Toolkit for blade engineering and manufacturing
Renishaw's blade inspection process utilises MODUS™ Blade planner software to program the REVO® system's sweep scanning routine and MODUS™ metrology software for data manipulation and analysis of the entire blade.
Combining the capability of MODUS™ Blade planner, SurfitBlade™ and MODUS™ metrology software, Renishaw's Blade Toolkit breaks through the limitations of standard measurement techniques for airfoil components.
Traditional methods determine the inspection of aerospace blades in a limited number of cross-sections. However, REVO 5-axis measurement system's sweep scanning technology enables you to accurately and quickly measure and evaluate the whole blade, collecting and analysing high-precision tactile probing data of an unlimited number of sections.
Using the Blade Toolkit
The first step is using MODUS Blade planner software to automatically generate a collision-free sweep scan program for the REVO 5-axis system, which is then run on the CMM using MODUS metrology software.
The sweep scan operation produces an accurate point cloud that covers the entire airfoil surface. Using MODUS point cloud sectioning functionality, it is possible to generate sections wherever required.
As the complete data set is stored, additional sections can be created at a later time without having to measure again.
The data collected can then be processed in two ways:
- Inspection
The data is sectioned by MODUS and compared to the nominal CAD model requirements. The analysis results are presented through MODUS reporter, which also produces a defined PDF document for archiving. - Engineering
the data is processed by SurfitBlade to produce a full NURBS surface for use in aerodynamic and stress analysis.
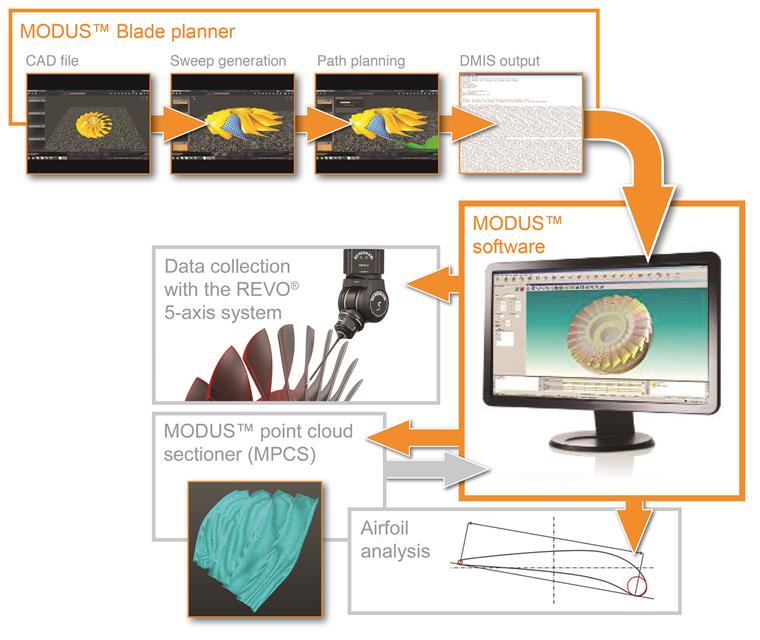