Innovation Matters 2022: From our shop floor
Discover the secrets to successful low‑volume small batch manufacturing.
Welcome to our world. In this interview, members of Renishaw's highly experienced global manufacturing teams will be sharing their expertise. Steve Jay and Antony Spill work across two of Renishaw's world‑class manufacturing facilities in the UK. Their jobs focus on improving manufacturing processes, using innovative solutions to reduce the process development time associated with low‑volume small batch production.
Steve Jay
Job title: Low Volume Production Group Leader
Renishaw site: Miskin
Role: Producing new and low batch size CNC machined parts on short lead times with a wide variety of disciplines, from machining of components ranging from 4 mm to 4 m in size, to additively manufactured parts. Creating production processes for the newest innovations and products under development.
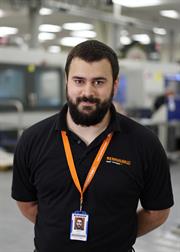
Antony Spill
Job title: Low Volume Production Group Leader
Renishaw site: Stonehouse
Role: Manage the introduction of new CNC machining processes into production with very short lead times and tight timescales. Also focus on improving current processes to ensure efficient methodologies are being used to help hit production and quality targets. Low volume batch sizes range up to a maximum of 300 parts per year and this area is where we also manufacture bespoke custom products.
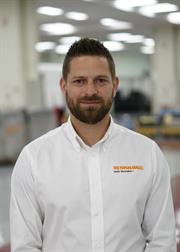
Describe the low-volume machining and piece part manufacturing operations at Renishaw.
Antony Spill: Introducing efficient and ‘low cost of quality' processes is our primary objective. Low volume is a separate entity to our main machine shop to help introduce new processes with very short lead times for custom and low volume products for all areas of the business.
Low-volume production (LVP) machinists are responsible for the complete manufacturing process for new components, from introducing a new CAM process, to setting and running the machines.Typically, we'll create a new process within an eight‑hour shift, which includes using CAM software to create a new piece part program, setting the machine, and manufacturing the piece parts within these tight timescales. To achieve efficient processes with short lead times, we have to ensure our machines are in the best possible condition, which we do by carrying out regular health checks using Renishaw's QC20 ballbar system. We rely heavily on Renishaw products to help maintain healthy machines we know are reliable and can produce correct components first time, every time.
When introducing new components, we focus less time on developing individual processes at the programming stage and more on developing procedures and processes where we know the machine tool is accurate enough to produce correct components every time.
Steve Jay: In 2018, our low-volume operation was expanded out to the Miskin site in South Wales to cater for increasing demand for larger component and additive manufacturing capabilities, along with increasing demand in custom products and specials.
How to maintain machine health
Save on piece part process development and implementation time by investing in the following machine health checks:
- Performance checks: machine calibration, using the QC20 ballbar kit (multiple processes)
- Health check procedure: using an OMP400 spindle probe (on a vertical mill process)
- Error mapping work co-ordinates: using an OMP400 spindle probe (on a mill/turn process)
- Turret-to-turret tool datuming: using an OLP40 probe and stylus assembly (on a mill/turn process)
What are the top three challenges impacting manufacturers today?
Improving efficiency
AS: Introducing innovative ideas to improve departmental efficiencies.
Reducing the cost of quality
AS: Reducing the cost of quality, primarily, by targeting setting scrap in low volume with high set to run ratio.
SJ: The increased size, cost and machining time of the average piece part manufactured at Miskin has highlighted this challenge. Cost of quality is an area we'll continue to improve using a variety of engineering solutions, including in-cycle piece part verification.
Ensuring customer satisfaction
AS: We aim for complete customer satisfaction, whether this is the end user or even the next operation within the assembly process.
SJ: Quite often when we supply parts for the very first time for custom or special products, there's an emphasis on ‘right first time'.
Why is it so important to avoid first off scrap, especially with larger parts?
AS: This comes down to a combination of efficiency and reducing the cost of quality. We can use probing technologies to find the positions of features, and to ensure features are cut to size accurately. Some large components can take several hours to machine across multiple operations, and rejecting a component because a feature is either out of position or not the right size is neither efficient nor cost effective. Introducing simple probing cycles can prevent this and targets key departmental metrics.
SJ: Time and money. As our variety of methods and components continues to grow (literally), it highlights the importance of Renishaw's ‘Productive Process Pyramid' concept. Making constant and conscious enhancements on each of the levels will continue to improve our efficiency and cost of quality.
What's it like working in a Renishaw machine shop?
AS: I'm very lucky to have had the opportunity to work in a variety of roles within Renishaw's machine shop. Without the experiences gained in these different positions, I certainly wouldn't be able to contribute as I do now and share my experiences and knowledge with those around me. This philosophy is shared across the machine shop where the teamwork and knowledge-sharing between everyone is exceptional. We all want each other to do well and be successful.
Our machine shop strategy includes streamlining the number of different machine platforms that we use. A high variety of machine types increases training requirements, which in turn can lead to resource issues that can create bottlenecks and then lead to supply issues. By standardising our machine platforms and processes, we have the flexibility to distribute our knowledge and resources more efficiently. This means that we hit our departmental targets and our employees can switch easily between areas.
