TONiC™ optical incremental encoder series
Exceptional, compact and versatile metrology
The TONiC series is a compact, non-contact incremental encoder system that offers speeds up to 10 m/s and, when combined with the Ti interface, resolutions down to 1 nm for linear, partial arc and rotary applications. Advanced filtering optics within the readhead give TONiC very low jitter, resulting in excellent positional stability and smoother velocity control.
The TONiC encoder also features exceptional signal stability with low Sub-Divisional Error (SDE) to help realise superior motion control performance. TONiC systems feature an integrated set-up LED for intuitive and efficient installation. They are compatible with Renishaw's ADTpro-100 diagnostic tool.
Additionally, the TONiC™ encoder series offers a variety of external interfaces that can be configured to meet the speed and resolution requirements of the application. With late-stage integration and configuration of the external interface, one versatile TONiC readhead offers many options for end user customisation.
Application-specific variants include TONiC Ultra-High Vacuum (UHV) and TONiC Functional Safety (FS).
Datasheets and technical documents
Further information about the technical specifications of the TONiC encoder series, such as datasheets and installation guides, are available from our technical downloads section.
What form of motion do you need to measure?
Linear (including UHV, FS)
Scale type | Scale name | Accuracy | Scale pitch | Coefficient of thermal expansion at 20 °C | Supplied length | Other variants |
Stainless steel tape | RTLC20 | ±5 µm/m | 20 µm | 10.1 ±0.2 µm/m/°C | Up to 10 m (> 10 m on request) | Ultra-High Vacuum, Functional Safety |
Stainless steel tape with track option | RTLC20 with optional FASTRACK | ±5 µm/m | 20 µm | 10.1 ±0.2 µm/m/°C | Up to 10 m (> 10 m on request) | Ultra-High Vacuum, Functional Safety |
ZeroMet™ spar | RELM20/RELE20 | ±1 µm for up to 1 m, then ±1 µm/m | 20 µm | 0.75 ±0.35 µm/m/°C | Up to 1.5 m | Ultra-High Vacuum, Functional Safety |
Stainless steel spar | RSLM20/RSLE20/RSLC20 | ±1.5 µm up to 1 m, ±2.25 µm up to 2 m, ±3 µm up to 3 m, ±4 µm up to 5 m | 20 µm | 10.1 ±0.2 µm/m/°C | Up to 5 m | Ultra-High Vacuum, Functional Safety |
Narrow stainless steel tape | RKLC20-S | ±5 µm/m | 20 µm | Matched to substrate material when scale ends are fixed with end clamps | Up to 20 m (> 20 m on request) | Ultra-High Vacuum |
Partial arc
Scale type | Scale name | Accuracy | Scale pitch | Coefficient of thermal expansion at 20 °C | Supplied length |
Narrow stainless steel partial arc tape | RKLC20-S | ±5 µm/m | 20 µm | 10.1 ±0.2 μm/m/°C | Up to 20 m (> 20 m on request) |
Rotary (including UHV, FS)
Scale type | Scale name | Accuracy (depending on ring diameter) | Scale pitch | Coefficient of thermal expansion at 20 °C | Ring diameter | Other variants |
Stainless steel ring | RESM20/REST20 | Graduation accuracy: ±3.97 to ±0.38 arc seconds | 20 µm | 15.5 ±0.5 µm/m/°C | 52 to 550 mm | Ultra-High Vacuum, Functional Safety |
Ultra-high accuracy stainless steel ring | REXM20/REXT20 | Installed accuracy: (≥ 100 mm diameter) ±1 arc second | 20 µm | 15.5 ±0.5 µm/m/°C | 52 to 417 mm | Ultra-High Vacuum |
Key benefits
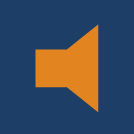
Very low jitter
Exceptionally low signal output jitter of <±0.5 nm RMS and low Sub-Divisional Error (SDE) of <±30 nm.
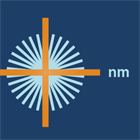
Fine resolution
Ultra-fine resolution down to 1 nm. Ideal for applications requiring precise velocity and positional control.
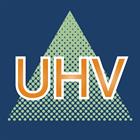
UHV and FS variants
TONiC UHV, for Ultra-High Vacuum applications, and TONiC FS, for Functional Safety certification to SiL2 and PLd.
TONiC's repeatable precision is at the measurement unit level, which massively increases the flexibility we have when we perform system optimisation including parameter compensation.
Sam-Jeong Automation (South Korea)
Optional Advanced Diagnostic Tool ADTpro-100
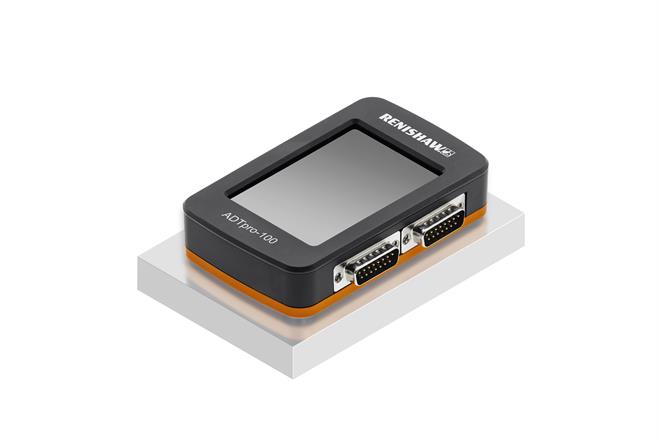
The ADTpro-100 is a handheld, standalone encoder diagnostic tool featuring an integral colour touch screen. It assists in system set-up and planned maintenance to help minimise unscheduled machine downtime. The ADTpro-100:
- Requires no computer or additional set-up equipment to display comprehensive real-time encoder information.
- Is easy and intuitive to use with plug-and-play functionality to aid system set-up and calibration.
- Interfaces with the optional ADT View computer software. ADT View can be used to update the ADTpro-100 firmware.
Discover our range of open optical encoders designed to meet your industrial automation needs.