RESOLUTE™ optical absolute encoder series
High-performance absolute position measurement
The RESOLUTE optical absolute encoder measures absolute position with fine resolutions down to 1 nm and high speeds up to 100 m/s. Advanced optics and innovative position determination algorithms deliver exceptional metrology performance. Low Sub-Divisional Error (SDE) and ultra-low noise (jitter) makes it suitable for demanding motion control challenges.
Application-specific variants include RESOLUTE Ultra-High Vacuum (UHV), RESOLUTE Extended Temperature Range (ETR) and RESOLUTE Functional Safety (FS).
Optional Advanced Diagnostic Tools and ADT View software acquire comprehensive real-time encoder data allowing optimisation and in-field fault finding.
Datasheets and technical documents
Further information about the technical specifications of the RESOLUTE encoder series, such as datasheets and installation guides, are available from our technical downloads section.
Serial interfaces
RESOLUTE encoders are available with linear, rotary and partial arc scales with a variety of serial interfaces:
- BiSS® C (unidirectional) with compatible controllers
- BiSS Safety (unidirectional)
- FANUC (α and αi)
- Mitsubishi (J4 and J5 series of servo drives, and the MDS-D2/DH2/DM2/DJ drives for machine tool applications)
- Panasonic (A5 and A6 series of drivers)
- Siemens DRIVE-CLiQ®
- Yaskawa (Sigma-5 and Sigma-7 SERVOPACKs)
Watch our introduction to RESOLUTE absolute encoders
Key benefits
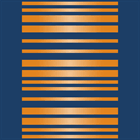
True-absolute
Position is acquired immediately on start-up without requiring any motion.
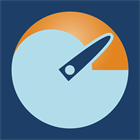
High speed
Measurement of absolute position with high speeds up to 100 m/s (36 000 rpm) and fine resolutions down to 1 nm.
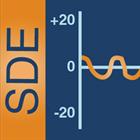
Metrology performance
Low Sub-Divisional Error (SDE) of ±40 nm and ultra-low noise (jitter) of less than 10 nm RMS.
What form of motion do you need to measure?
Linear (including UHV, FS)
Scale type | Scale name | Accuracy | Scale pitch | Coefficient of thermal expansion at 20 °C | Supplied length | Other variants |
Stainless steel tape | RTLA30 | ±5 µm/m | 30 µm | 10.1 ±0.2 µm/m/°C | Up to 21 m | Ultra-High Vacuum, Functional Safety |
Stainless steel tape with track option | RTLA30 with optional FASTRACK™ | ±5 µm/m | 30 µm | 10.1 ±0.2 µm/m/°C | Up to 21 m | Ultra-High Vacuum, Functional Safety |
ZeroMet™ spar | RELA30 | ±1 µm for up to 1 m, then ±1 µm/m | 30 µm | 0.75 ±0.35 µm/m/°C | Up to 1.5 m | Ultra-High Vacuum, Functional Safety |
Stainless steel spar | RSLA30 | ±1.5 µm up to 1 m, ±2.25 µm up to 2 m, ±3 µm up to 3 m, ±4 µm up to 5 m | 30 µm | 10.1 ±0.2 µm/m/°C | Up to 5 m | Ultra-High Vacuum, Functional Safety |
Narrow stainless steel tape | RKLA30-S | ±5 µm/m | 30 µm | Matched to substrate material when scale ends are fixed with end clamps | Up to 21 m |
Partial arc
Scale type | Scale name | Accuracy | Scale pitch | Coefficient of thermal expansion at 20 °C | Supplied length |
Narrow stainless steel partial arc tape | RKLA30-S | ±5 μm/m | 30 µm | 10.1 ±0.2 μm/m/°C | Up to 21 m |
Rotary (including UHV, FS, ETR)
Scale type | Scale name | Accuracy (depending on ring diameter) | Scale pitch | Coefficient of thermal expansion at 20 °C | Ring diameter | Other variants |
Stainless steel ring | RESA30 | Graduation accuracy: 4 to 0.4 arc seconds | 30 µm | 15.5 ±0.5 µm/m/°C | 52 to 550 mm | Ultra-High Vacuum, Functional Safety, Extended Temperature Range |
Ultra-high accuracy stainless steel ring | REXA30 | Installed accuracy: (≥100 mm diameter) ±1 arc second ±1.5 arc seconds ±2 arc seconds | 30 µm | 15.5 ±0.5 µm/m/°C | 52 to 417 mm | Ultra-High Vacuum, Functional Safety, Extended Temperature Range |
We exclusively use RESOLUTE encoders in our radar products, the line-of-sight and SATCOM antennas and high-power microwave products. We have chosen these encoders for their high accuracy and high resolution, which we can use in our control loops.
Pacific Antenna Systems (USA)
Optional Advanced Diagnostic Tool ADTa-100
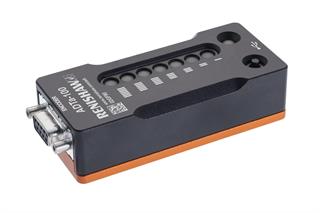
RESOLUTE encoder readheads (marked with the ADT symbol) are compatible with the Advanced Diagnostic Tool ADTa-100 and ADT View software. They provide comprehensive real-time encoder data feedback to aid more challenging installations and diagnostics. The intuitive software interface can be used for:
- Remote calibration
- Signal optimisation over the entire axis length
- Digital readout of encoder position (relative to the scale)
- Exporting and saving data
- Setting zero
Discover our range of open optical encoders designed to meet your industrial automation needs.