Which Renishaw technologies do you enjoy using the most and why?
AS: I love a challenge and uncovering issues where we can pull together to implement a solution. We are solution providers and try to ensure this is instilled into everyone in the team. Finding new and innovative ways to use Renishaw products to improve our department is exciting and challenging, but having this technology at our disposal is invaluable.
A recent example, and probably the most rewarding project I've been involved with to date, involved a machine that was almost classed as ‘fit for the scrap heap'. We used Renishaw technologies to uncover genuine machine issues and implement a robust solution, which has given the machine a new lease of life.
SJ: Our additive manufacturing capability; the technology is brilliant. The way it challenges designers' imaginations, and the way in which we've introduced it as a productive workcentre within the department, is fantastic.
What's the secret to successful low volume manufacturing?
AS: With a very high setting to running time ratio, it's imperative that we adopt quick processes from start to finish. This includes adopting programming methods that give confidence that the machine tool is accurate.
I've been targeting the error mapping of machinery to ensure the first component is correct without adding to the initial process development time. One example of how we've achieved this involved a machine with extremely poor set time performance.
- Complex large mill turn machine with dual spindle, B-Axis and turret.
- This caused multiple position errors in the machine.
- Without knowing these positional errors, it would lead to poor set performance on average of eight hours per set (often more than this) to run small/low-volume batch sizes.
- Inefficiencies on this workcentre were regularly leading to supply issues.
- Implementation of Renishaw's OMP400 spindle probing has allowed us to find positional errors in the machine between axes and help implement an error-mapping procedure.
- This health check is performed bi-weekly to ensure machine positional errors are found and stored in the macros, which are then called back into each new machine set-up incorporated through the machine work co-ordinates.
- This process, along with the additional turret-to-turret tool datuming, means complete accuracy between all the machine's axes – error mapping the machine.
- Average set times have now been halved and the impact on savings, in terms of production time and cost of quality, is extremely rewarding.
SJ: Although the first question in every machinist's mind is ‘how do we machine this?', making a conscious effort to consider the component or feature verification can often lead to a completely different method. Piece part orientation and work holding, for example. Finding a way to verify the piece part in-cycle, knowing the part or a potentially troublesome dimension is correct before we open the machine door is a priceless capability.
Dave Miles
Job title: Manufacturing Engineering Manager
Renishaw site: Stonehouse and Miskin
Renishaw has seen continued growth and a hugely diverse product portfolio since forming in 1973. Working in the manufacturing services division over the last 20 years has provided many different experiences and problems to solve. It is a pleasure to work with a team who are passionate, driven and push the boundaries to continually improve our manufacturing processes.
Steve Roberts
Job title: Machine Shop Manager
Renishaw site: Stonehouse and Miskin
“In my 30+ years at Renishaw, I've seen manufacturing services change beyond all recognition. Expanding across multiple sites, becoming a manufacturing industry leader, with world class factories and facilities. I am privileged to work as part of a dedicated and skilled team to meet the daily challenges of production. Striving to meet deadlines to deliver customer orders, and continuously looking for opportunities to expand and progress our engineering knowledge and processes.”
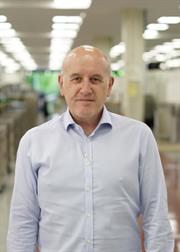
Renishaw's Miskin and Stonehouse facilities
Our operations
- Multiple machining processes, including: Renishaw's Automated Milling, Turning and Inspection Centre (RAMTIC) system for manufacture of prismatic components; Millturn machines for one-hit manufacture of medium parts; sliding head lathes for small turned parts; and various low-volume batch production machines.
- Various inspection processes, such as in-cycle gauging systems through to fully automated CMM inspection.
- Process finishing operations, including anodising, laser engraving and deburring, grinding processes for cutting tool manufacture and laser cutting.
- Assembly facilities for styli, additive manufacturing and encoder products, as well as automated surface mount electronics assembly lines (Miskin).
What we make
- The manufacture of parts for all Renishaw products is managed across both Stonehouse and Miskin, using similar processes across the sites for flexibility and contingency.
- From parts for smaller probes, such as TP20 and OMP40, to larger products, such as the REVO® 5-axis measurement system measuring head and RenAM 500Q additive manufacturing system.
The Renishaw products we use
- Across our machining platforms, there are multiple applications of Renishaw machine tool probes for tooling/part set-up and component inspection, including OMP40, OMP400, RMP60, RLP40, NC4, TS27R, MP250 and various tool setting arms.
- Machine calibration and process foundation is carried out with Renishaw calibration products, such as the QC20 ballbar, XL-80 laser system and AxiSet™.
- Final component gauging and inspection is performed by either Equator™ gauges, or CMMs using probe systems such as PH10, SP25, TP20 and MODUS software.
Miskin, Wales
Demonstrating future smart factory concepts with current technology
Size: 460,000 sq ft
Personnel: 550
Stonehouse, England
One of the UK's most efficient precision engineering operations
Size: 100,000 sq ft
Personnel: 220