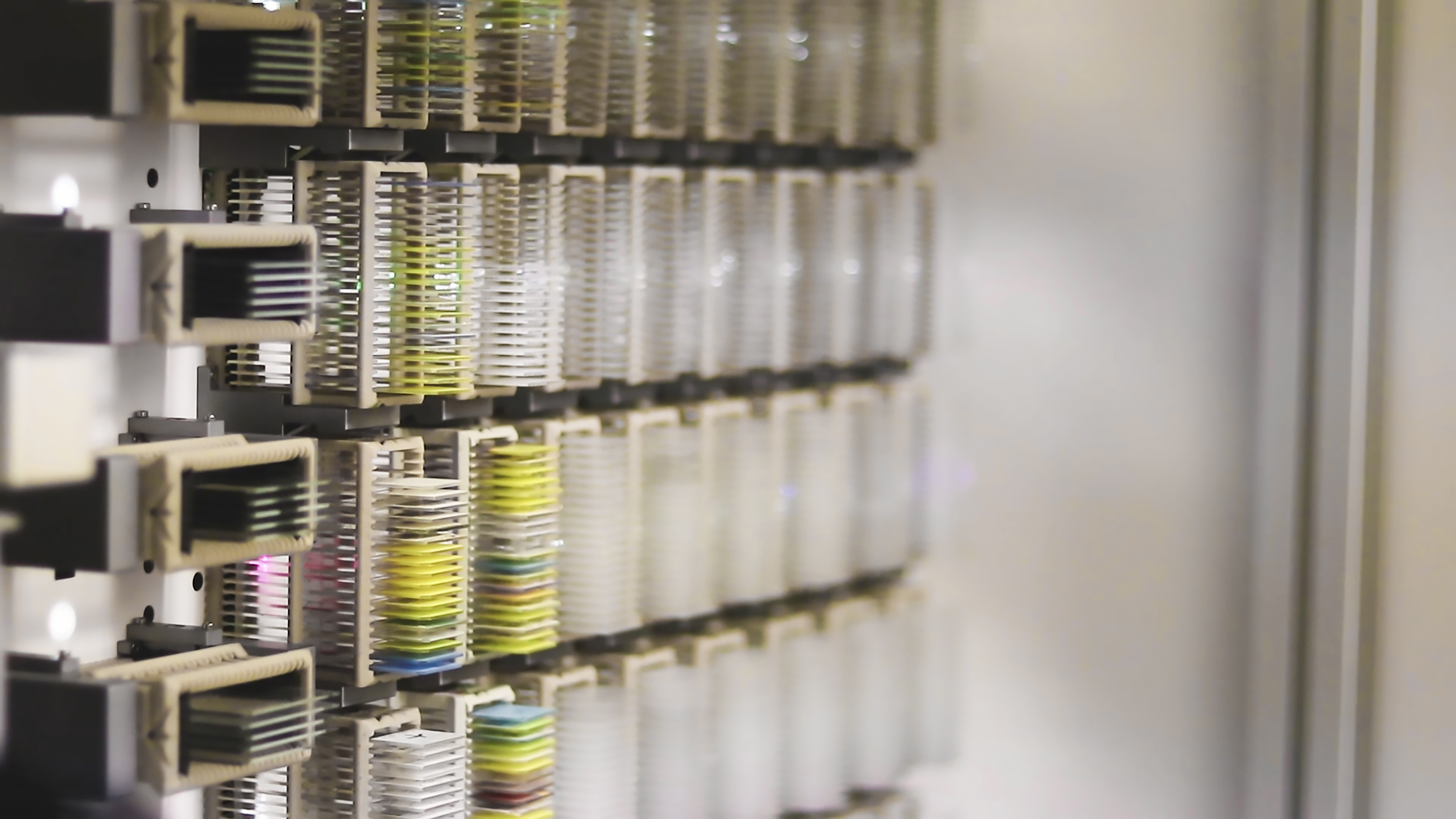
P1000 has capacity for 1000 slides and can digitise all of them in one work-shift
Results
With Renishaw's technical support, 3DHISTECH's engineering team were able to specify an encoder for each machine axis and find the appropriate encoder products for their applications. Advanced encoders, such as Renishaw's VIONiC series and RLS' LA11 magnetic encoder, enable the P1000 to achieve truly market-leading performance.
About 3DHISTECH
3DHISTECH was founded in 1996 and manufactures high-speed slide scanners and digital microscopes. Its aim is to fully digitalise the traditional pathology workflow to meet the ever growing demands of 21st century healthcare. 3DHISTECH's facility is located in Budapest, but it has machines all over the world from Europe and US to East Asia, including Korea and Japan.
About RLS
RLS d.o.o is a Renishaw associate company. RLS produce a range of robust magnetic rotary and linear motion sensors for applications such as industrial automation, metalworking, textiles, packaging, electronic chip / board production, robotics and more.
For more information about the RLS magnetic encoder range, visit www.rls.si